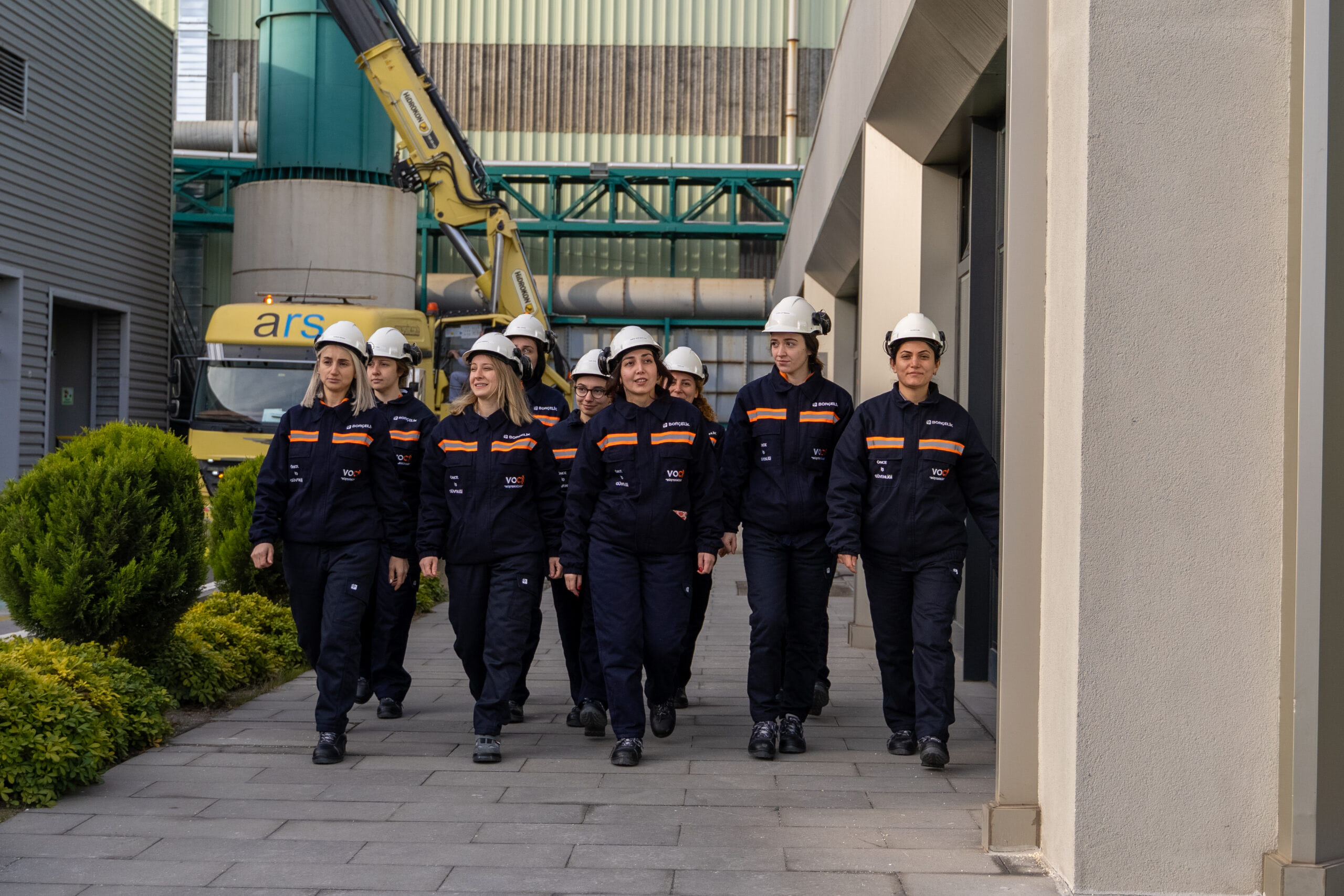
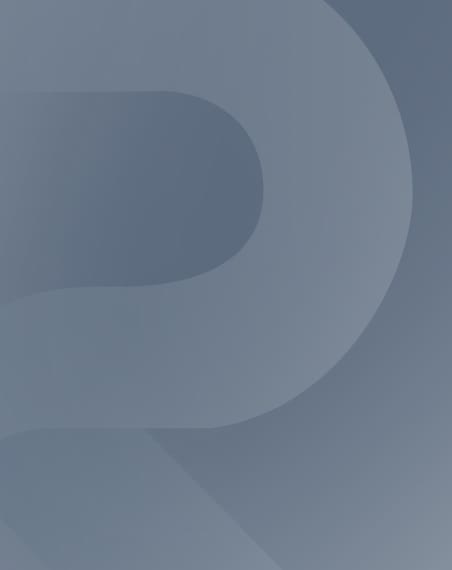
Borçelik: Our Greatest Strength
“We see our human resources as our greatest strength.” Worker well-being is a crucial part of creating a sustainable industry. This means not only ensuring a healthy and safe working environment, but also providing the care, opportunities, and respect that every individual deserves and needs in order to thrive. Derya Demirer, Director of Human Resources and Corporate Communications for Borçelik, discusses the strides the company is making to promote equality, support professional growth, and put worker well-being first.
Borçelik, a special collaboration between Borusan Group, a leading conglomerate in Turkey, and ArcelorMittal, the world’s largest steel producer, proudly stands as Turkey’s biggest galvanized flat steel producer. We wholeheartedly embrace and endorse Borusan Group’s sustainability vision, which revolves around three key pillars: climate, people, and innovation. At Borçelik, we integrate initiatives aligned with these focal points into our core business operations, ensuring a holistic and responsible approach to our endeavours.
The Borçelik Technical Academy (BTA), established with the aim of supporting the professional development of Borçelik employees, is deeply committed to creating value for society. It welcomes individuals who are eager to enhance their expertise in the fields of metal, machinery, transportation, logistics, communication, chemistry, petroleum, rubber, and plastics. Moreover, BTA dedicates itself to designing a unique curriculum for technical high school students, empowering students to become highly skilled professionals and promoting diversity in the industry.
Gender equality holds immense significance for us at Borçelik. We are proud to lead the way in introducing innovative initiatives for our industry in Turkey. One such initiative is our “No Job Too Tough for Women” project, implemented in collaboration with the BTA, which establishes a comprehensive programme to enable female employees to work in the predominantly male-dominated steel industry.
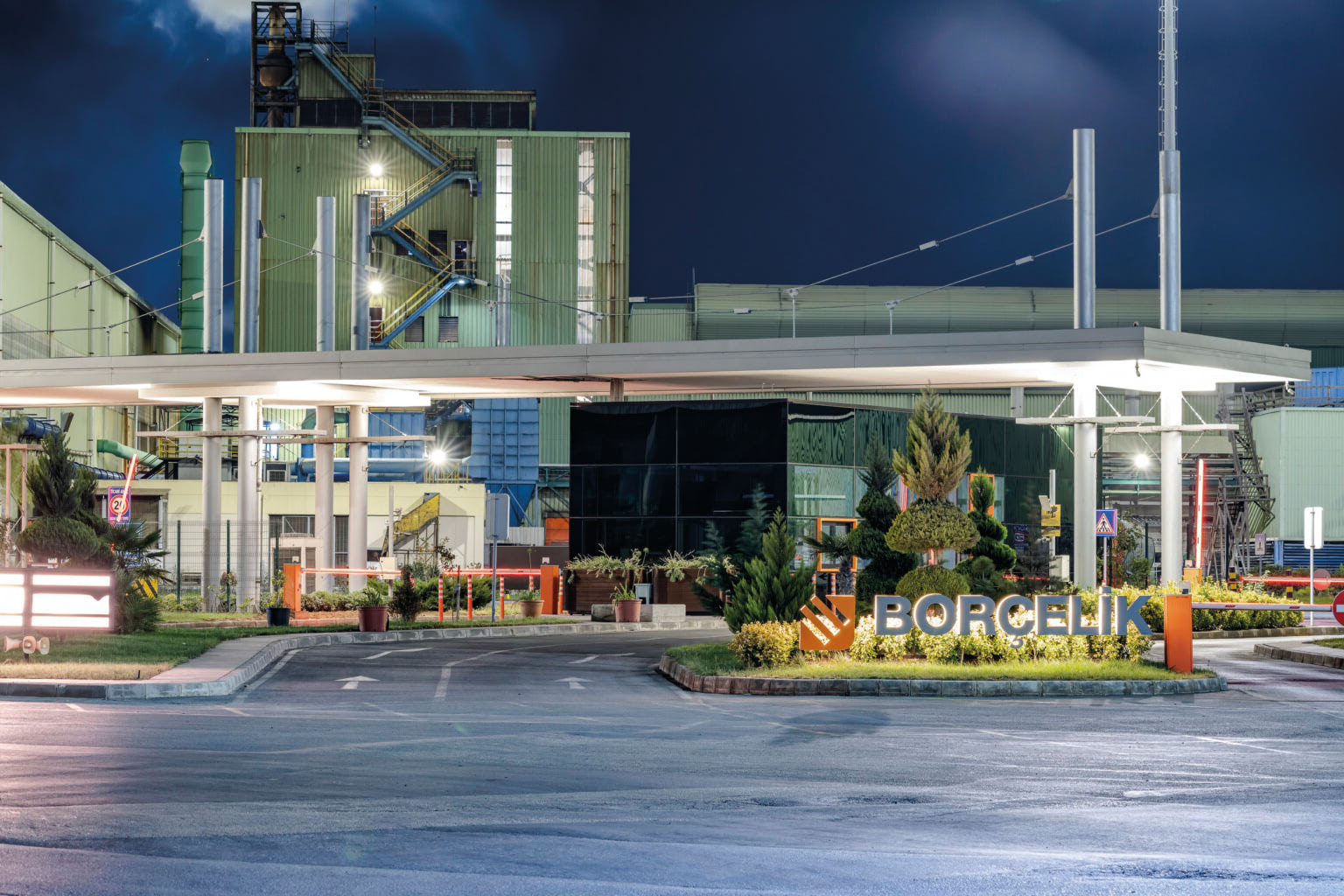
Furthermore, we actively engage in the Gender Lens initiative as a key participant within Borusan Group’s Equal Borusan Platform. Through this initiative, we implement a wide range of practices to foster gender equality. These include offering private health insurance with maternity coverage to both male and female employees, ensuring uninterrupted utilization of maternity and paternity leave, providing support programmes for maternity and postnatal care, granting leave on important occasions like the first day and last day of school for colleagues with children, organizing well-being activities, implementing hybrid work arrangements, and establishing an accessible Ethics Line to report any gender equality violations.
We also offer childcare assistance to our female employees with children aged 0-66 months. Moreover, we engage in the Borusan Equality School project initiated by the Borusan Group, which aims to raise awareness about equality. Through continuous gender equality-focused training programmes, we strive to foster awareness and understanding both within and beyond our company.
At Borçelik, we remain dedicated to our sustainability endeavours, focusing on climate, people, and innovation. We prioritize the well-being of individuals and embrace the concept of “Inspiring the Future by Inspiring the World.” Our dedicated efforts revolve around fostering the healthiest and safest work environments for our workers. Recognizing our workforce as our greatest asset, we have developed comprehensive programmes to enhance their competencies and promote their overall welfare. Central to our approach is the utilization of cutting-edge technology to continuously improve working conditions and establish a secure atmosphere within our facilities.
Through innovative solutions, we strive to create a workplace that ensures the safety and satisfaction of our employees. We are committed to conducting inspiring projects that set the benchmark across the industry.
By Derya Demirer, Director of Human Resources and Corporate Communications, Borçelik
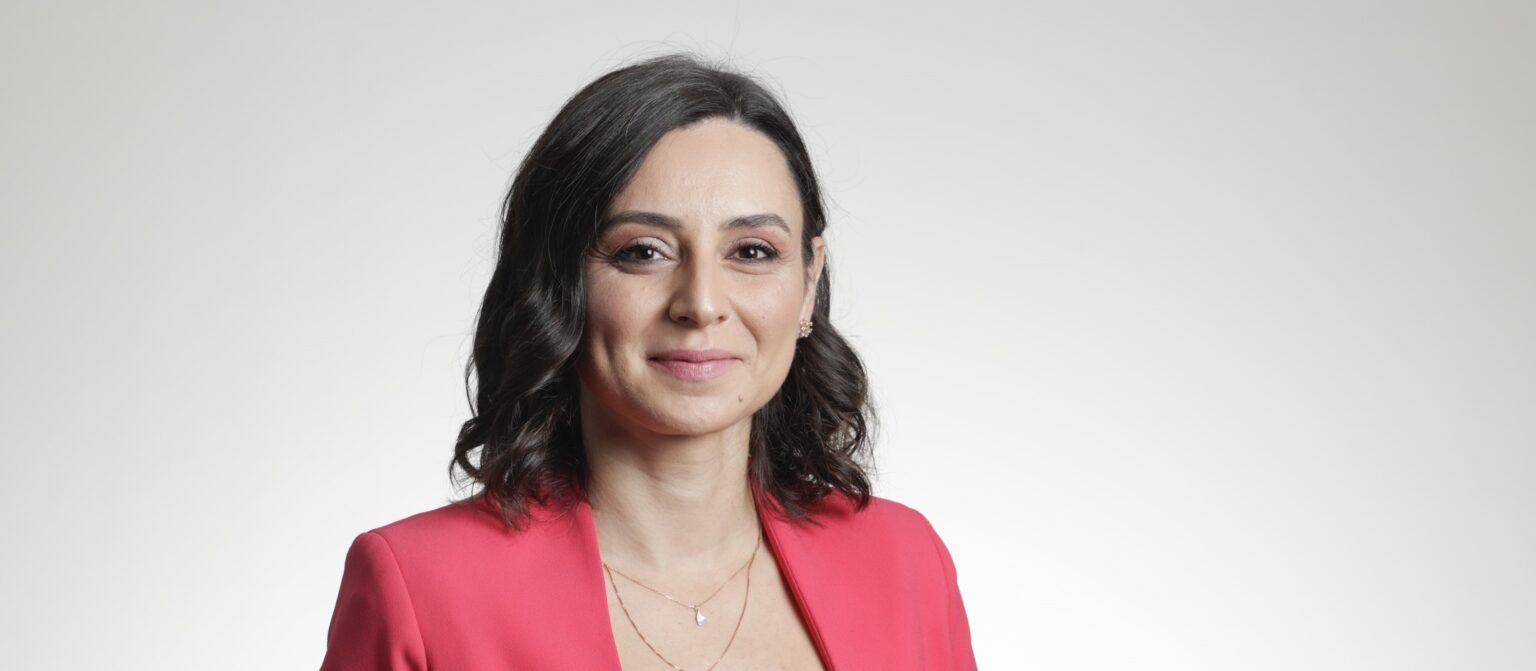
Derya Demirer is an experienced Human Resources Professional who has an undergraduate degree in Industrial Engineering. Her areas of expertise includes performance management, talent and career management, organisational design and diversity and inclusion studies. She is currently working for Borçelik as Human Resources and Corporate Communications Director.
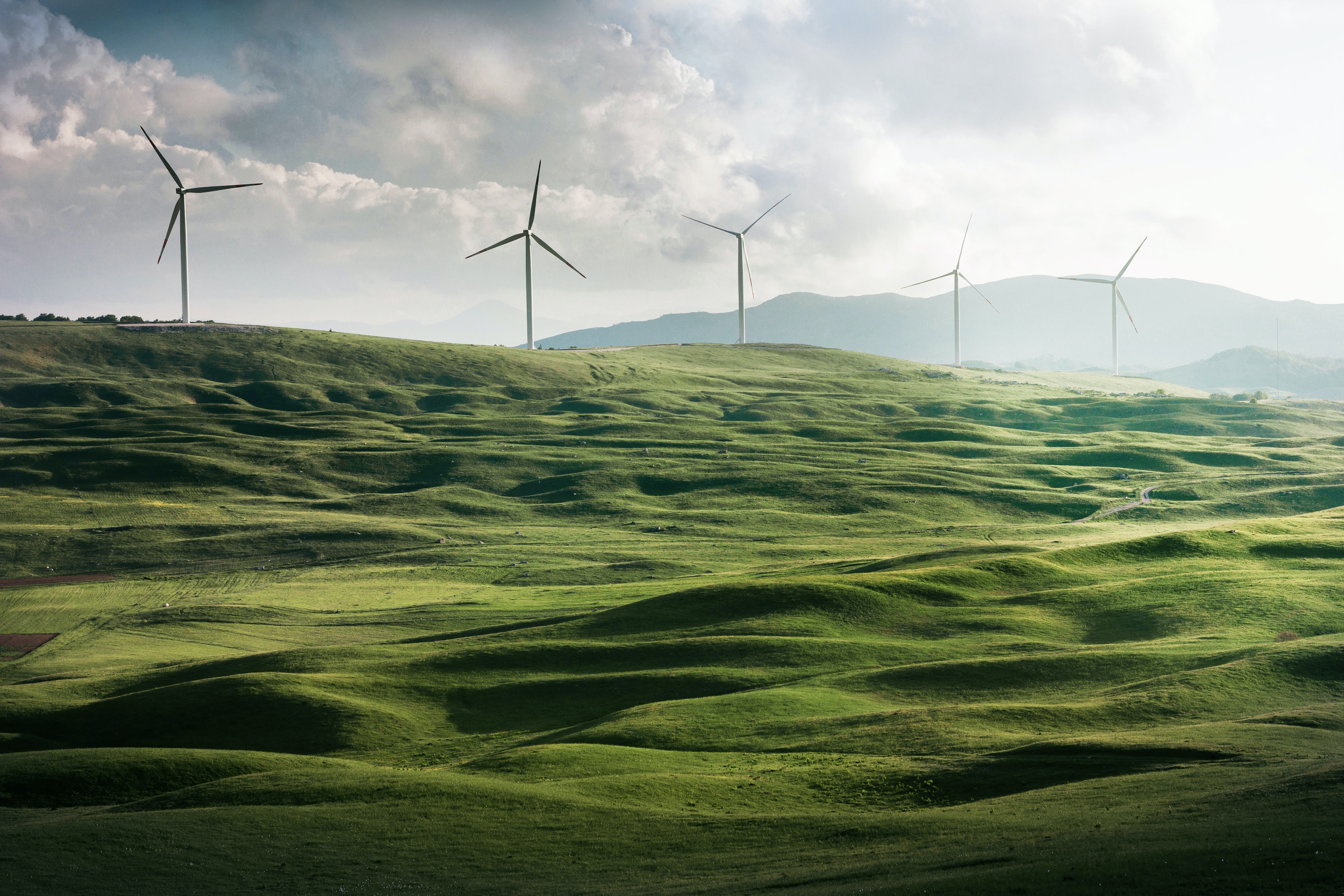
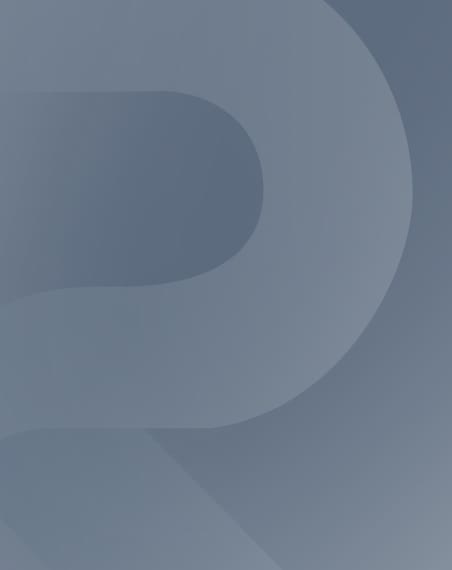
ResponsibleSteel hosting event at upcoming 14th Clean Energy Ministerial in Goa
ResponsibleSteel is hosting a critical meeting at the upcoming 14th Clean Energy Ministerial (CEM14) demonstrating the role of the ResponsibleSteel International Standard in impacting policy, finance and the energy transition to accelerate decarbonisation in India’s steel industry at pace and scale. The event will take place from 9:00 to 10:30 am (IST) on Saturday, July 22nd.
India is the second-largest producer of steel after China and according to the IEA, the Indian steel industry is projected to triple by 2050. Currently, the steel industry accounts for around 12% of India’s emissions. The country’s push to meet its net zero targets will rely heavily on the decarbonisation of its steel sector. That is why ResponsibleSteel will bring together key stakeholders from government, downstream, and the steel industry to discuss the challenges and solutions needed to achieve an equitable and just transition in India.
The event will feature keynotes from Shri. Nagendra Nath Sinha, Secretary for the Indian Ministry of Steel, Shri. Alok Sahay, Secretary General & Executive Head of the Indian Steel Association, and Annie Heaton, CEO of ResponsibleSteel, as well as a panel discussion between representatives from the Ministry of Steel, JSW Steel, and SteelZero.
Topics of discussion will include:
- The main challenges facing the Indian steel industry as it moves to a “greener” future
- The role the ResponsibleSteel Standard and certification programme can play to help accelerate the decarbonisation of India’s steel industry
- The importance of driving alignment on frameworks and near-zero definitions
- The investments, innovations and new policies needed to speed up a decarbonised future
Learn how more about CEM14 and how you can register to join us in Goa here!
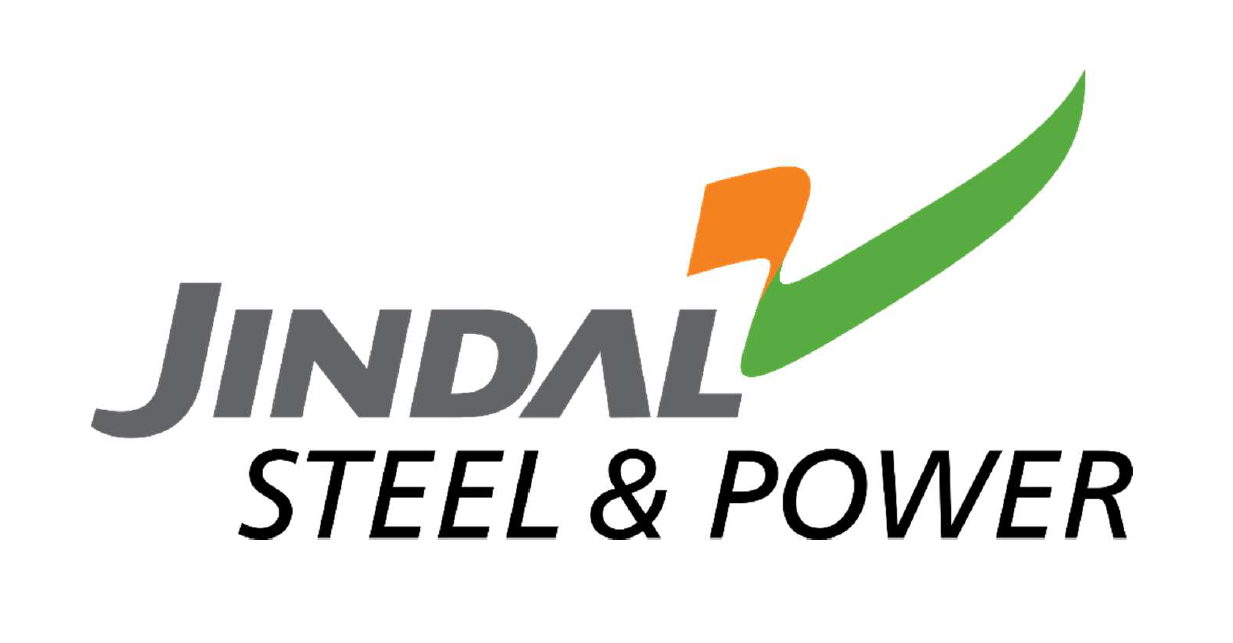
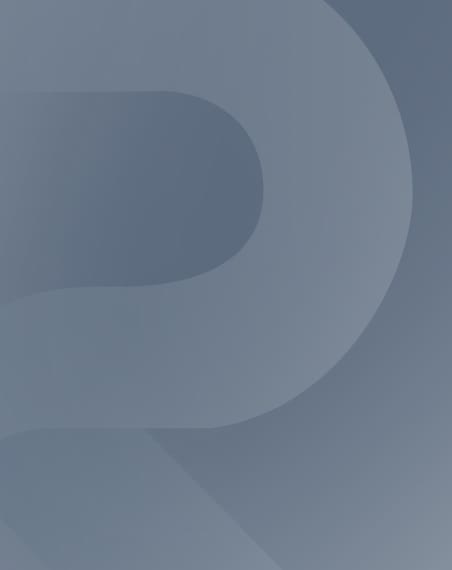
Jindal Steel & Power Joins ResponsibleSteel
Jindal Steel & Power has become the latest steelmaker to join ResponsibleSteel, demonstrating their commitment to our mission to be a driving force in the socially and environmentally responsible production of net-zero steel, globally.
Jindal Steel & Power (JSP) is an industrial powerhouse with a presence in steel, power, mining and infrastructure sectors in India and abroad. Led by Mr Naveen Jindal, the company’s success has been based on overarching goals to promote innovation, set new standards, enhance capabilities, and support company stakeholders.
ResponsibleSteel CEO, Annie Heaton commented, “We’re delighted to welcome Jindal Steel & Power to ResponsibleSteel. This is yet another prime example of the growing commitment of Indian steelmakers to building a more sustainable industry. As one of the largest steel-producing countries in the world, India has a critical role to play in driving steel decarbonisation. With JSP, we now have nearly 40% of India’s steelmaking capacity in our membership. We look forward to working closely with JSP as we continue to accelerate the rollout of the ResponsibleSteel International Standard globally.”
ResponsibleSteel steelmaking members commit to starting the certification process of at least one steelmaking site against the ResponsibleSteel International Standard within one year of joining. As one of the largest steel producers in India with a turnover of more than $7.6 billion, JSP has a significant presence in sectors like mining, power generation, and infrastructure. Through technologies like Coal to Liquid & Coal Gasification, JSP has worked to become a trailblazer and drive innovation in the steel industry.
Mr Bimlendra Jha, Managing Director for JSP stated, “By associating with ResponsibleSteel, JSP has reiterated its commitment to a more sustainable future by incorporating environment-friendly initiatives and technologies. JSP has been an ardent advocate and practitioner of sustainable development since its inception and is wholeheartedly committed to improving its sustainability performance. We aim to incorporate sustainability into our businesses by strengthening our economic, social & environmental pillars by mitigating the impact of our operations.”
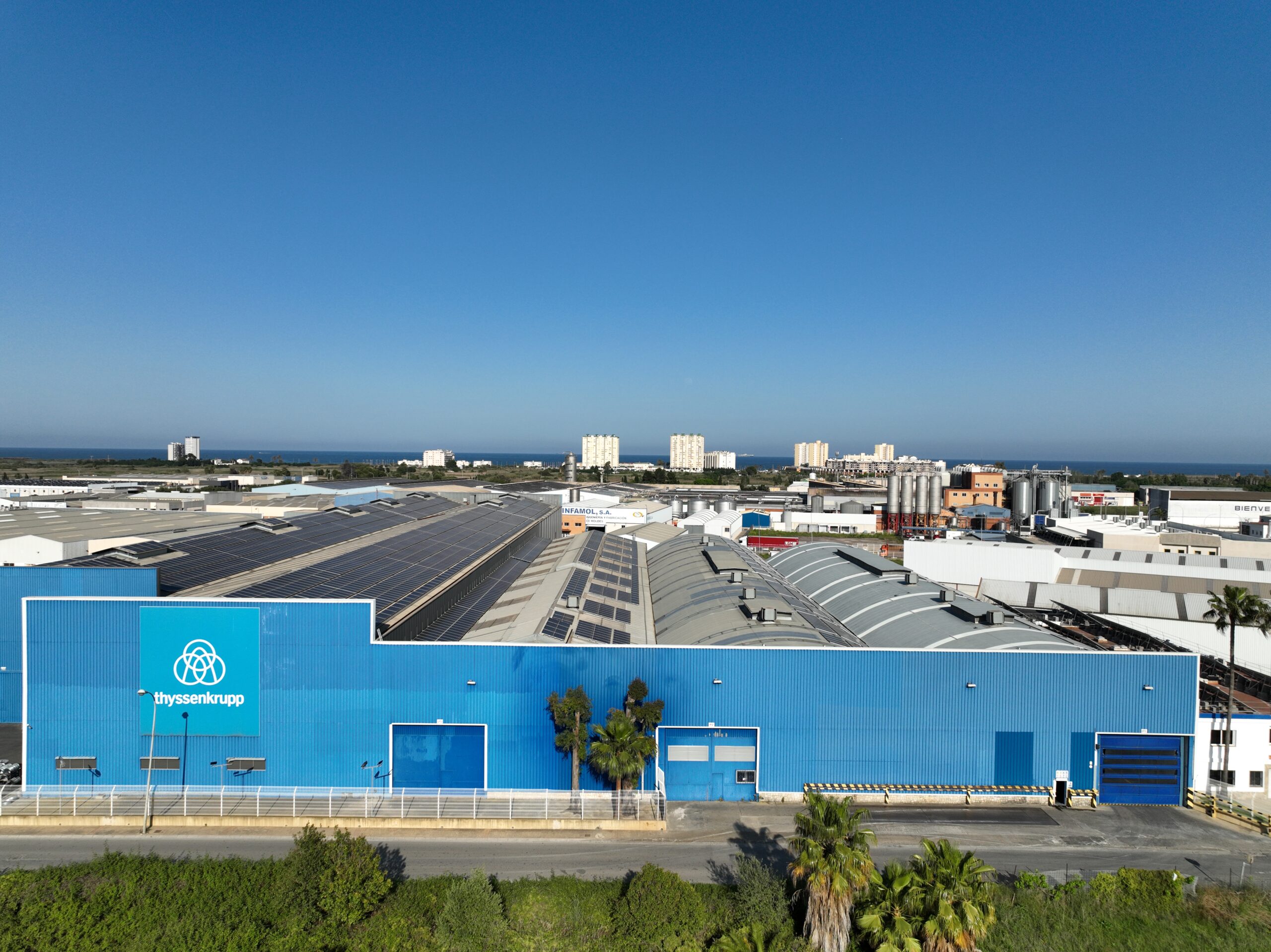
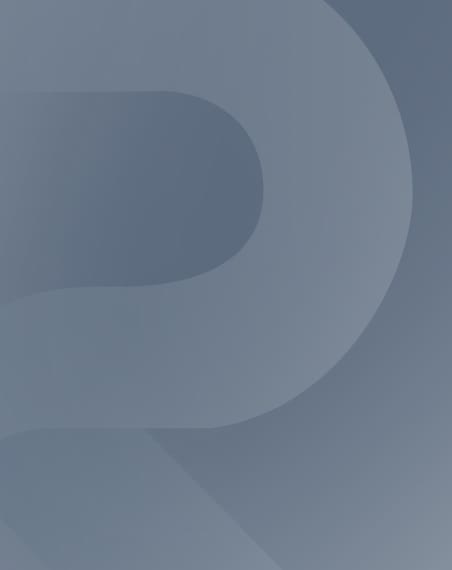
Thyssenkrupp Materials Processing Europe Achieves First ResponsibleSteel Certification
Following an independent audit conducted by DNV, thyssenkrupp Materials Processing Europe’s El Puig site has successfully obtained ResponsibleSteel certification. This is the organisation’s first certification globally and is an unprecedented milestone as the first steel-cutting service centre to obtain the certification.
The El Puig Steel Service Centre was founded in 1989 as a joint venture and has belonged to thyssenkrupp Materials Processing Europe since July 2016. This achievement was the result of a collective effort by the entire El Puig team to fulfil the 12 principles of ResponsibleSteel’s International Standard Version 1.1, covering a wide range of ESG criteria.
Oliver Bensing Carvalhal, CEO of thyssenkrupp Materials Processing Europe S.L, said, “This ResponsibleSteel certification reflects our commitment to our environment as well as acts as a differentiating factor between our competitors and us and endorses our path to a sustainable and decarbonised production process for future generations. It is not an easy task, but this is what responsible management is about, combining economic development, social inclusion, environmental sustainability and transparency to contribute to creating a more sustainable future for people and the planet. This certification positions us as a reference steel cutting service centre worldwide.”
Thyssenkrupp has set targets for 2030 to reduce the sum of its direct emissions (Scope 1) and its emissions from purchased energy (Scope 2) by 30% compared to 2018. Furthermore, the company aims to reduce indirect emissions from its value chain by 16%.
ResponsibleSteel CEO, Annie Heaton, commented: “We’re delighted to have thyssenkrupp’s El Puig site join the growing ranks of ResponsibleSteel certified sites. This achievement, the first for thyssenkrupp Materials, demonstrates their commitment to our mission to drive the responsible production of net zero steel and the importance of managing sustainability impacts all along the value chain. The site has worked to create a culture which promotes worker safety and wellbeing and has made significant environmental strides. Most notably, El Puig has reduced its water consumption rate by 40% and has already made progress reducing emissions, having lowered CO2 emissions by 25.6% between 2017 and 2021.”
Read the public audit summary here.
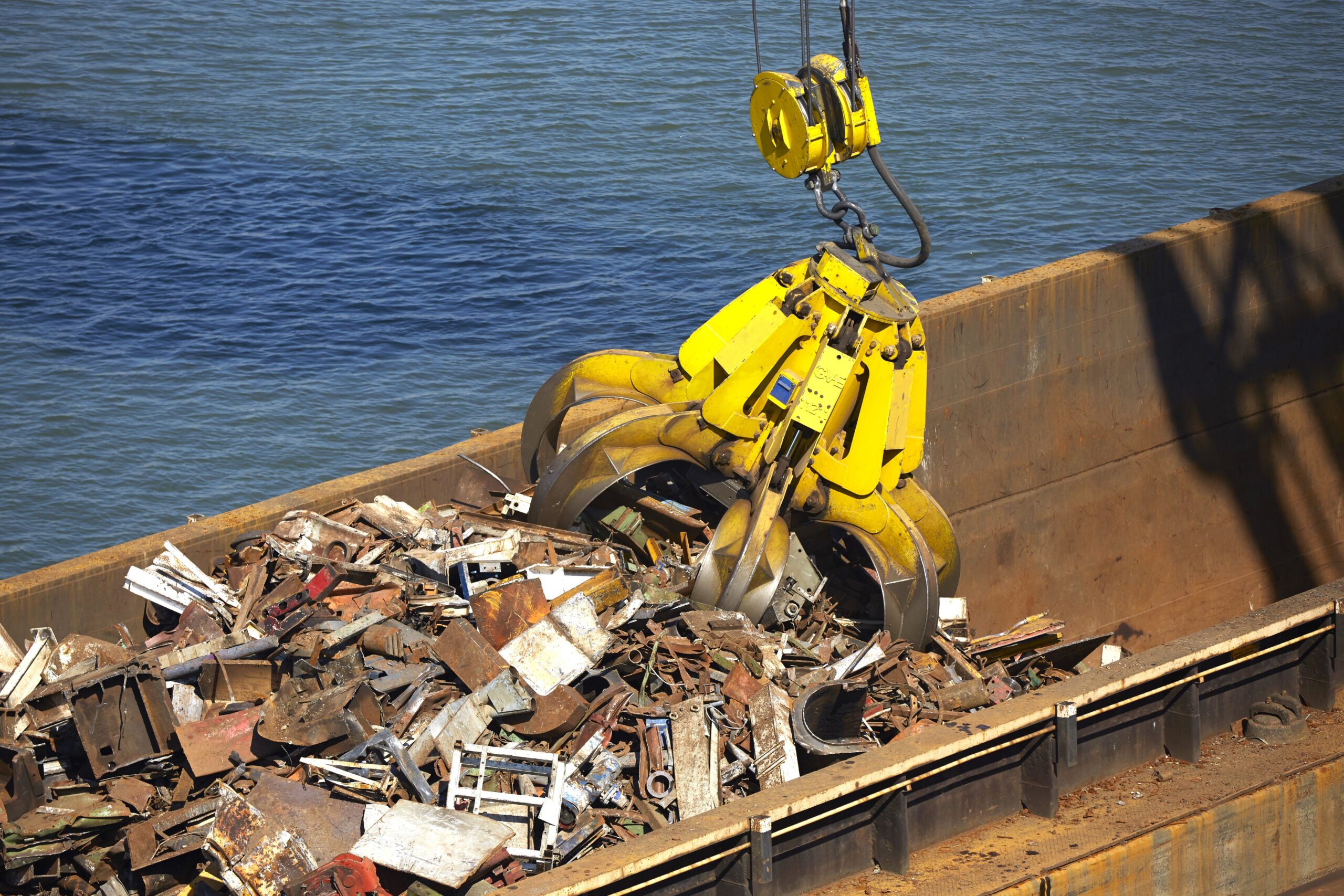
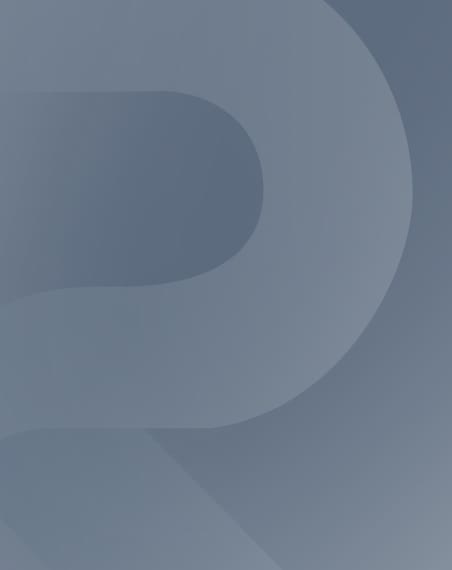
May 2023 Newsletter
Please view the May 2023 newsletter by clicking the link below:
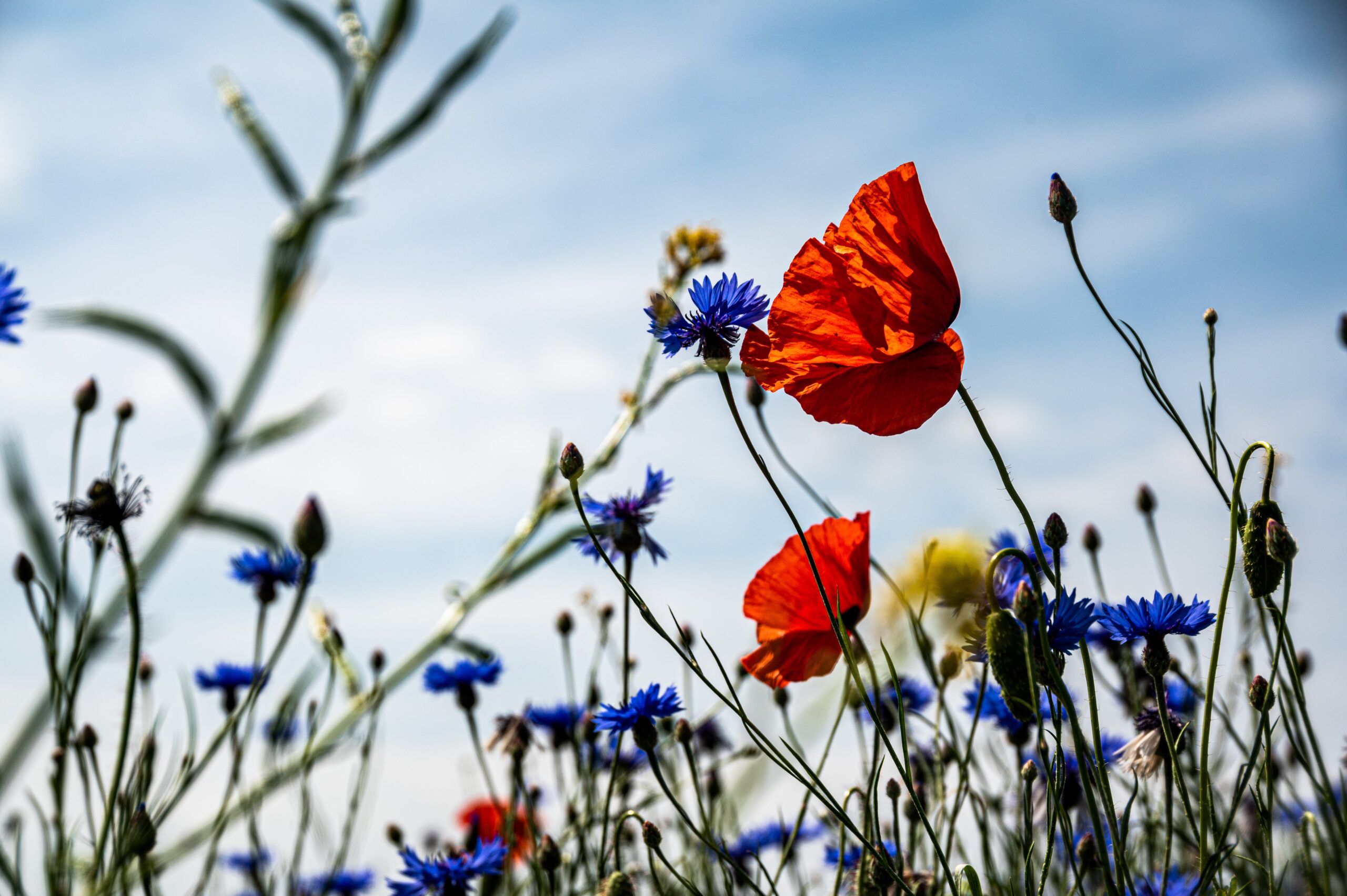
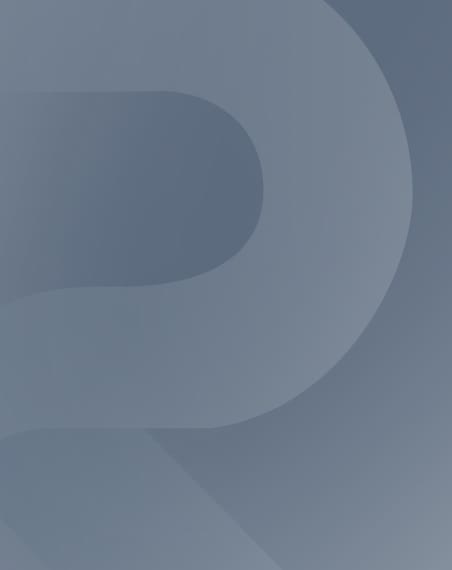
From Commitment to Action: World Biodiversity Day 2023
We face a global biodiversity crisis. Biodiversity losses are running at unprecedented levels with up to a million species facing extinction in coming decades. The maintenance of biodiversity is an important and shared responsibility. That’s why the ResponsibleSteel International Standard requires sites to take stock of the risks and impact they have on biodiversity. Anne Sophie Pellier, Senior Programme Manager at Fauna & Flora and ResponsibleSteel Board Member, discusses how the steel industry is working to protect biodiversity.
World Biodiversity Day 2023 feels very significant. We are riding on a new wave of optimism with the adoption of the Kunming-Montreal Global Biodiversity Framework, setting out a goal to halt and reverse nature loss by 2030 – putting nature visibly and measurably on the path of recovery.
This comes at a critical time. We understand nature’s vital contributions to our planet and to society, and its interconnections with climate change. Yet nature is under threat like never before. Biodiversity loss stands in the World Economic Forum’s top five global risks, reflecting the potential for significant negative impacts for humanity within the next 10 years; for our food, water, economy, health and well-being.
We must act together and swiftly, putting nature loss on a par with climate change and aligning our new goal for nature with the net-zero Paris Agreement. If we fail to do so, the consequences will be catastrophic.
The business community is critical to this; not only due to the scale of its impact, but because biodiversity loss directly translates into business risk. Loss of ecosystem resilience, reputation damage and supply chain disruption can all have an impact.
Fauna & Flora: Why we value our membership of ResponsibleSteel
Fauna & Flora is a nature conservation charity protecting the diversity of life on Earth; for the survival of species and habitats, the planet and people. We have a long history of working with businesses, supporting them to put biodiversity at the heart of decision-making.
Being a member of ResponsibleSteel enables us to come together with other stakeholders to influence the industry’s commitment to biodiversity and help drive the development of the standards necessary for sector-wide change.
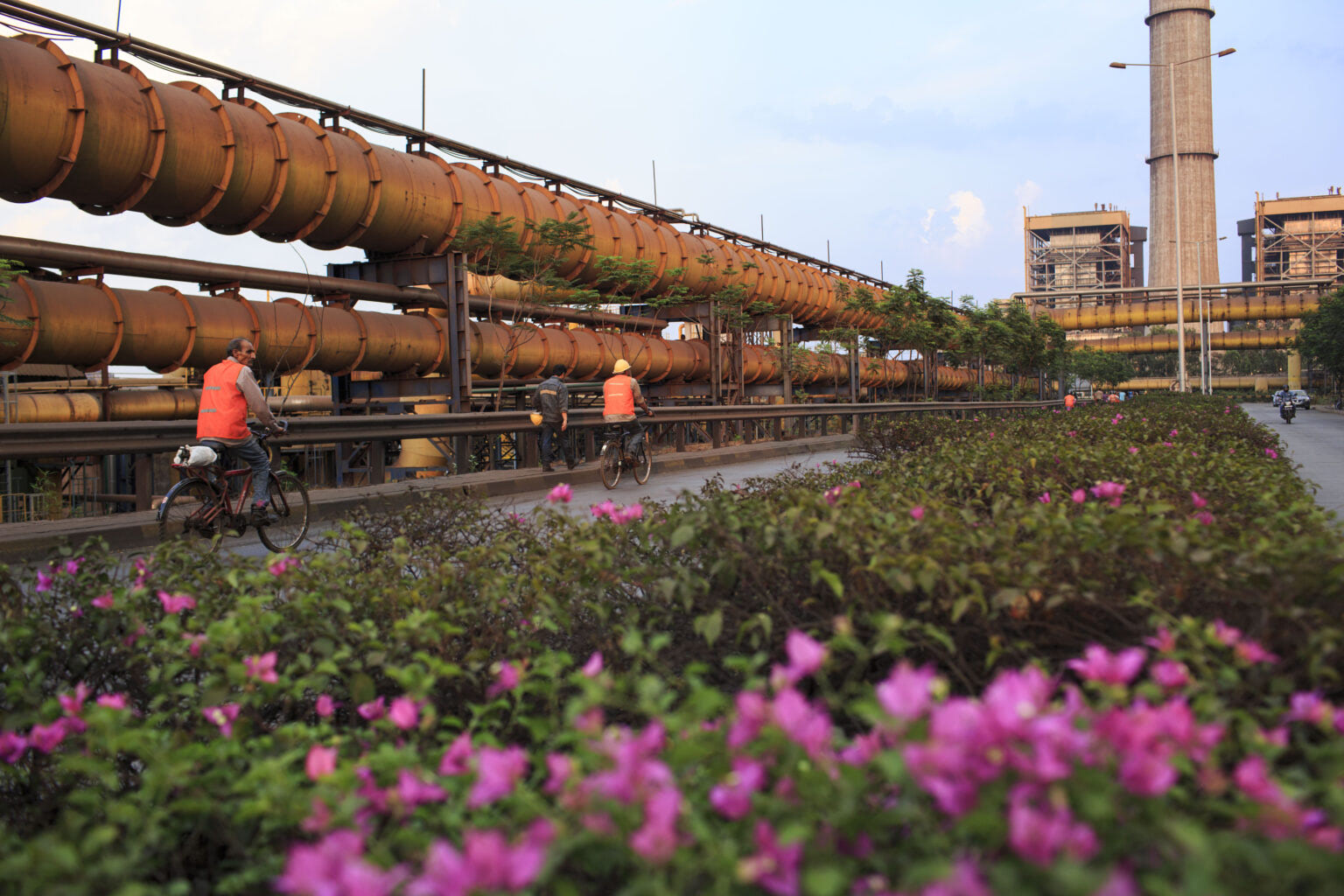
We are encouraged by the significant steps the industry is already taking to protect nature. At an operational level, steel companies are developing biodiversity plans, aiming to minimise negative impacts on biodiversity and to restore sites no longer used. Some are investing in reforestation and habitat restoration projects locally to offset residual impacts on biodiversity, and are seeking to reduce their supply chain impacts through the sustainable sourcing of raw and recycled materials.
As companies invest in reducing their carbon emissions and transitioning to more sustainable energy sources, this also brings positive benefits for biodiversity. In addition, we’ve seen how some are engaging in sectoral and company-specific partnerships, to share good practice and create consistency across the industry.
Achieving our 2030 ambitions for nature: what next for the steel industry and biodiversity?
If the steel industry is to build on this progress and continue to push boundaries, companies need to further integrate biodiversity into core business practices, and commit to becoming nature positive. Companies need to go beyond mitigation and identify opportunities to invest in habitat restoration where mining has caused damage, and to support conservation initiatives in regions of high biodiversity value. Importantly, companies must be transparent about their impact on biodiversity and support progress towards conservation goals.
If we are to spearhead the transformational change so urgently needed, companies should use their influence to engage and educate employees, customers and other stakeholders on the importance of protecting and restoring nature and the role they can play.
If we are to reverse nature loss at the scale and pace needed, progress should be underpinned by collaboration – with other businesses, government, civil society and local communities – to exchange knowledge and identify solutions to our shared challenges.
By Anne-Sophie Pellier, Senior Programme Manager in Corporate Sustainability, Fauna & Flora
Anne-Sophie Pellier works in partnership with businesses to bring about positive change for biodiversity, providing them with best practices for avoiding and mitigating their impact on nature’s assets. She has worked in biodiversity conservation and sustainable development for local communities for 13 years in Southeast Asia, Latin America and Europe, during which she developed her expertise on ecosystem services and natural capital. She joined the ResponsibleSteel Board in 2022.
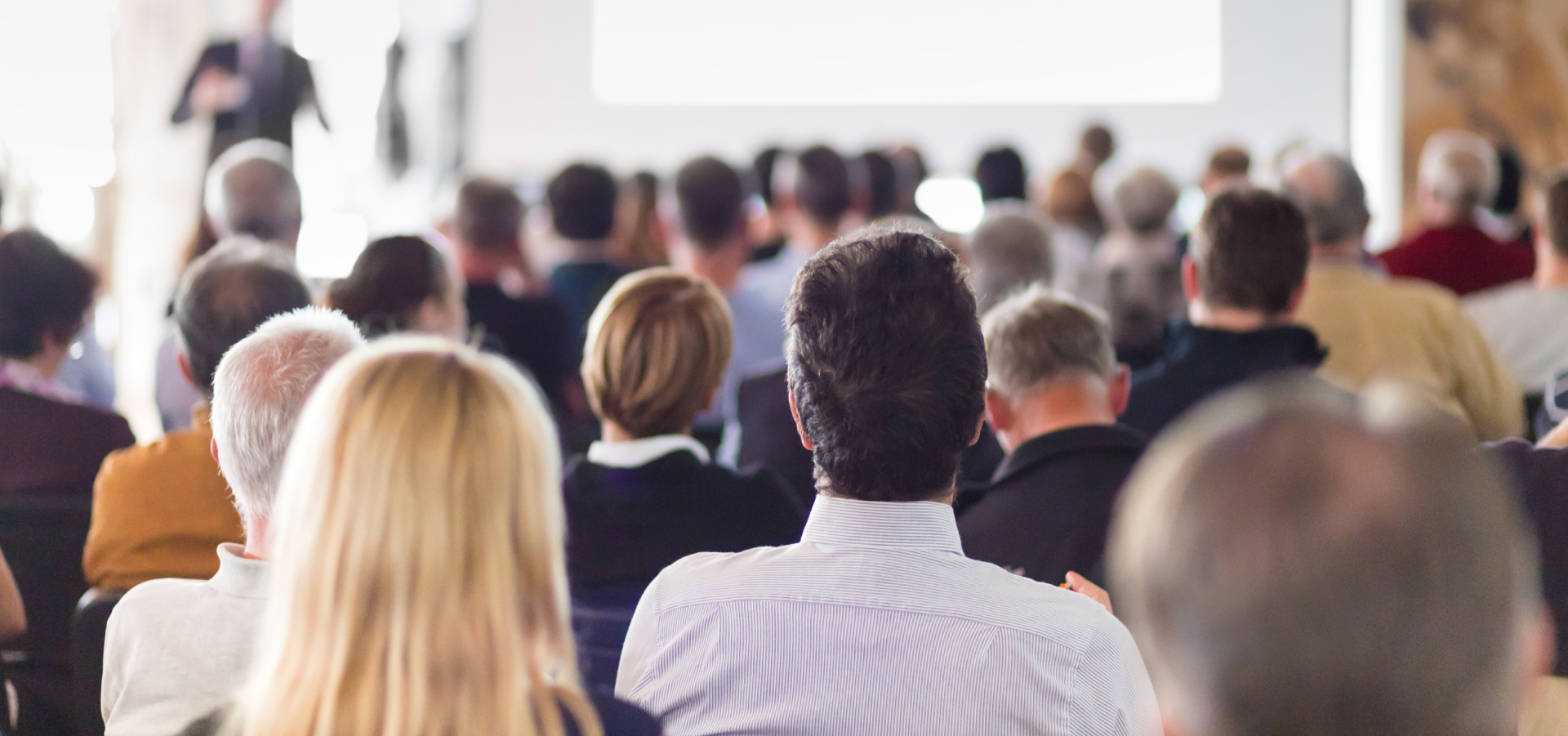
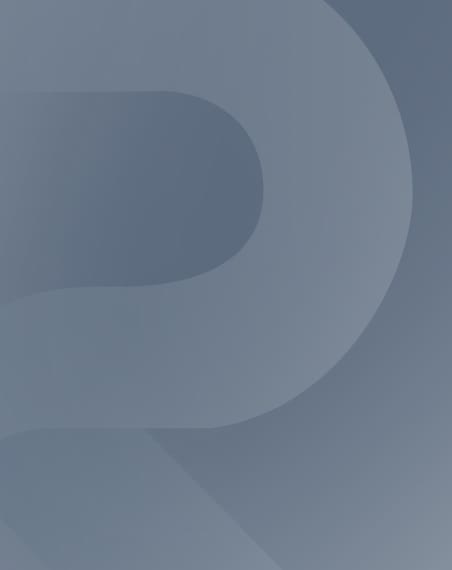
New ResponsibleSteel 'meet the expert' webinar series
We're delighted to invite members to the first two in a new series of ResponsibleSteel’s ‘Meet the Expert’ webinars.
Our series will kickoff on Friday, May 26th with a deep dive briefing by the International Energy Agency (IEA) industrial decarbonisation team on the latest IEA report to the G7 on ‘Emissions Measurements and Data Collection for a Net Zero Steel Industry.’
Webinar: Emissions Measurements and Data Collection for a Net Zero Steel Industry
Date: Friday, May 26th
Time: 7:30 EDT (NYC)/ 12.30 BST (London) / 20:30 JST (Tokyo) / 21:30 AEST (Melbourne)
In addition, the World Steel Association (worldsteel) will share their plans to review their own CO2 methodology, and ResponsibleSteel CEO Annie Heaton will outline ResponsibleSteel’s work on furthering GHG alignment as part of the Steel Breakthrough Agenda.
This webinar will be an exclusive opportunity for ResponsibleSteel members to hear from the IEA, worldsteel, and ResponsibleSteel on building a robust, globally aligned framework for measuring progress towards a net zero steel industry.
Our second member-only webinar on Tuesday, May 30th in partnership with the International Labour Organization (ILO), will explore labour standards in the steel industry, particularly the implementation of the ResponsibleSteel International Standard across different labour contexts.
Webinar: Labour Rights and the ResponsibleSteel International Standard
Date: Tuesday, May 30th
Time: 8:00 EDT / 1:00 BST / 14:00 CEST / 17:30 IST / 21:00 JST / 22:00AEST
Representatives from ArcelorMittal Brazil and Borçelik will also join to discuss potential challenges to implementing the Standard which is based on the ILO Core Conventions.
This webinar will be an exclusive opportunity for ResponsibleSteel members to hear from the ILO, ResponsibleSteel and two ResponsibleSteel members on the importance of ensuring robust labour standards in the industry and the role the ResponsibleSteel Standard plays in this.
Both webinars will include Q&A sessions following the speaker presentations and ample opportunity for a broad and dynamic discussion with members.
If you are interested in participating please contact us.
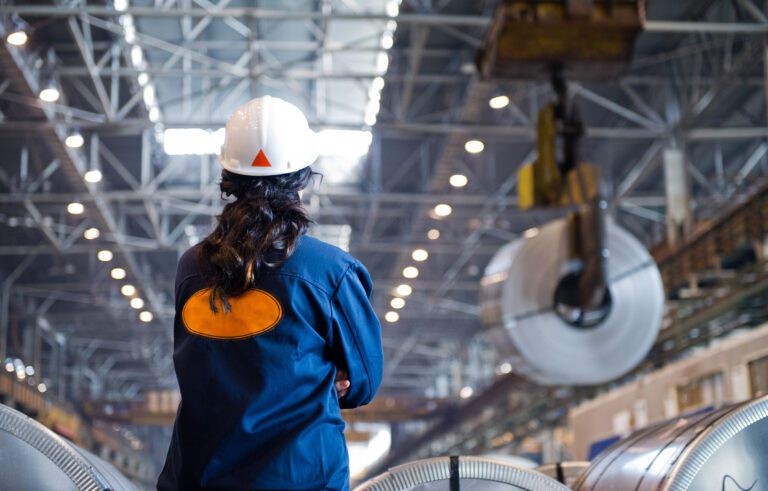
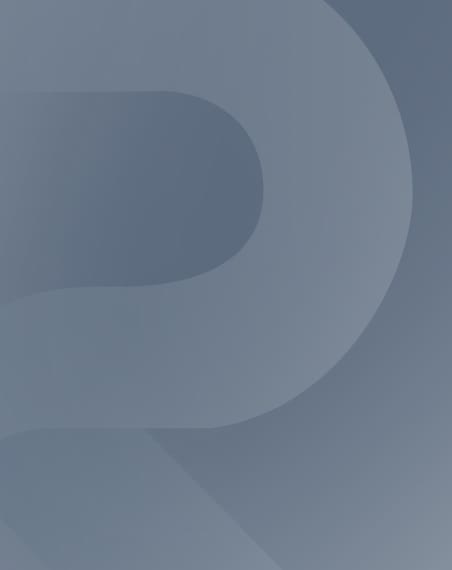
Working together to ensure the health and safety of workers in an evolving steel industry
Industrial processes can be inherently hazardous, and when accidents or work-related illnesses occur they can have serious consequences. Consequently, the first priority of any steel site should be the health and safety of workers. That is why Occupational Health and Safety is a crucial component of the ResponsibleSteel International Standard. Patrick Correa, Director for Base Metals and Mechanical Engineering for IndustriALL Global Union, discusses how we must work together to continue to ensure the health and safety of workers in an evolving industry.
The Global Day for Safety and Health at Work is an opportunity to raise awareness about the importance of workplace safety and health for employees across all industries, not least in the steel sector, where workers face a variety of hazards and risks.
Steel production is a complex and demanding process that involves exposure to high temperatures, heavy machinery, hazardous chemicals, and other physical and environmental hazards. Steelworkers face a range of potential health and safety risks, including burns, cuts, respiratory problems, hearing loss, and more.
To address these risks and promote a safe and healthy workplace for all, robust occupational health and safety (OHS) measures are essential. This can include implementing safety protocols and guidelines, providing training and education on workplace hazards, conducting regular safety inspections, and ensuring workers have access to appropriate personal protective equipment (PPE).
Unions play a key role in advocating for health and safety. By joining a union, workers can leverage collective bargaining power to negotiate for safer working conditions, better PPE, and other crucial protections.
But despite improved OHS in the sector, increasing automation, changing job requirements, evolving health and safety risks and a lack of investments from companies to ensure adequate OHS policies and resources, pose new challenges.
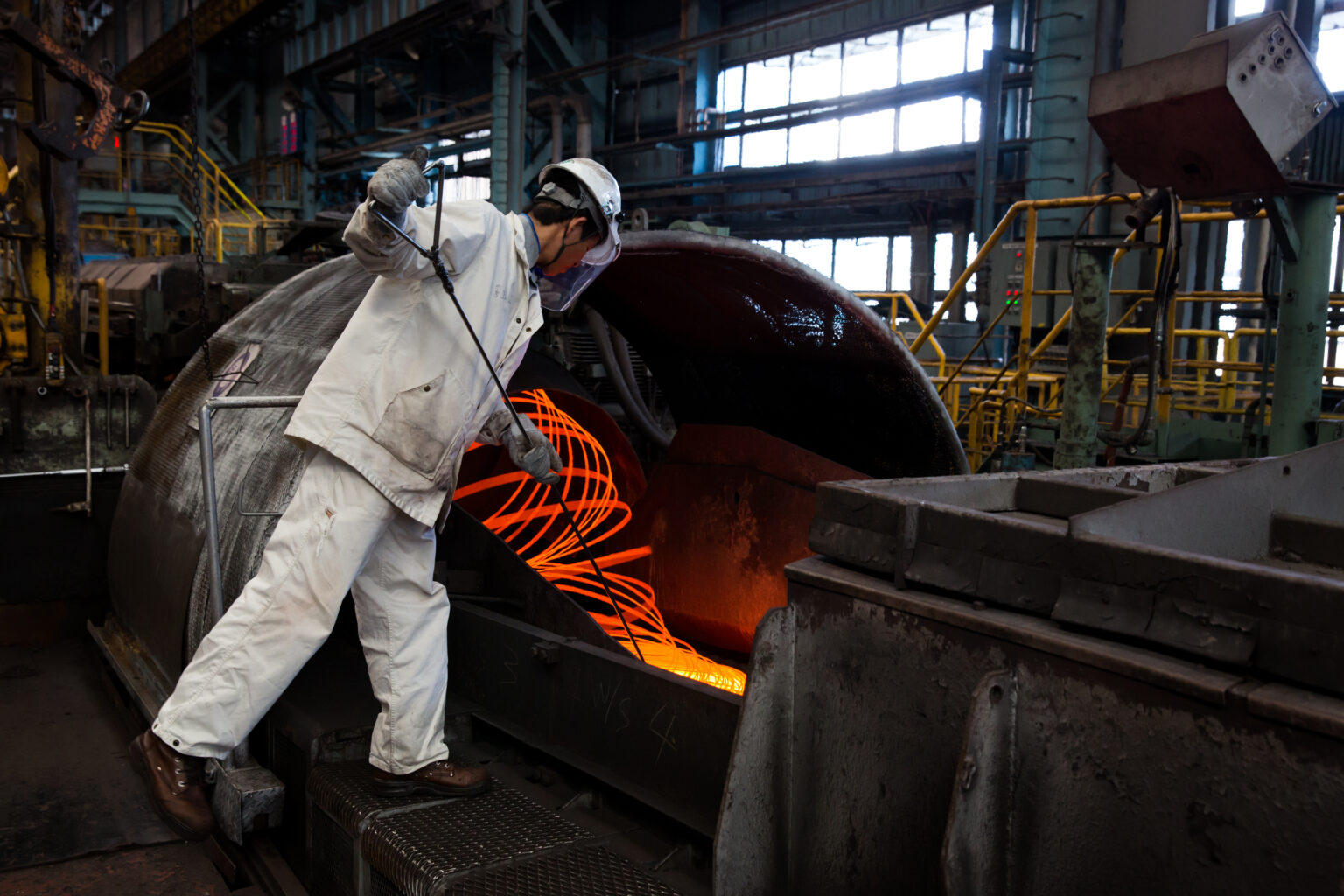
As more tasks become automated, the nature of steelworkers’ jobs will change and with that, the risks and hazards they face. Unions and employers must work together to identify and address emerging OHS concerns, like potential risks associated with robotic machinery.
As our understanding of workplace hazards and their impact on worker health and well-being continues to evolve, it is critical that OHS measures keep pace. This means that workers, unions, and employers must remain vigilant and proactive in identifying and addressing emerging risks, such as those associated with new chemicals or materials.
The Global Day for Safety and Health in the workplace is an important reminder of the critical importance of occupational health and safety in the steel sector. By promoting robust OHS measures together with the unions and addressing emerging challenges and opportunities, we can ensure a safer and healthier workplace for all steelworkers.
By Patrick Correa, Director for Base Metals and Mechanical Engineering, IndustriALL Global Union
Patrick Correa has worked in international trade unionism for 25 years, including as International Director of the CGT Métallurgie in France. He has been a member of the executive committee of IndustriALL Global Union and IndustriALL Europe and European trade union coordinator for Renault, GE Power, Engie, Nexans and Lisi. Patrick has a Master 2 degree in labour law from the University of Paris II Pantheon-Assas.
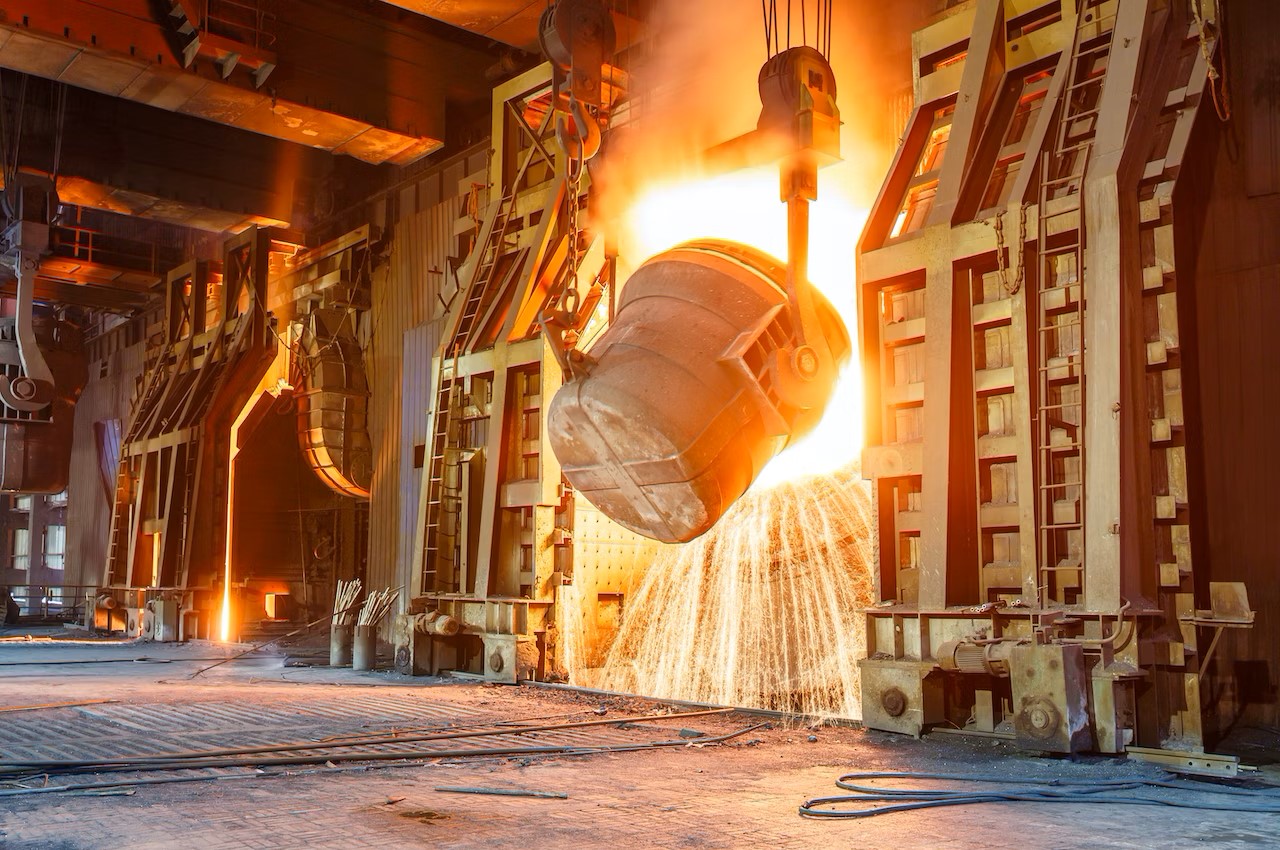
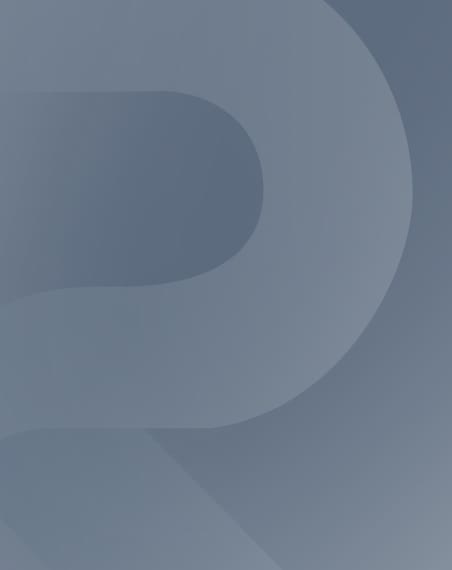
April 2023 Newsletter
Please view the April 2023 newsletter by clicking the link below:
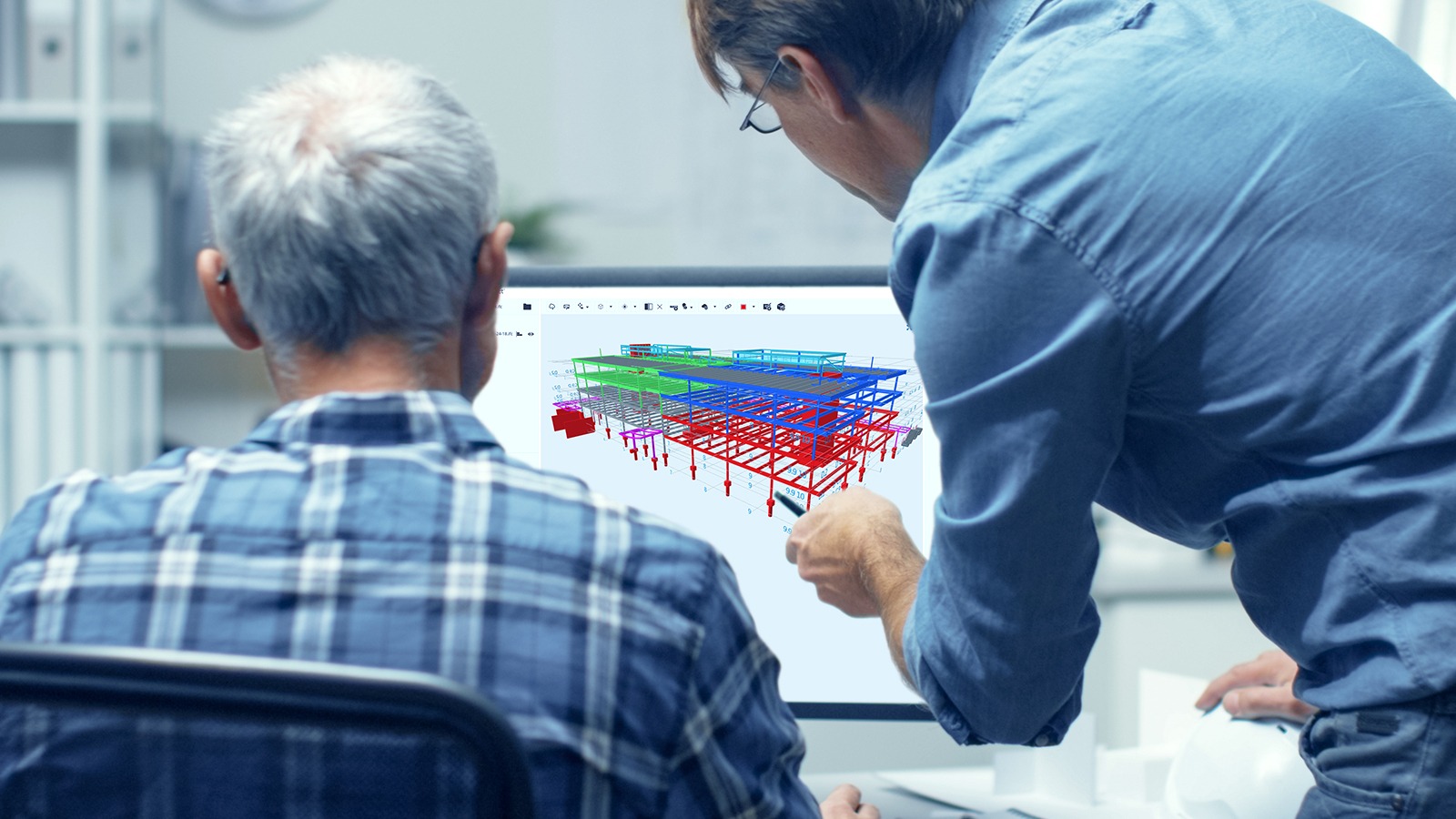
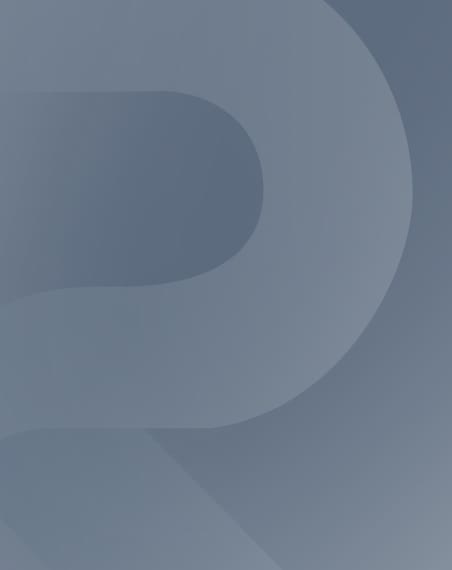
Collective Creativity will Strengthen Sustainability
The United Nations designated 21 April as World Creativity and Innovation Day, citing that the “concept of creativity is open to interpretation, from artistic expression to problem-solving in the context of economic, social and sustainable development.” Dietmar Grimm, Vice President of Corporate Strategy & Sustainability Solutions for Trimble, discusses why we urgently need to capitalise on today’s innovations to drive future change.
Now, more than ever, creativity and innovation are needed to accelerate efforts to achieve the UN’s Sustainable Development Goals (SDGs). Trimble is committed to ensuring that our mission, solutions, and initiatives align with and support the objectives of the SDGs. And joining forces with industry initiatives like ResponsibleSteel underscores that alignment.
Innovation has always been and always will be at the heart of Trimble. For almost 50 years, the company has pushed the boundaries of technology to help our customers work better, faster, safer, cheaper, and greener across the industries we serve. These are not separate goals, but actually five, highly intertwined principles. Trimble’s contribution toward helping customers operate more efficiently enables them to operate more sustainably. Examples include reducing idle time on machinery, lowering fuel consumption and emissions and reducing construction waste – all through data driven insights and decisions.
In the world of steel, our design software has enabled some of the most intriguing and intricate designs for buildings, bridges, and other structures. Technology provides endless possibilities to architects to come up with designs that really push the limits. That same technology now needs to give us the input to drive down carbon emissions across all of the construction continuum. All phases that make up an asset’s lifecycle – design, build, operate – carry emissions. That’s why our Sketchup design software portfolio includes tools that help designers make the most environmentally-friendly design decisions at the earliest possible stage, taking into consideration the effects of a building’s orientation, the local climate, the use of materials, the number and type of windows, and the application of HVAC technology. All with an eye to creating designs with the smallest environmental footprint over the long term.
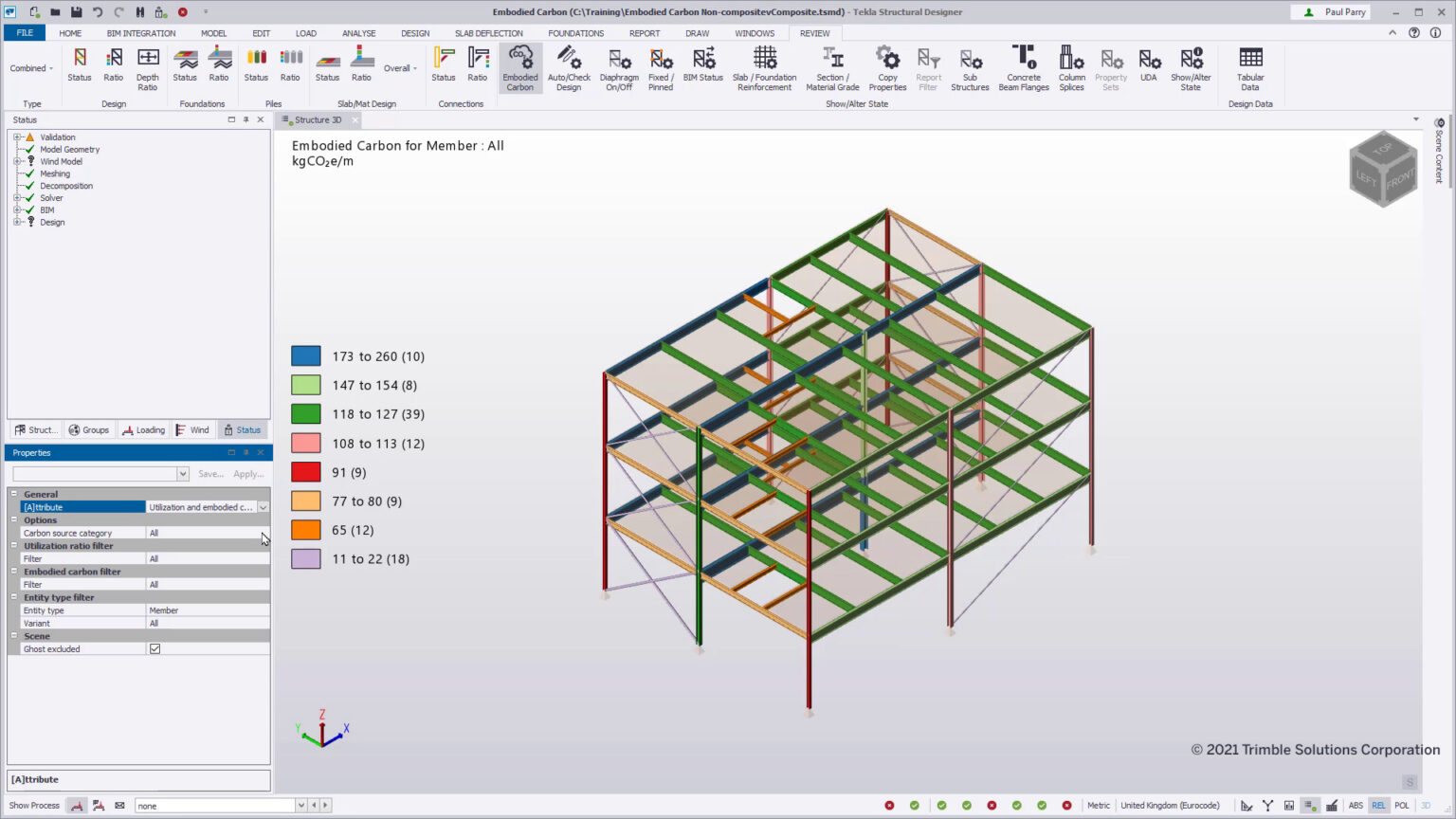
We incorporated a carbon calculator in our Tekla structural design software and worked with the One Click LCA automated life cycle emissions assessment software to offer our users enhanced visibility of the environmental impact of their structural designs. And it is also why Trimble strives to connect the traditionally separated workflows within the construction industry: to make data flow across projects to provide short- and long-term insights.
With the wider steel and construction industries being some of the largest industrial emitters of CO2, industry-wide sharing of data is crucial. With more data availability, designers can more readily come up with awe-inspiring and creative designs that still ensure our cities’ livability for decades to come. Working together with the wider industry in bodies like ResponsibleSteel has the potential to spark some interdisciplinary thinking. Many solutions to the global sustainability challenges are still years out. But we have opportunities to drive real emissions down already today if we build on the successes we already accomplished to make even more deliberately sustainable choices in all aspects of business operations. We need to challenge ourselves — on this day even more than on others — to dig deep into our collective wells of innovation and creativity and find new and lasting solutions together.
By Dietmar Grimm, VP Corporate Strategy & Sustainability Solutions, Trimble Inc.
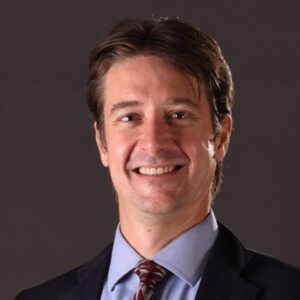
As VP Corporate Strategy and Sustainability Solutions at Trimble, Dietmar Grimm is helping the company drive profitable systems change across industries to a more productive, efficient, and sustainable, low-carbon, diverse, and equitable future for all communities.
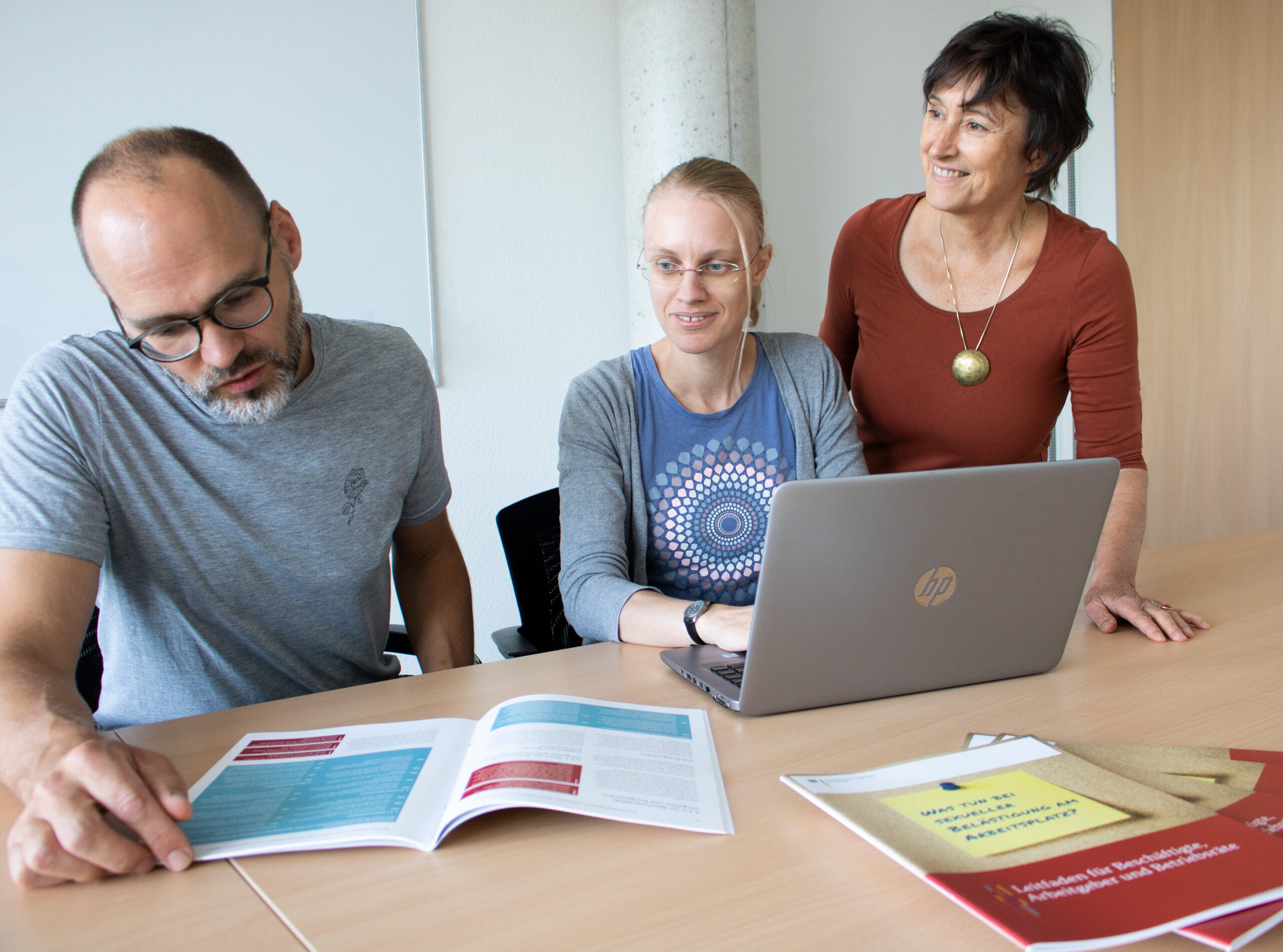
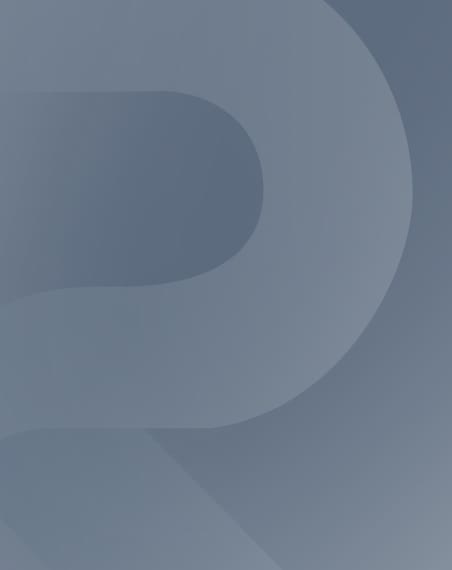
Harassment has no place in a ResponsibleSteel-certified site: Jana Loos on ArcelorMittal Bremen’s zero tolerance for harassment
ArcelorMittal Bremen in Germany was one of the first sites to become certified against the ResponsibleSteel Standard. As part of the certification process, the site had to address issues involving workplace harassment which had been raised by several female employees. Jana Loos, leader and spokesperson for ArcelorMittal Bremen’s anti-harassment project explains how the site tackled these issues and why it is so important to be vigilant and help to empower and support those who might be at risk.
A female worker received feedback from her team leader: “I like how you told the whole team that you won’t continue to tolerate their sexist comments towards you. However, my wife would never have allowed this to happen in the first place.”
Oftentimes, sexual harassment in the workplace does not constitute an overt criminal offence but is more subtly pervasive. In many cases, clumsy communication crosses the boundaries of what is appropriate in a professional environment. Or it transforms a normal social situation into an awkward one – simply because of one word too much, one touch in the wrong place or too long a gaze.
A while back, several women working at ArcelorMittal Bremen’s steel factory had the courage to disclose their experiences and seek help. A group of health experts, working council members and labour union members found the official processes wanting and united to tackle the issue. Shortly after, ArcelorMittal Bremen founded a project group to implement the social management standards required to obtain certification against the ResponsibleSteel Standard. This was the deciding factor that gave the topic the significance it needed.
The ResponsibleSteel Standard includes requirements which ensure a site identifies any risks, takes the necessary action to address such risks, and monitors the outcomes to determine where improvement is needed. Principle 6 of the recently updated ResponsibleSteel International Standard V2.0 specifically aims to make sure that “certified sites respect the rights of workers and support worker well-being.” Certified sites make the commitment to uphold labour rights and human rights, including maintaining a zero-tolerance policy for workplace harassment. Furthermore, certified sites must have effective procedures in place to understand and address any concerns raised by workers or their representatives.
Now, a few years later, ArcelorMittal Bremen has a contact person and a broad communications campaign on harassment. Trainings on the topic are implemented at all levels – comprising a seminar for new apprentices, leadership training and an awareness guide for all employees.
However, the path has not been smooth. With female staff making up only 8.6% of the workforce, some employees do not understand and even ridicule the topic. One male employee commented: “I, for my part, would like to be harassed one day!” The project team often need to stand up to such uninformed or hostile attitudes and provide basic education around these issues. The most important aim is a respectful working environment. There is no need to slander a specific person for a rude comment. Instead, the project group focuses on the empowerment of women – their approach is to equip women with the knowledge and training they need to tackle harassment situations confidently as well as raise overall awareness of the situation.
Since the beginning of the project, a noticeable change has taken place. Sexual harassment is a topic that is being talked about – even by the management board during official staff meetings with around 1,000 attendants. The goal is not “zero cases reported” – because this does not equal “zero cases” in actuality. In an atmosphere of mutual respect and encouragement, people experiencing harassment will have the courage to speak up and talk about their experiences. Therefore, the goal must be “as many cases reported as possible”.
We encourage any other organization to walk a similar path and provide their staff with all they need to tackle harassment situations. We firmly believe that this is a very important aspect of producing “responsible steel.”
By Jana Loos, Project Leader, ArcelorMittal Bremen
Please note: In the text, we only mention women being harassed by men, because this is the only constellation, we have come across so far in our organization, but we are fully aware that members of the LGTBQ+ community are exposed to similar harassment and of course, men might be harassed as well.
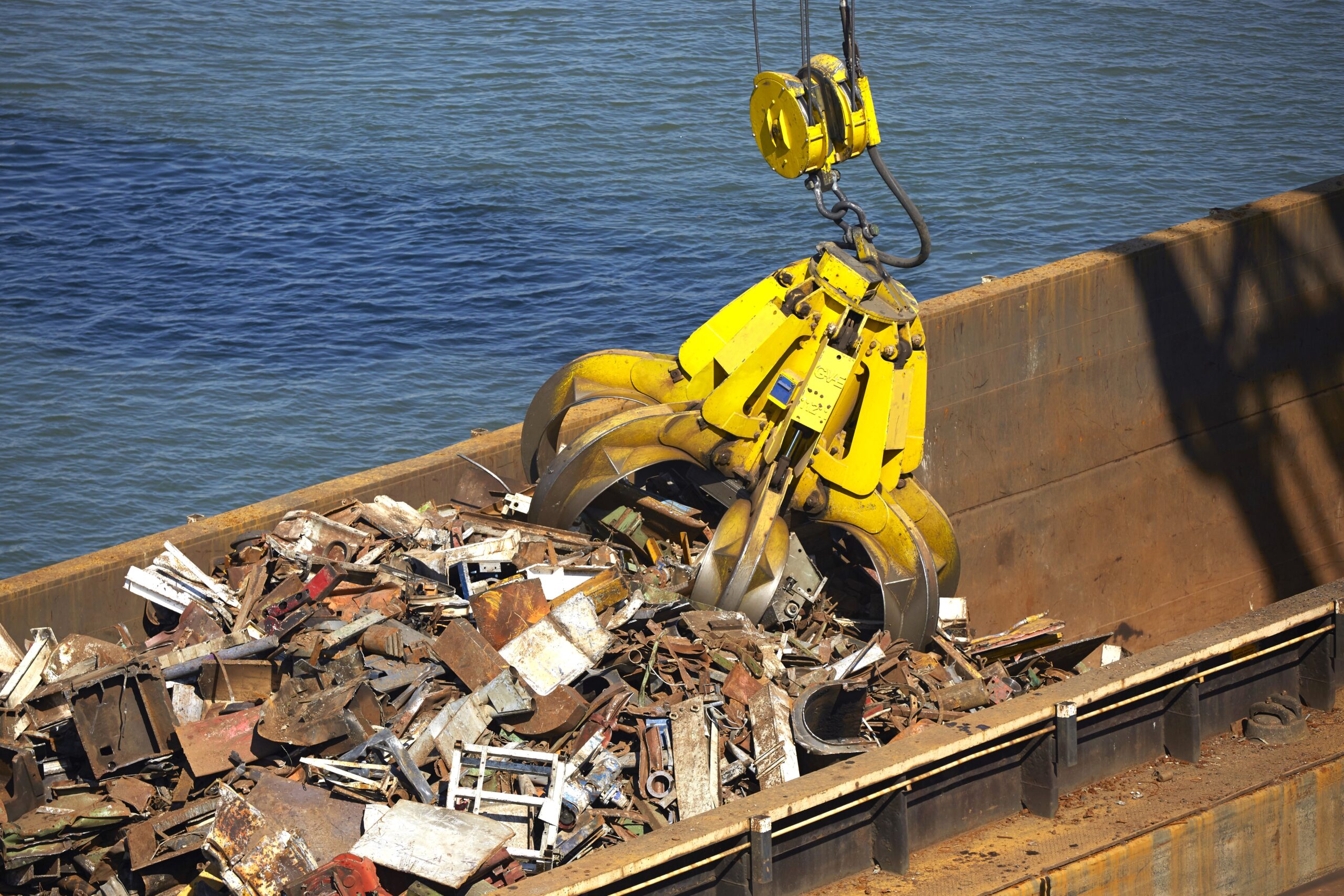
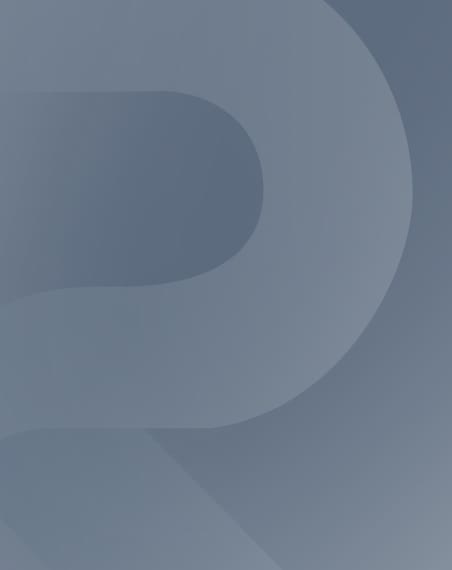
Maximising Circular Economics for Decarbonising Steel
The climate challenge for the steel industry is now well-established. Steelmaking currently accounts for between 7% and 9% of global CO2 emissions. We have not only the opportunity to do things differently across the industry, but it is vital if we are to drastically reduce the amount of emissions emitted from the steel value chain, and so have a real and lasting impact on people and the planet.
Steel is often talked about as the world’s most circular material. Maximising the recovery and use of recycled steel (i.e. scrap steel) is a critical lever and the most natural way to drive decarbonisation in the steel industry. The rates of scrap recovery today are extremely high – the highest of all materials. Worldsteel estimates that steel is recovered at a rate of 85% on average – far more from some product markets. Still, there is always opportunity for further progress. And yet, frustratingly, scrap alone is just not sufficient to meet global steel demand, and even if the use of scrap was maximised, published models tell us that it won’t provide more than half of what we need to get us to net zero by 2050 (International Energy Agency, 2020).
Clearly, as more and more buildings, cars and washing machines reach the end of their useful life, we must ensure that every last tonne of scrap is recovered, in order to produce lower-footprint steel products. But this alone will not be enough if we are serious about net zero by 2050.
It is absolutely vital that we also incentivise the decarbonisation of the only other alternative, the reduction of iron ore, however this is done, and however much scrap is available to complement it. And this is why the ResponsibleSteel International Standard adopts a ‘sliding-scale’ approach to incentivise decarbonisation across all steelmaking, regardless. In effect, our thresholds provide an equitable and effective mechanism for assessing progress on core decarbonisation across the sector and have been echoed and endorsed in numerous reports, proposals and schemes, by the International Energy Agency (IEA), Science Based Targets Initiative (SBTi), the Sustainable Steel Principles, the German Steel Federation and the Australian Green Buildings Council.
There is also a third dimension here. Let’s not forget that to maximise the progress to a net zero world, we need product design to create more value from every tonne of steel we produce and so reduce demand overall. A car made with stronger steel requires less material. Ball bearings that last longer will not need to be replaced so often. In each market, therefore, policymakers will need to reward product design that lengthens the product lifetime, reduces the amount of steel needed for a given purpose, and rewards the reuse and remanufacturing of steel products.
All these three elements – scrap recycling, demand efficiency, and decarbonisation progress – will be needed to get the steel sector to net zero within the next three decades. But how much the first two of these levers can contribute will be critical to understanding the scale of the decarbonisation progress challenge. In the coming months, ResponsibleSteel will be publishing further analysis of both scrap availability and steel demand to shed further light on what is undoubtedly the industry’s biggest challenge.