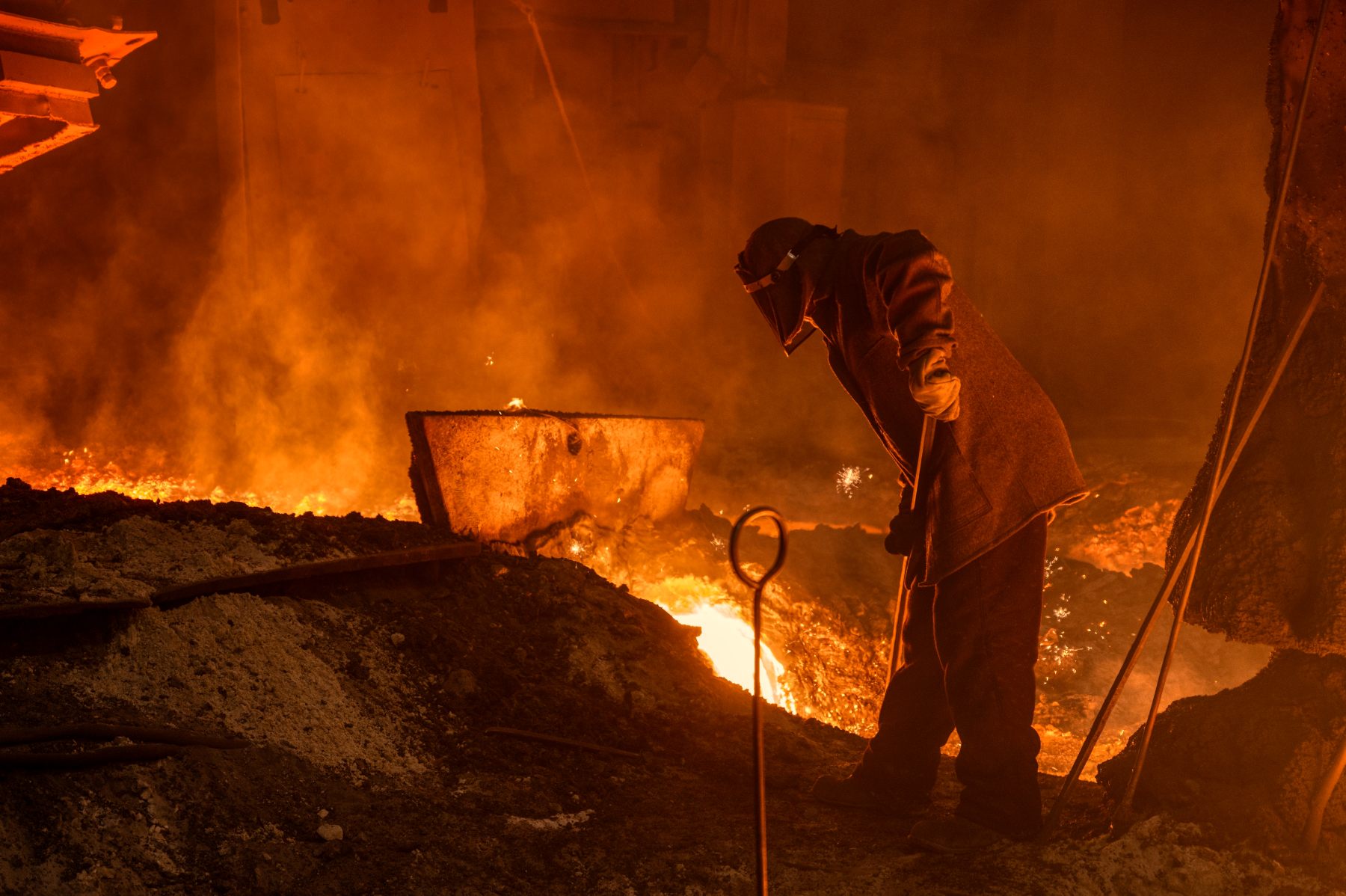
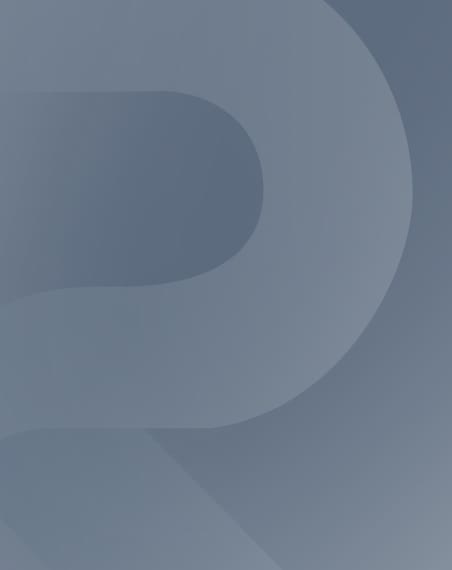
June 2025 Newsletter
The June edition of the ResponsibleSteel newsletter is here!
This month, we’re sharing key updates, including the launch of our joint European policy briefing with @LESS and the publication of our Fundamentals for GHG Emissions Accounting and Classification - a reference document for policymakers, investors, steelmakers, and civil society, among others, to measure and track decarbonisation progress.
We also spoke with our Head of Programmes, Amy Jackson, in a Q&A about her background, what drew her to ResponsibleSteel, and her plans for the role.
Plus, explore insights from our recent Just Transition Workshop and discover ways to get involved in our initiatives.
Click here to read the full newsletter.
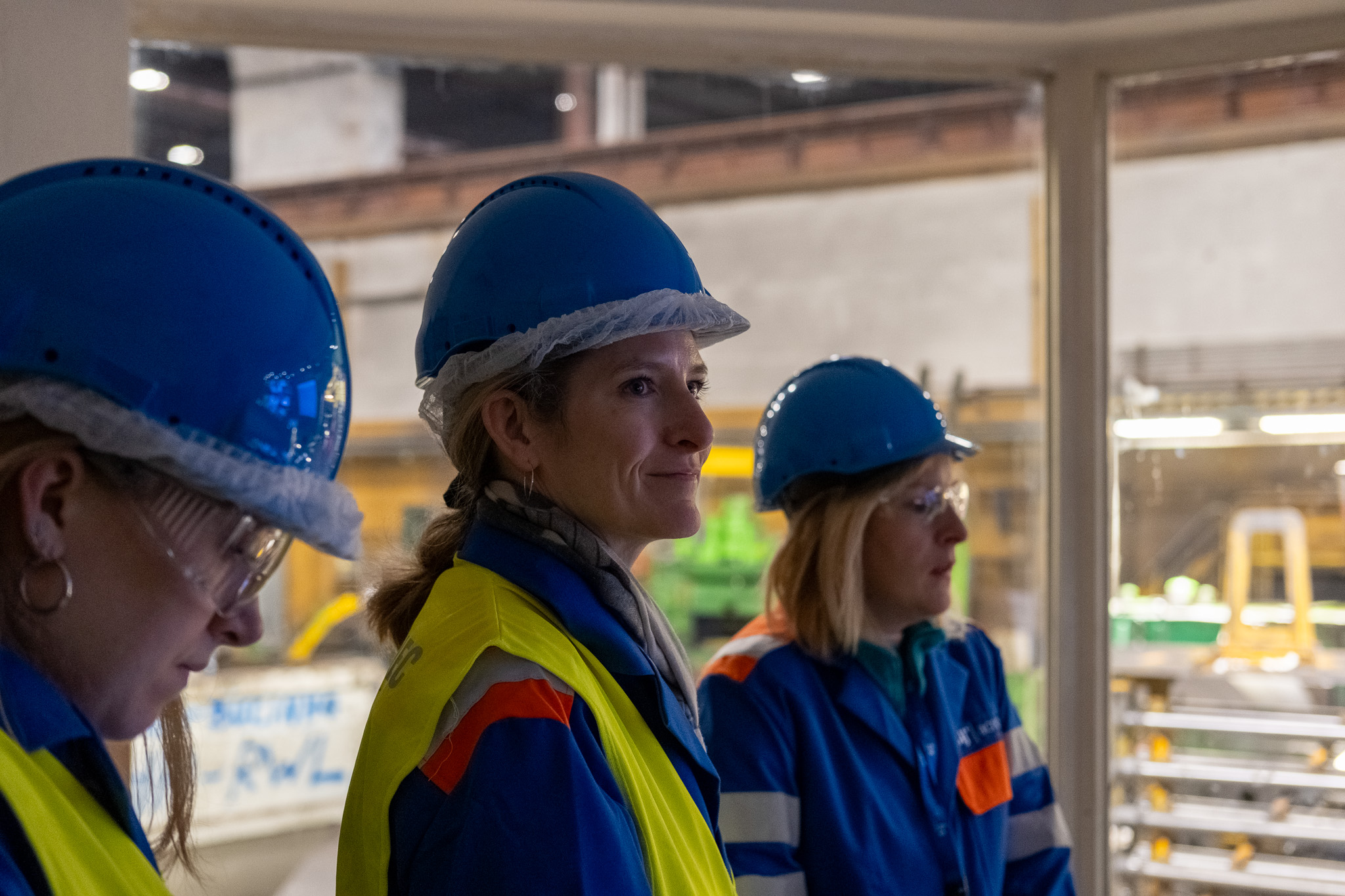
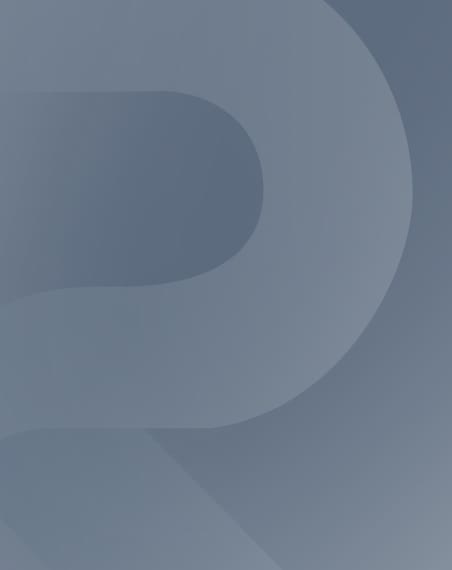
Meet the Team: Amy Jackson, Director of Programmes at ResponsibleSteel
Earlier this year, we welcomed Amy Jackson to ResponsibleSteel as our new Director of Programmes. With a background spanning ethical trade, to agriculture and responsible investment, read on to learn more about her experience in the standards industry, what brought her to ResponsibleSteel, and what she sees as key priorities for the standards and assurance programme moving forward.
1. You’ve spent a significant amount of time working on global sustainability standards. What originally sparked your interest in this work?
My journey began as a case of being in the right place at the right time. After completing my degree in Animal Biology and Marine Conservation, I moved to London, seeking adventure, and worked in a restaurant whilst job hunting. I overheard some regulars speaking about sustainability and oceans - I introduced myself, started volunteering, and eventually, a paid opportunity opened at the Marine Stewardship Council. I stayed for 11 years!
I’ve always had a passion for sustainability, and the inclusive, science-based, solutions-focused approach of sustainability standards appealed to me. They acknowledge the importance of ensuring good actors are recognised and rewarded for their work, and to me, this seemed a very constructive way of engaging people and businesses in improving practices.
Joining MSC in its early days helped me experience all sides of the system, from standard-setting to assurance, fundraising, communications, commercial engagement, and all from within a global organisation. The diversity of the challenge, the evolving landscape in how standards are seen and used, and the commitment to credibility are what kept me involved for so long.
2. Your experience spans ethical trade, agriculture, sustainable cotton, and responsible investment. How has your work in these areas shaped your approach to sustainability at ResponsibleSteel?
I’ve been very fortunate to have had the opportunity to engage with this wide range of sectors and different groups of stakeholders. In each of these, the basis has been on a defined agreement of good practice (the most important first step!), then the organisations work to find different ways to aid, verify, and reward progress towards the good practice. So, the basics are quite similar, with different organisations employing different theories of change as to the most effective levers to pull.
The most significant benefit of learning each new area has been the important reminder that, apart from your key partners and stakeholders, no one is thinking about your area of work as much as you are, or as much as you think they are. This means it’s very important to be clear about the benefits that each stakeholder gets from engaging with your system, and to make sure you are listening.
3. At ISEAL, you played a role in developing best-practice frameworks. How will those experiences influence your work on ResponsibleSteel’s International Production Standard?
The most valuable learning from those processes was how to bring diverse stakeholders together to reach an agreement. In a multi-stakeholder environment, differing opinions on some of the specifics are inevitable, so we must instead focus on the objectives we are trying to achieve, which is usually where we can find common ground.
It is also essential to ensure each group’s voice is heard, and not just the loudest! For our standard revision, we will ensure we are clear, from the outset, about the stakeholder map and the minimum level of response needed from each group. At the same time, we need to be aware that because of the differing perspectives, it will likely be impossible to reach overall (enthusiastic)consensus in all areas. At ISEAL, finalising the Credibility Principles involved asking stakeholders to indicate for each one whether a) they were happy and wouldn’t change a thing, b) could not live with it, or c) they could live with it, but had some tweaks or improvements to suggest. This allowed us to understand where the deal breakers were and what was causing them. It also allowed us to move forward and finish the document, while still noting the potential areas to review for the next version.
.jpg)
4. What excites you most about the future of sustainability in the steel industry, and what role do you see ResponsibleSteel playing in it?
It has been an exciting and sharp learning curve coming into the steel industry, and I know this will continue for some time. This might be a standards nerd thing to say, but the thing that excites me the most is the agreement on the need for harmonisation and alignment of the methodologies we’re using to assess steel sustainability.
When I was preparing for my interviews for the job, I learned that depending on the methodology used, emissions numbers could vary by as much as 30%! This makes comparing performance and tracking improvements very difficult and means so much time is wasted on completing different reporting templates, rather than focusing on times and resources on making sustainability improvements.
With the Steel Standards Principles and the efforts of ResponsibleSteel and others to ensure interoperability, I think we are in a good place. In other sectors, this need for alignment has been noted. For example, in disclosure with the TCFD and TNFD, it allows all efforts to be pointed in the same direction, resulting in greater effectiveness and less wasted time.
What also stands out is the passion of the people involved –from the ResponsibleSteel team to our members and other stakeholders. There is a personal commitment to improving how steel is produced, and this passion and leadership are essential for making a difference.
5. You’ve worked on standards development, chain of custody, and assurance. What do you think are the most essential components when it comes to forming credible and impactful sustainability initiatives?
One reason I have come back to working with voluntary sustainability standards systems is because I love how beautifully all the different pieces fit together. Agreeing on what good looks like, assessing progress, assuring that a certain level is met, building capacity - it’s a whole system designed for continuous improvement, and it's what makes sustainability standards systems unique and special actors in the landscape. There are other standards, but it’s one thing to say what to do, it’s a whole other (harder)thing to make sure everyone’s doing it (assurance), and an even greater challenge to be certain that we’re making a difference (MEL: monitoring, evaluation and learning). This continued engagement with ensuring the effective implementation of the standard once it’s released is perhaps one of our collective community’s most understated USPs.
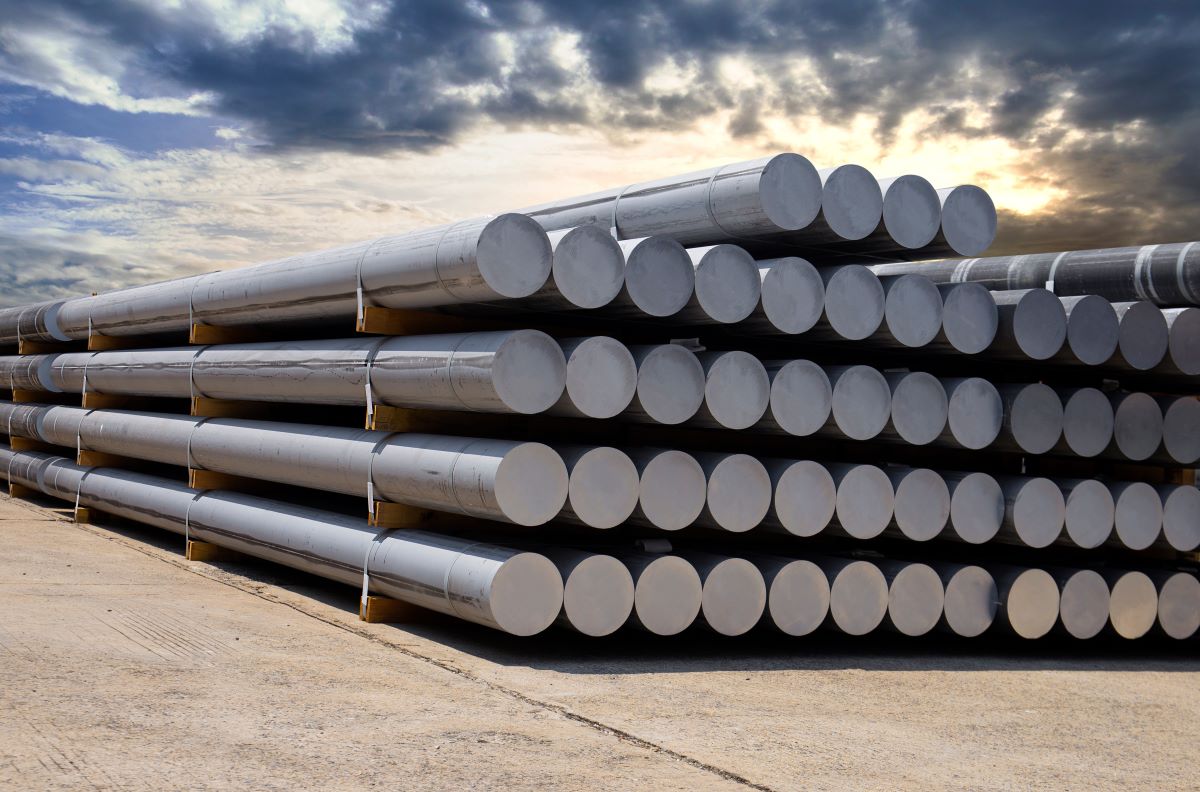
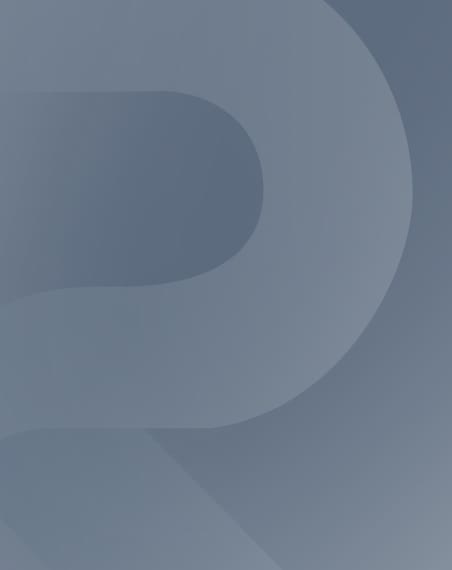
ResponsibleSteel publishes fundamentals for GHG emissions accounting and classification to drive transparency, comparability, and decarbonisation progress
To help improve the accessibility of ResponsibleSteel’s emissions methodology and accelerate robust emissions accounting and reporting, ResponsibleSteel has today published extracts from Principle 10 of the ResponsibleSteel International Production Standard relating to Climate Change and Greenhouse Gas (GHG) Emissions.
Importantly, this is not an independent standard against which steelmakers can make certification claims. Instead, ResponsibleSteel's Fundamentals for GHG Emissions Accounting and Classification is designed as a valuable resource for steelmakers, steel buyers, policymakers, investors, and civil society organisations to use as a reference to measure and track progress as the global industry transitions to lower-emission production practices.
The document aims to improve the comparability, consistency and transparency of emissions accounting and reporting across the global steel industry by outlining three of Principle 10’s fundamental components:
- ResponsibleSteel’s methodology for the calculation and disclosure of crude steel GHG emissions intensity at the site level.
- ResponsibleSteel’s classification system to assess a steelmaking site’s decarbonisation progress.
- ResponsibleSteel requirements for GHG emissions intensity declarations at product-level.
ResponsibleSteel’s “Decarbonisation Scale” approach enables all steelmaking sites, globally, to be compared on a like-for-like basis, based on transparent and fair accounting rules. By adopting this approach, the industry has the opportunity to increase the transparency and consistency of emissions data across the value chain, reducing administrative burdens and enabling more effective implementation of decarbonisation policies and mechanisms.
This new publication will be particularly valuable for stakeholders either looking to align with ResponsibleSteel’s approach or to build interoperability between GHG-specific frameworks, regulations, and procurement systems.
It is important to note that no claims relating to ResponsibleSteel certification, or its equivalency, or Decarbonisation Progress Level achievement, can be made based on this document alone. The document only represents a subset of Principle 10, which in full also addresses corporate commitments to the Paris Agreement, climate-related financial disclosures, and additional site-level emissions reductions. Nor does it include any of the other 12 Principles outlined in the Production Standard relating to the responsible production of steel.
We believe that truly responsible steel production requires steelmakers to go beyond decarbonisation and take steps to mitigate other social and environmental impacts. But amidst the growing urgency of the climate crisis, ResponsibleSteel remains committed to supporting global steel decarbonisation through practical tools developed with multi-stakeholder support. This latest publication reflects that commitment to offering robust, credible, scalable tools to accelerate emissions reductions at scale.
For any questions about the use or development of ResponsibleSteel’s Emissions Metrics, please contact standards@responsiblesteel.org.
Learn more about ResponsibleSteel’s Fundamentals for GHG Emissions Accounting and Classification here.
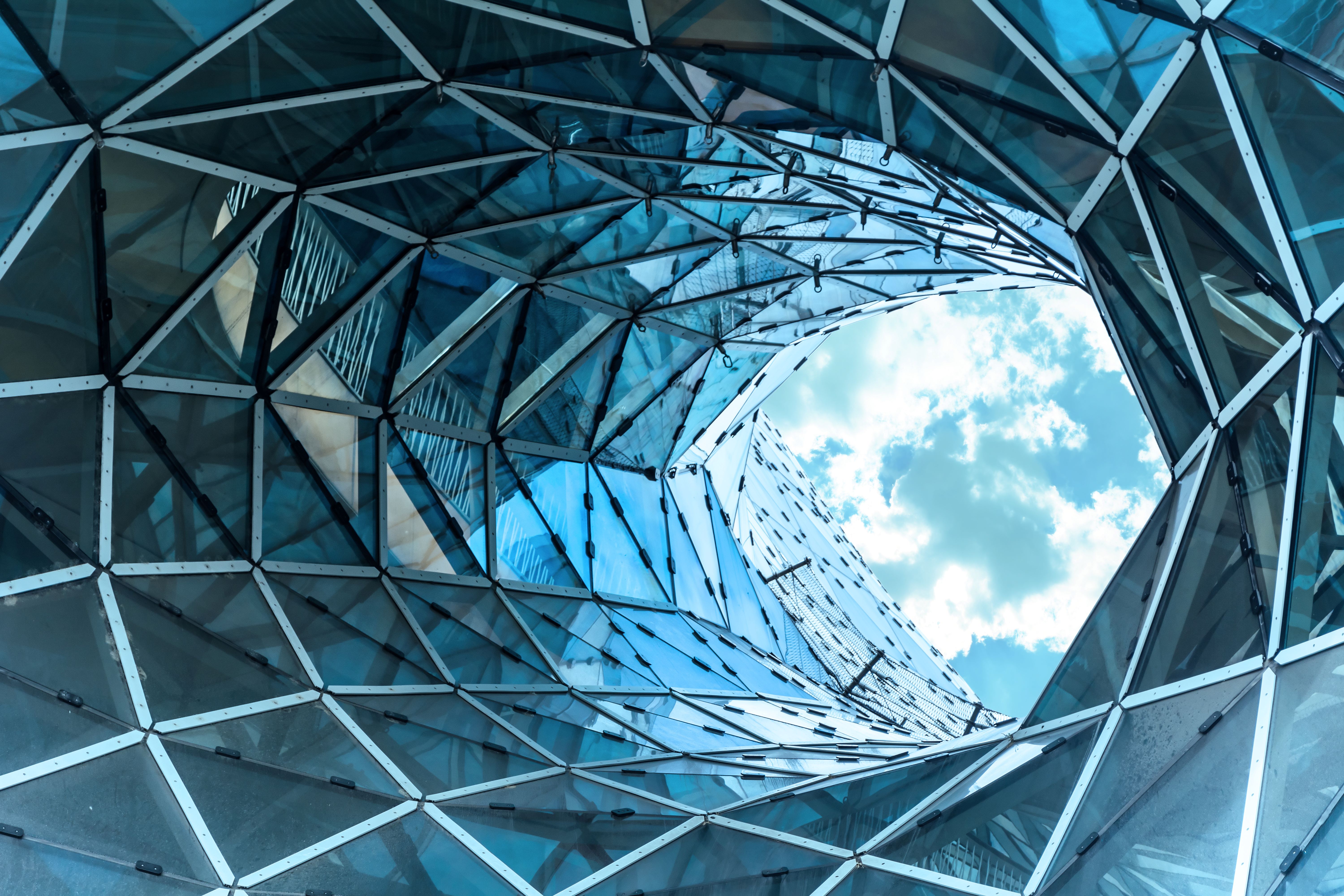
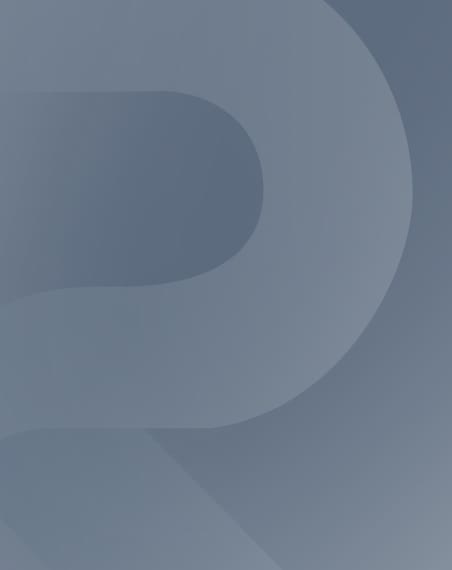
ResponsibleSteel and LESS aisbl urge robust, scrap-conscious approach to effective European steel decarbonisation
ResponsibleSteel and the Low Emission Steel Standard (LESS aisbl) today jointly release a new policy briefing, ‘The Steel Decarbonisation Scale’, urging European policymakers to adopt a more robust and realistic approach to steel decarbonisation—one that recognises the physical limits of scrap supply and incentivises genuine emissions reductions across all steel production routes.
The study highlights that Europe’s steel industry, as the world’s second-largest producer, is responsible for 6% of the European Union’s total emissions. With ambitious EU targets aiming for a 55% reduction in net greenhouse gas emissions by 2030 and net zero by 2050, the way steel decarbonisation is measured and incentivised is of critical importance.
A key finding of the study is that current policy discussions, including the European Steel and Metals Action Plan (ESMAP) and proposals for voluntary carbon labels for steel, risk undermining climate goals if they fail to account for the fundamental constraints on scrap availability. Despite a high global steel recycling rate of 85%, only about 32% of the world’s demand for new steel can currently be met with recycled scrap due to the long lifetime of steel products, according to the International Energy Agency (IEA). While the amount of available scrap is set to increase, the IEA estimates that scrap will still only be sufficient to meet 46% of steel demand by 2050.
“Steel decarbonisation requires an appropriate base for comparing steel products in terms of their global climate impact,” said Dr. Martin Theuringer, Secretary General of LESS aisbl. “Scrap is a valuable and limited resource. Any label or standard that ignores this risks distorting markets and ultimately slowing down the transition to truly low-emission steel. Our approach ensures that both primary and scrap-based production are incentivised to decarbonise, not just to compete for a fixed pool of scrap.”
ResponsibleSteel and LESS propose the adoption of a “steel decarbonisation scale” that complements traditional carbon footprinting by explicitly accounting for the ratio of scrap and primary iron used in steelmaking. This approach, already recognised by the G7 and incorporated into international standards, would:
- Prevent fruitless competition for a limited scrap supply
- Incentivise decarbonisation across all steel production routes
- Promote technology-neutral, WTO-compliant solutions
- Support the competitiveness of European industry while advancing global climate goals
“A European label for steel is a great opportunity to incentivise steelmakers to become globally competitive on their real decarbonisation progress,” said Annie Heaton, CEO of ResponsibleSteel. “A well-designed classification system will do this by taking into account scrap content in addition to the measurement of steel‘s carbon intensity, recognising that scrap will at best provide half of the world’s steel by 2050. As a result, this ‘steel decarbonisation scale’ approach incentivises investments that drive progress in the steelmaking process itself, whether in primary or secondary iron and steel making.”
The two organisations call on the European Commission to integrate the steel decarbonisation scale into the development of voluntary labels, lead markets, and investment support mechanisms, ensuring that future measures are effective, fair, and aligned with Europe’s climate ambitions.
Download the briefing here.
Access ResponsibleSteel’s approach to GHG emissions metrics here.
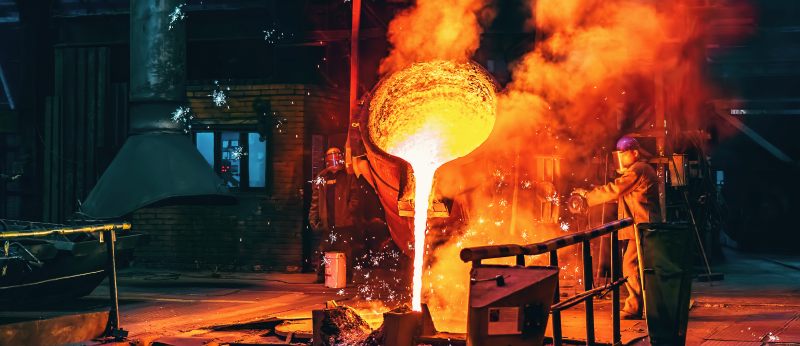
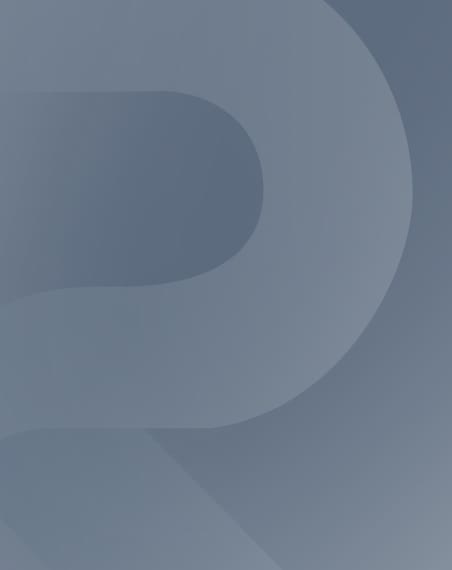
May 2025 Newsletter
This month, we’re building on the momentum from our recent AGM and Members Meeting, where we reflected on the progress of the past year and explored the key priorities for 2025.
We’ve launched a new events page for upcoming initiatives. Alongside this, we are announcing new training sessions and working groups, with workshops scheduled in the coming months.
We are also calling on members to submit guest blogs for the ResponsibleSteel website to share insights, innovations, and experiences of responsible steelmaking.
Read our latest newsletter for updates, opportunities to engage, and news from across our network.
Click here to read the full newsletter.
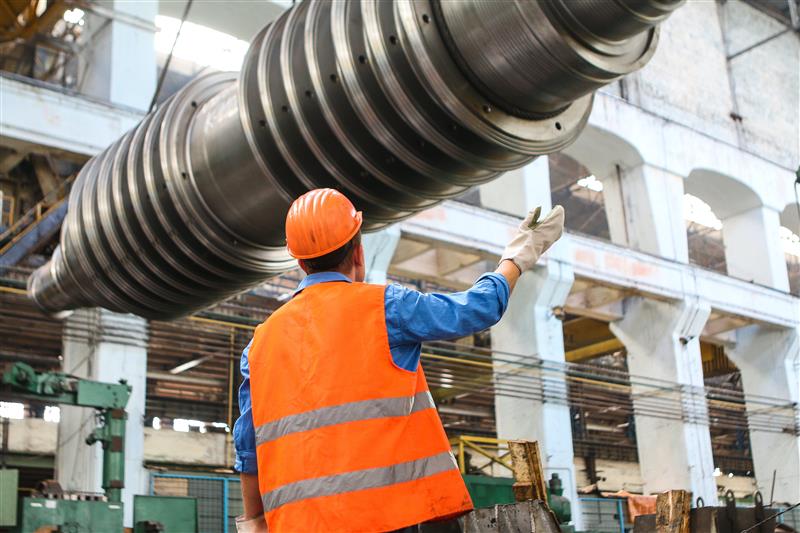
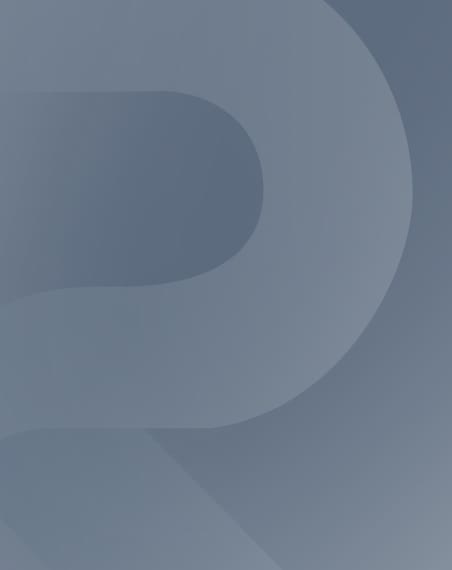
April 2025 Newsletter
This month, we’re proud to share the second ResponsibleSteel Progress Report - a chance to reflect on the major milestones achieved in 2024, highlight key learnings, and look ahead to the work still to come.
Our upcoming AGM and Members Meeting will also explore important developments across our programmes. If you haven’t registered yet, now’s the time.
To mark Earth Day, we’ve published a new article examining our relationship with the planet and the role ResponsibleSteel plays in supporting its protection.
We highlight an important upcoming development relating to our decarbonisation requirements and guidance. You’ll also find the latest updates on audits, events, and training opportunities.
In this newsletter, you will find updates on:
- Our 2025 Progress Report
- New members
- Upcoming trainings
- Updates from the team
- And more...
Click here to read the full newsletter.
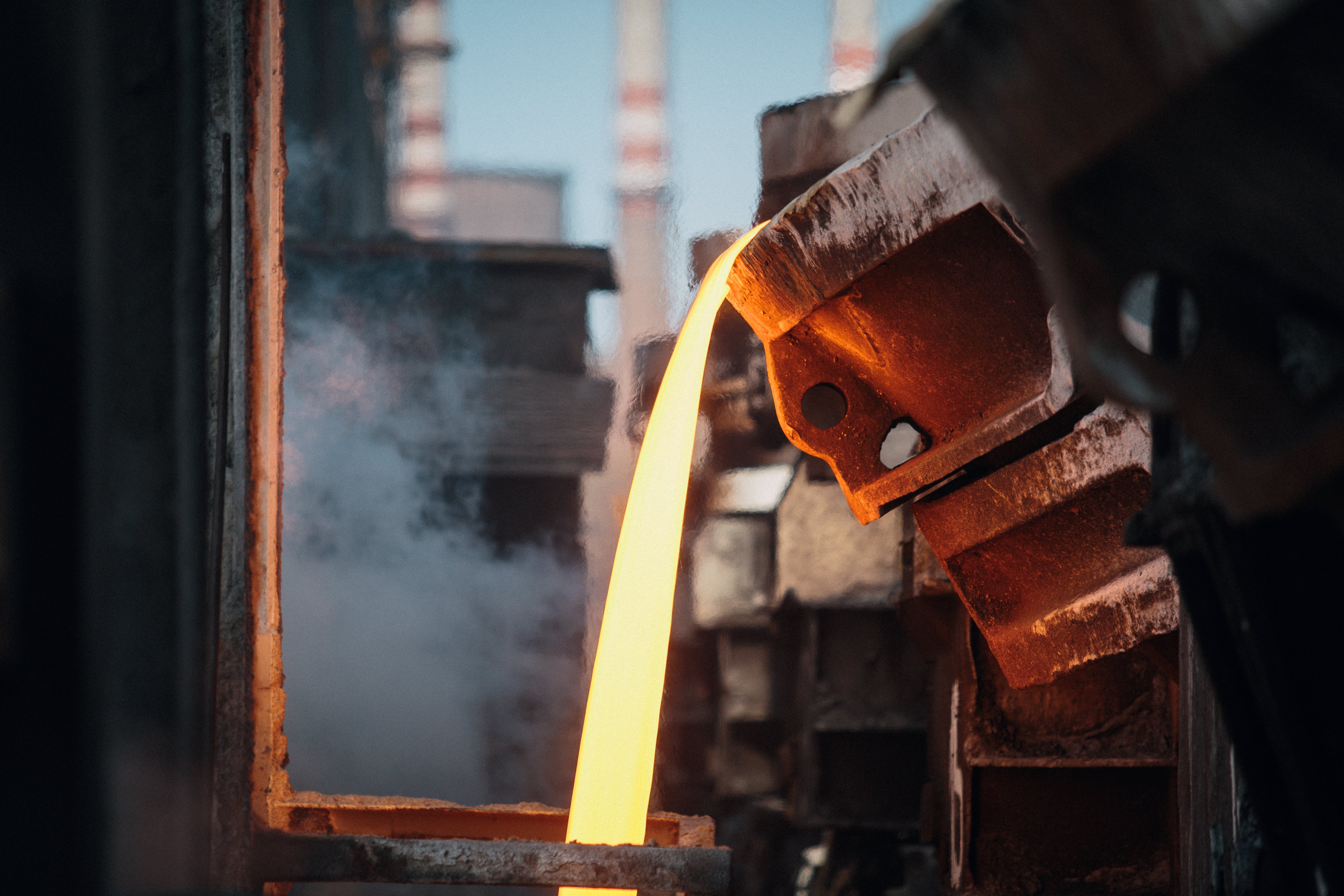
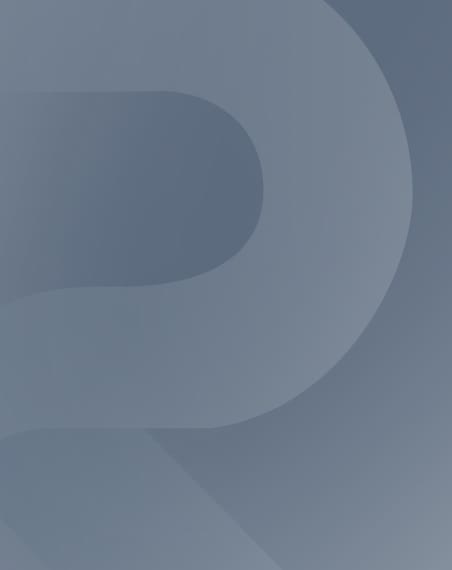
ResponsibleSteel publishes second annual Progress Report
ResponsibleSteel is fast becoming the reference tool to drive the demand, policy, and finance levers necessary for the steel industry’s transition, providing a sustainability roadmap that customers, communities, investors, and workers can all get behind.
ResponsibleSteel’s annual Progress Report provides an opportunity to measure and report on the progress of our programmes, celebrating our milestones and identifying areas for learning and improvement.
In this second ResponsibleSteel Progress Report, we track the development of new work undertaken in 2024, the growth of ResponsibleSteel's membership, and the progress of our certification programme as we look toward 2030 and beyond.
2024 was a challenging year for the industry, but despite setbacks, we continued to see real determination and progress.
In 2024, we saw a 34% increase in the number of Certified Sites, bringing the total up to 87. And we saw the first sites complete re-certifications, a true testament to the enduring value of ResponsibleSteel certification. Critically, the first Certified Steel was also launched on the market – 2.4 million tonnes produced by U. S. Steel’s Big River Steel site – marking a new era of progress.
This Progress Report examines the growth of ResponsibleSteel’s certification programme and membership in 2024, as well as featuring other highlights from the year, including:
- The launch of the International Production Standard Version 2.1
- The launch of a draft Chain of Custody Standard
- The publication of our report, Charting Progress to 1.5°C through certification
- Insights into the value of ResponsibleSteel membership and certification from our 2024 Membership Survey
Looking to the future, we continue to build on work begun in 2024 to build a market for responsibly produced, near-zero steel by engaging with and mobilising policymakers, investors, and buyers of steel.
Read the full report to find out more about our progress in 2024 and plans for 2025.
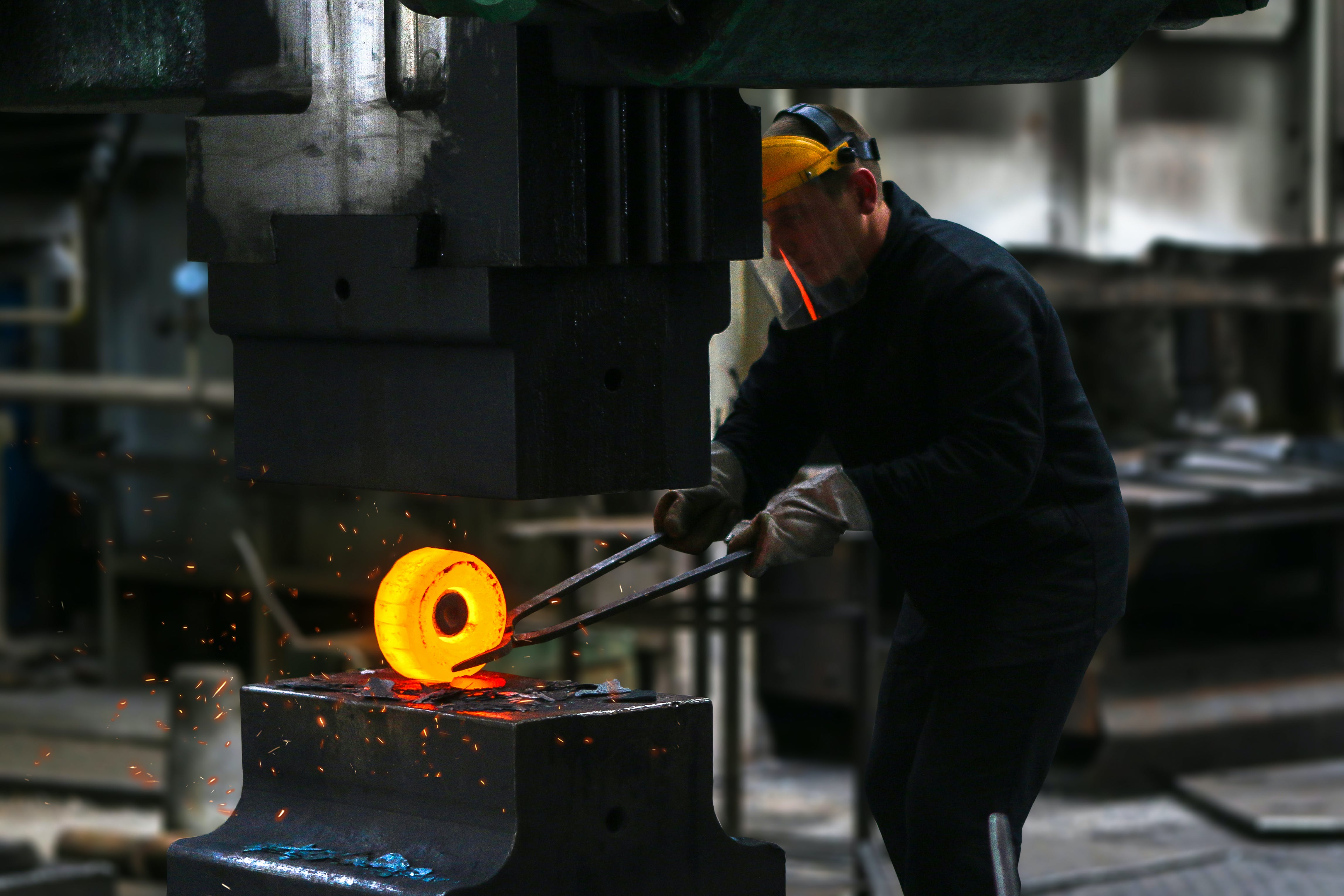
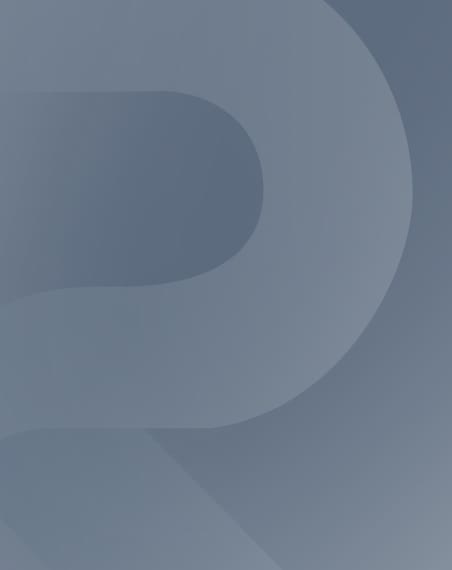
Steel Safety Day: Strengthening safety in a high-risk industry
Steel Safety Day is a reminder that safety must be a shared value across the global steel industry. Established to reduce accidents, it highlights the risks workers face daily, from heavy machinery and extreme heat to hazardous materials, and reinforces our collective responsibility to protect them.
In 2023, World Steel Association (worldsteel) members reported 61 fatalities globally, representing a global fatal frequency rate (FFR) of 0.017, the lowest on record. While this demonstrates progress, steelmaking remains a high-risk industry compared to other sectors. According to worldsteel, on average, 20% of incidents have the potential to lead to serious injuries or fatalities. Without strong safety frameworks, the risks associated with working in the steel industry can have devastating consequences for workers, families, and wider communities.
ResponsibleSteel members are making strong headway in fostering a culture of safety. At Arvedi AST, safety is a shared responsibility from leadership to the frontline. HSE Manager Fernando Camponi explains:
"In Arvedi AST, over the last few years, major efforts have been directed towards increasing the health and safety culture at every level, from management to workers, with particular reference to the key role of supervisors. As an example, we can mention the 'STAR' (Safety Training and Review) project, through which the most expert supervisors check on site the correct application of all safety operating instructions by all workers, providing, if necessary, for their revision or updating."
Meanwhile, Outokumpu has embraced technological innovation to enhance safety. Thorsten Piniek, VP of Health & Safety, comments:
"Safety of our people is our first priority. During 2024, we maintained world-class safety performance. We have implemented a structured way of doing safety behaviour observations and learning from each other across the organisation. Last year, our preventive safety actions were up 5% since 2023, so our people have done a fantastic job! In addition, our three safety robots utilising AI helped us reduce our employees' exposure to hazardous areas."
There is also a financial benefit to investing in health and safety. A 2017 study by the Institute for Work & Health in Canada found that employers investing in occupational health and safety in the manufacturing sector earned on average an estimated return of 24%.
As technology advances, so does our ability to prevent harm within the steel sector. But lasting progress relies on culture: empowering workers, building trust, and making safety the priority and default. A sustainable steel industry must first and foremost be a safe one.
At ResponsibleSteel, health and safety are core to our International Production Standard, as they are fundamental to a sustainable industry. The Occupational Health and Safety (OHS) principle embedded in our Production Standard ensures that the safety of workers is prioritised at every level of steel production. A sustainable industry must be safe for the people who power it, and without proper protections in place, there can be no true social or environmental progress.
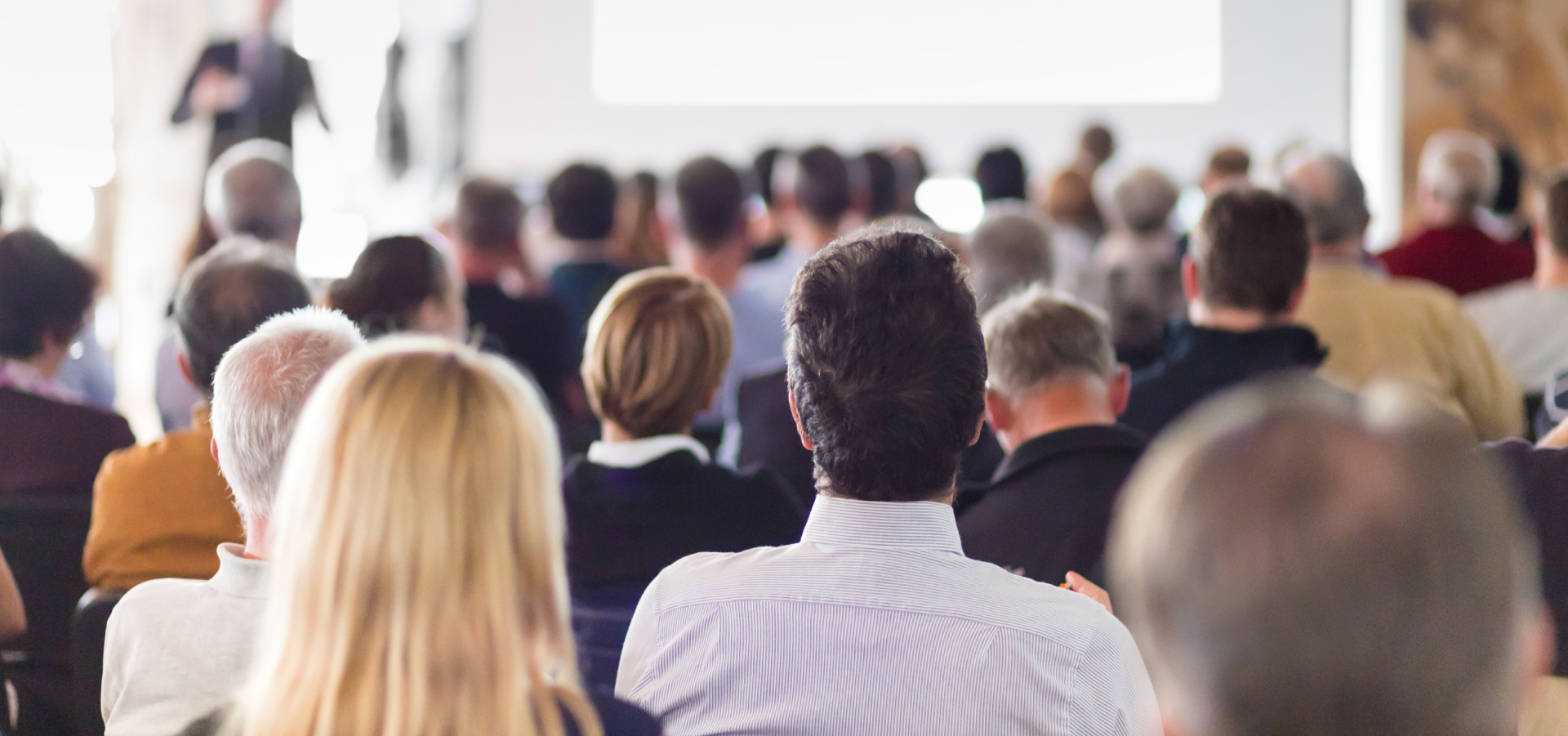
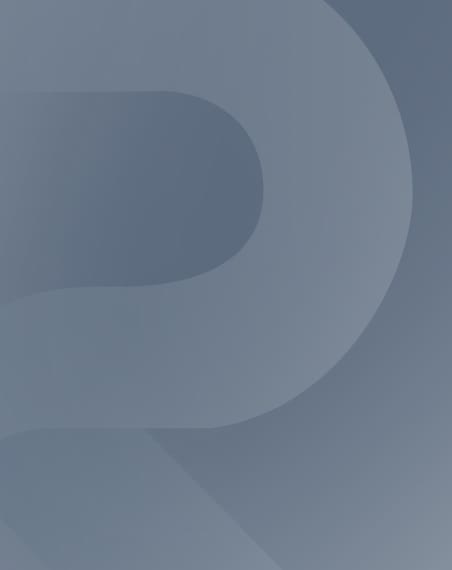
Join us at our upcoming Annual General Meeting
We are pleased to invite ResponsibleSteel members to the 2025 Annual General Meeting (AGM) of ResponsibleSteel Ltd on Monday, 19 May 2025. The meeting will be held online via Microsoft Teams.
Time:
- AGM: 12:00 – 12:30 (GMT+1)
- Members Meeting: 12:30 – 13:30 (GMT+1)
Agenda:
- Chair’s Report
- CEO’s Update
- Financial statements and reports
- Announcement of the results of the election of Directors
Registration in advance is required to attend the AGM and Members Meeting, and members must be up-to-date with their membership fees to be able to join and participate in any votes. We encourage all members to register and participate in the call.
The AGM will be followed by a Members Meeting, during which we will explore the latest developments around ResponsibleSteel and what’s in store for the rest of the year. Members will also have the chance to ask questions and provide input on a number of topics.
If you have any questions or would like to register, please contact our membership team.
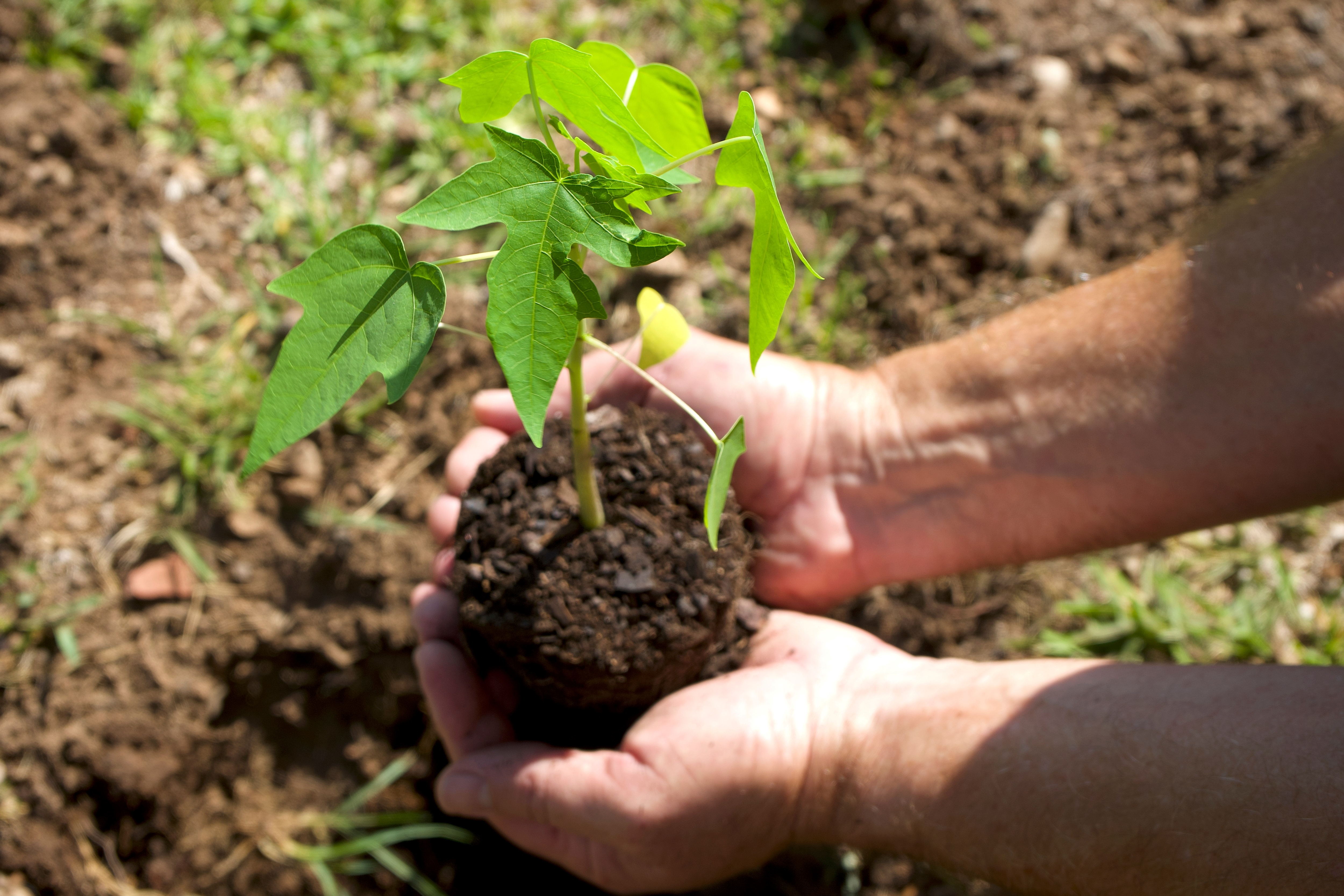
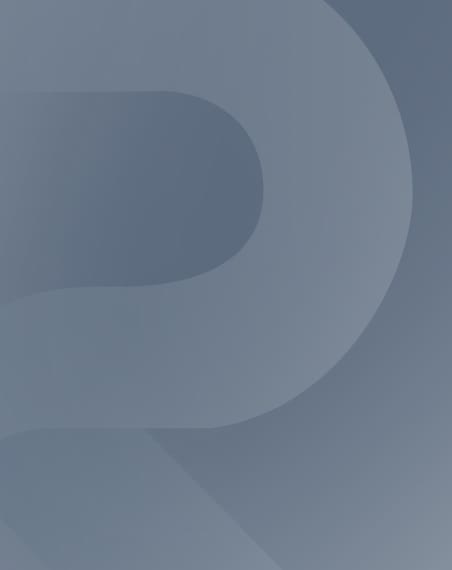
Earth Day 2025: Advancing sustainability in the steel industry
Earth Day is a moment to reflect on our relationship with the planet, and a call to protect the ecosystems and communities that sustain us. As we face accelerating climate and environmental crises, it’s clear that good intentions are not enough. Real progress requires meaningful, measurable action.
Steel is an essential part of modern life, supporting everything from clean energy systems to the infrastructure around us every day. But the way that steel is produced comes with a heavy environmental and social footprint. It’s one of the most emissions-intensive industries, and its impacts on land, water, and people are significant. At ResponsibleSteel, we believe that the future of steel must be aligned with the future of the planet. We unite businesses, civil society organisations, sustainability experts, and other industry stakeholders around a shared vision: that steel can—and must—be produced in a way that is environmentally and socially responsible. Our work is grounded in a set of shared principles that reflect the full scope of sustainability, including climate action, biodiversity protection, responsible resource use, and respect for human rights.
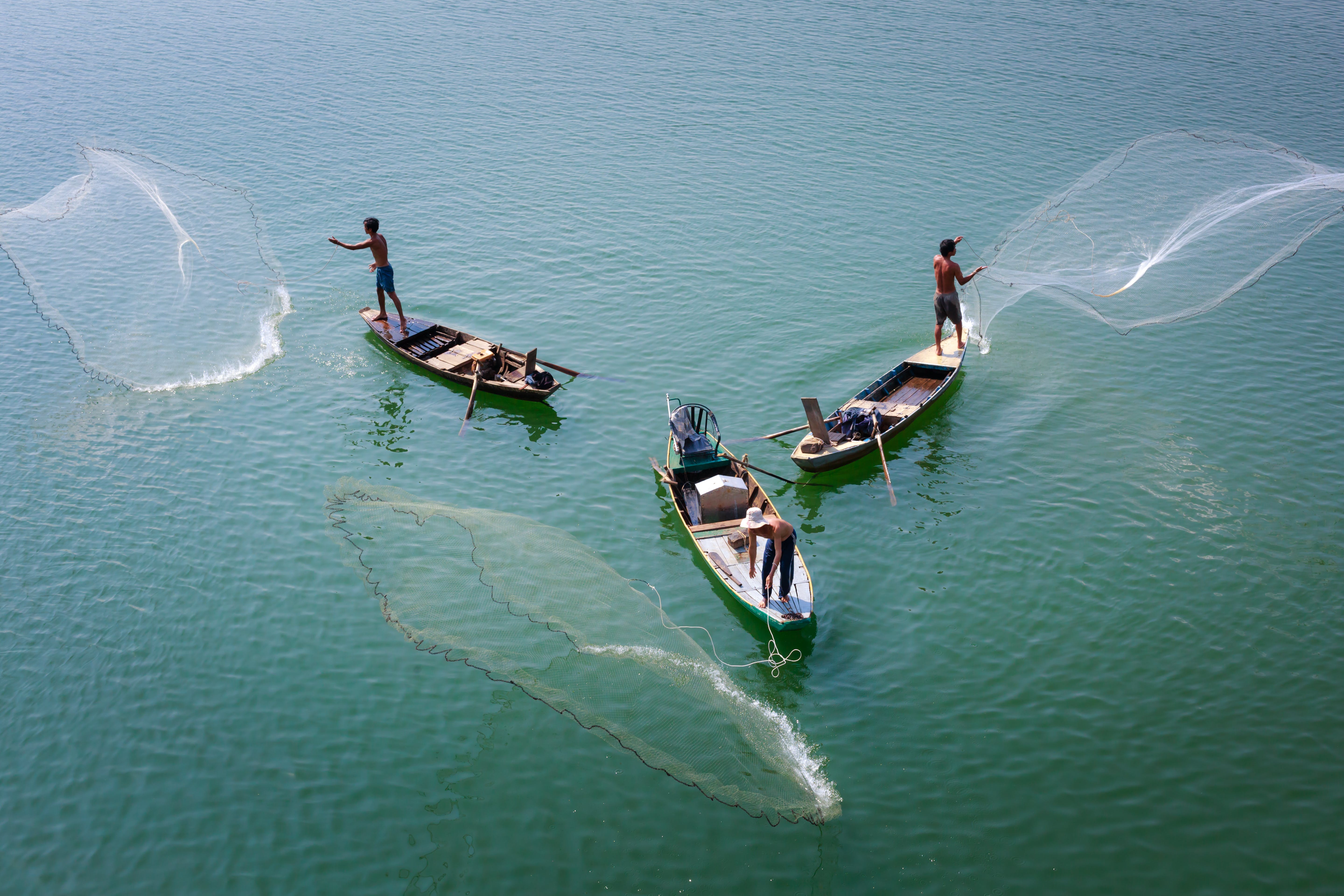
For example, our Biodiversity Principle aims to ensure that sites actively protect nature by respecting conservation areas, avoiding harm to high-value habitats, and following the mitigation hierarchy to reduce impacts. Sites are expected to assess biodiversity risks and aim for no net loss, and even a net gain, where critical habitats are involved. Our Water Stewardship Principle calls for a clear understanding of how water is used and shared in each location, with strong planning to protect water quality, support local communities, and safeguard stressed resources. By setting clear expectations like these across our Production Standard, we’re helping drive the changes the steel industry needs.
Earth Day is a reminder that environmental and social responsibility are inseparable. Steel may not be the first thing that comes to mind when we think about nature or climate, but it plays a central role in shaping both. The transformation of the industry is already underway, and must continue apace, driven by accountability, urgency, and collaboration. We don’t produce steel, but our work ensures that when it is made, it’s done with consideration for people and the planet. Because a thriving Earth requires responsible progress in every sector, including steel.
Learn more about how we’re supporting change here.
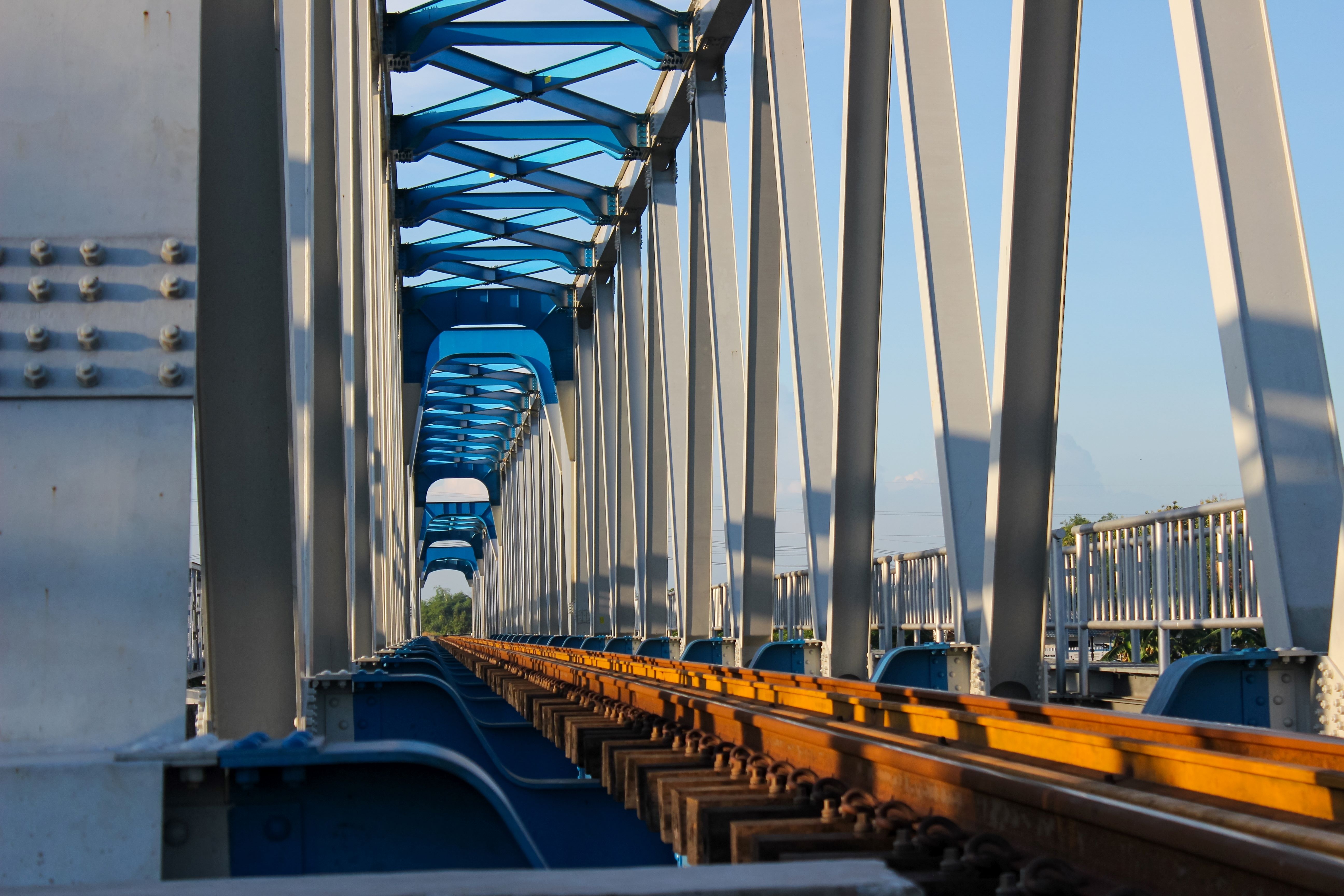
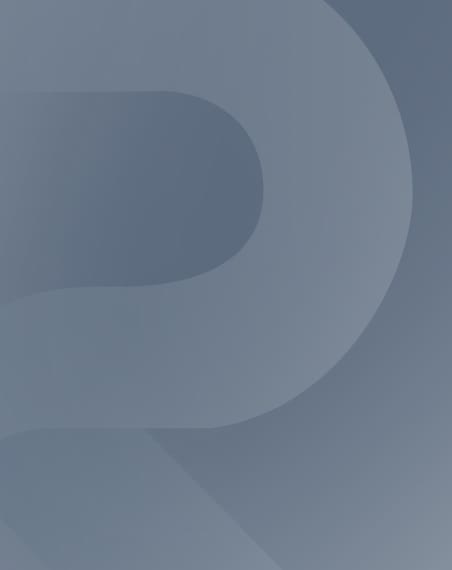
March 2025 Newsletter
This month, we were delighted to see JSW achieve its first ResponsibleSteel certifications for four sites in India, covering 83% of the company’s national steel production—an important milestone for Indian steel. And as steel policy continues to evolve rapidly worldwide, we've provided a summary of key developments from the EU, UK, China, and beyond.
We also celebrated International Women’s Day by highlighting the women driving change across the steel supply chain. In recognition of Global Recycling Day, we reflected on the history of steel recycling and the valuable lessons it offers in the journey toward responsible near-zero steel.
Additionally, we’re pleased to welcome three new members to the ResponsibleSteel community—PRCO America, ABS, and Yeşilyurt Demir Çelik. Welcome aboard!
In this newsletter, you will find updates on:
- New certifications
- New members
- Policy developments
- Upcoming audits and training
- Member survey results
- And more...
Click here to read the full newsletter.
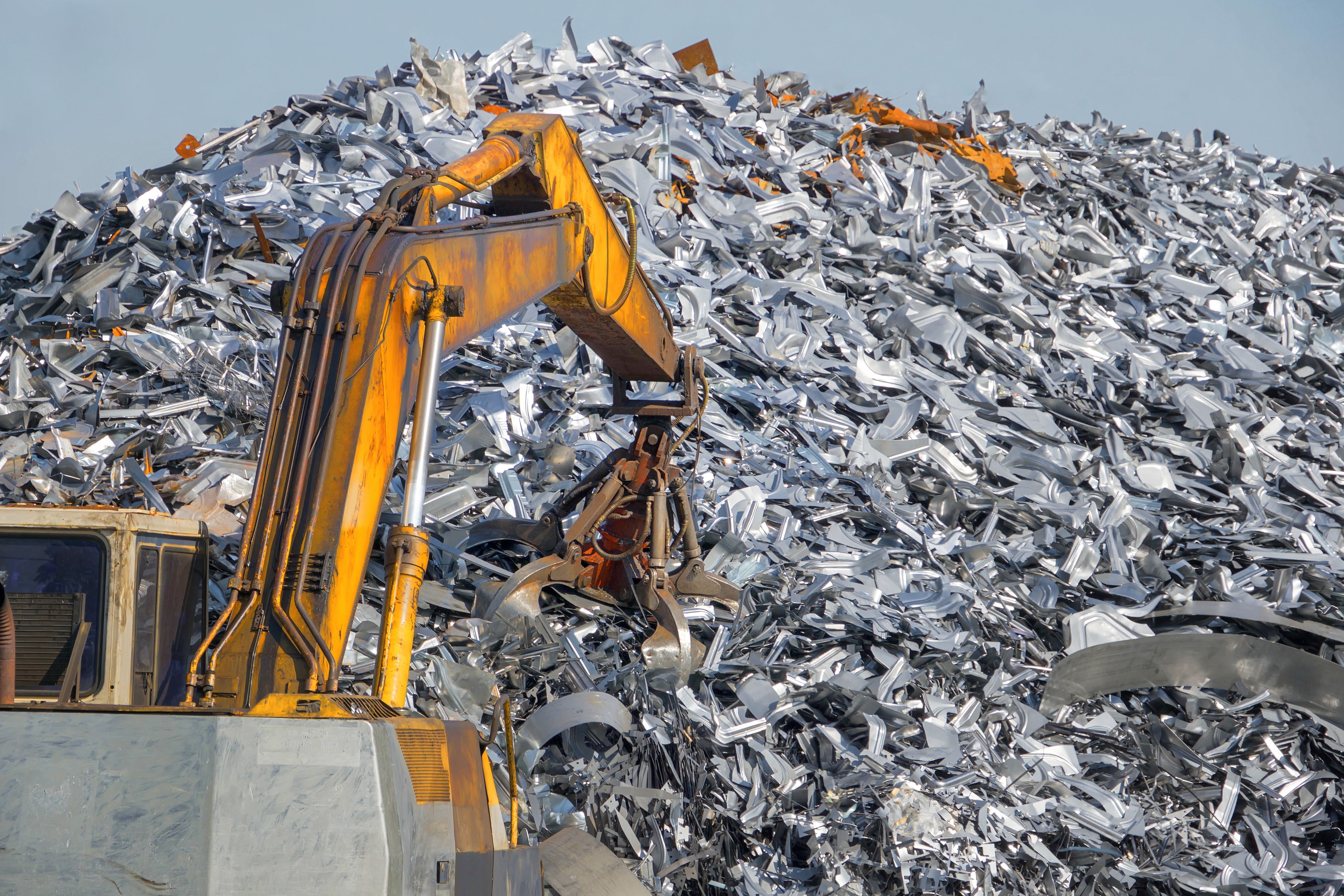
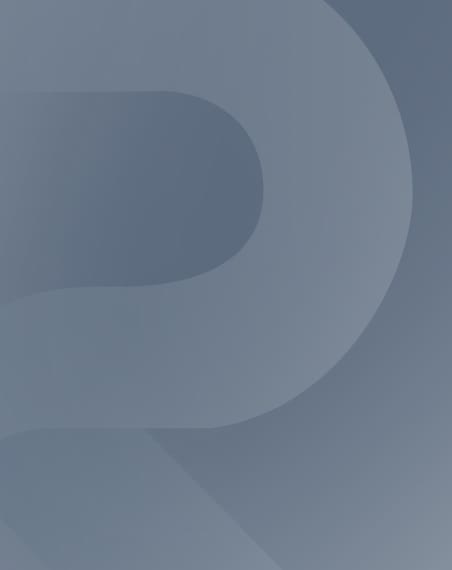
Global Recycling Day: Analysing the role of scrap in steelmaking through the years
To mark Global Recycling Day, Matthew Wenban-Smith reflects on the history of steel recycling and what it tells us about the transition to a net-zero steel economy in the future.
When it comes to recycling, it is worth taking the long view. For the first few thousand years, iron and steel recycling meant reworking rather than re-melting. The development of the blast furnace around one thousand years ago made it possible to convert steel scrap into liquid metal. And the first commercial Electric Arc Furnace (EAF), capable of using 100% scrap, was built in 1906.
Smaller, less costly to build, and more flexible to operate than blast furnaces, the spread of EAFs through the 20th century was limited only by the availability of scrap and electricity.
In the US, as demand for new steel approached saturation and as the steel in infrastructure and buildings constructed 40 or 50 years previously became available for recovery and recycling, scrap-based EAF production began to replace blast furnace steelmaking, even as the blast furnaces themselves used more scrap. Blast furnace production peaked in 1969, and no new blast furnace has been built in the US since 1980 (Construction Physics, 2023). Today, around 70% of steel in the US is made in EAFs (American Iron and Steel Institute, 2021).
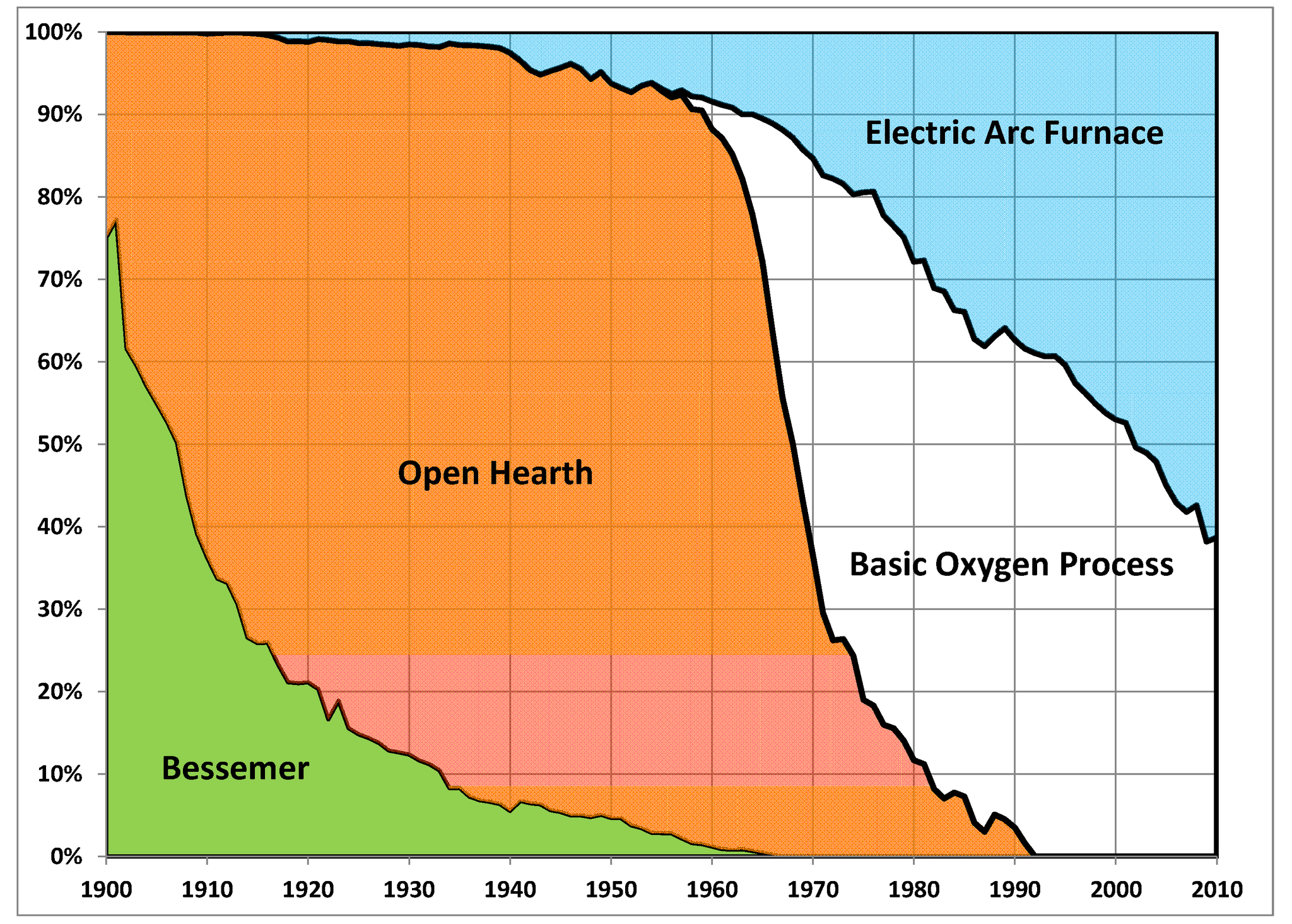
The same pattern of increasing demand, met initially from primary production and then later through a growing reliance on scrap, is now playing itself out in Europe and China, is set to take off in south Asia, and it is to be hoped will roll out across Africa. Steel production globally is projected to peak in the second half of the 21st century, with scrap supply following 30 or 40 years after that.
The growth of scrap-based production has been driven by economics, of course, rather than by any concerns about the climate or greenhouse gas emissions – but that doesn’t make it any less welcome. A tonne of steel made entirely from scrap has around one-fifth of the greenhouse gas emissions of a tonne of steel made from iron ore.
Does that mean we can all relax, and recycle our way out of the climate crisis? Sadly not.
The American Iron and Steel Institute (AISI) estimates that the USA now recycles between 70% and 80% of all of its potentially available scrap (AISI, 2021). The World Steel Association (worldsteel) puts the global recycling rate even higher than that, at around 85% for end-of-life scrap.
Then why, despite these impressive recycling rates, is there currently only enough scrap to meet around one-third of the global demand for steel? The main reason is that scrap availability reflects the level of steel production a generation ago, rather than today. Steel production in 1985 was around 720 million tonnes. Today it is around two billion tonnes. Even without taking account of end-of-life recovery and furnace yield losses there is no way to make those numbers add up.
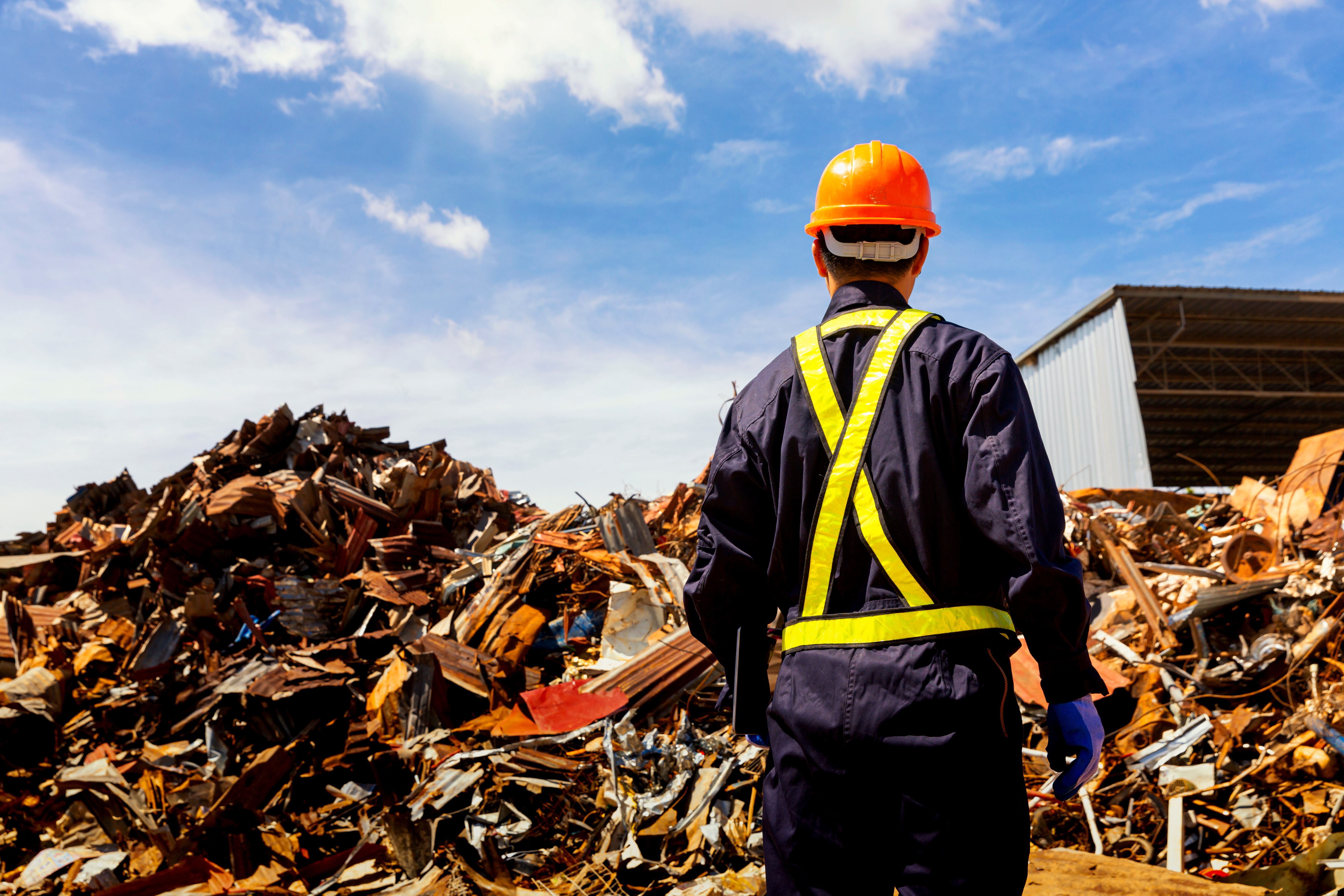
As demand for steel levels off in the future, a higher proportion of that demand will be met from scrap. In its ‘Sustainable Development Scenario’, in which the end-of-life recycling rate rises to 90%, the IEA estimates that there would be enough scrap to meet 45% of the demand for steel in 2050 (IEA, 2020). That is something to celebrate. But to put it the other way around, it would mean that 55% of the world’s steel – perhaps 1.2 billion tonnes of it – would still be made directly from iron ore.
To have any chance of limiting climate change to ‘well below 2 degrees’ and at the same time respecting the aspirations of 9 to 10 billion people, two things therefore need to happen. Firstly, the vast majority of primary steel will need to be made using ‘near zero’ emission sources of iron – using hydrogen-based direct reduction iron (DRI), direct electrolysis, biofuels, carbon capture or other new processes. And secondly, the electricity used in steelmaking will need to be generated with near zero emissions, whether it is used to power electric arc furnaces, hydrogen production, or direct electrolysis.
Those are the twin challenges for policy makers, steelmakers and steel users, and they apply across the whole sector.
To meet those challenges, they, and we, need to be able to compare the GHG emissions performance of all steelmaking on a like-for-like basis, whether steel is made from 100% scrap, 100% primary iron, or from any ratio of inputs in between – an approach pioneered in the ResponsibleSteel Production Standard, and recommended by the IEA, German Steel Association and others.
So let’s hear it for the recyclers, but also for the ‘near zero’ power generators, and the ‘near zero’ iron innovators.
And for a successful transition to a net-zero steel economy.
By Matthew Wenban-Smith