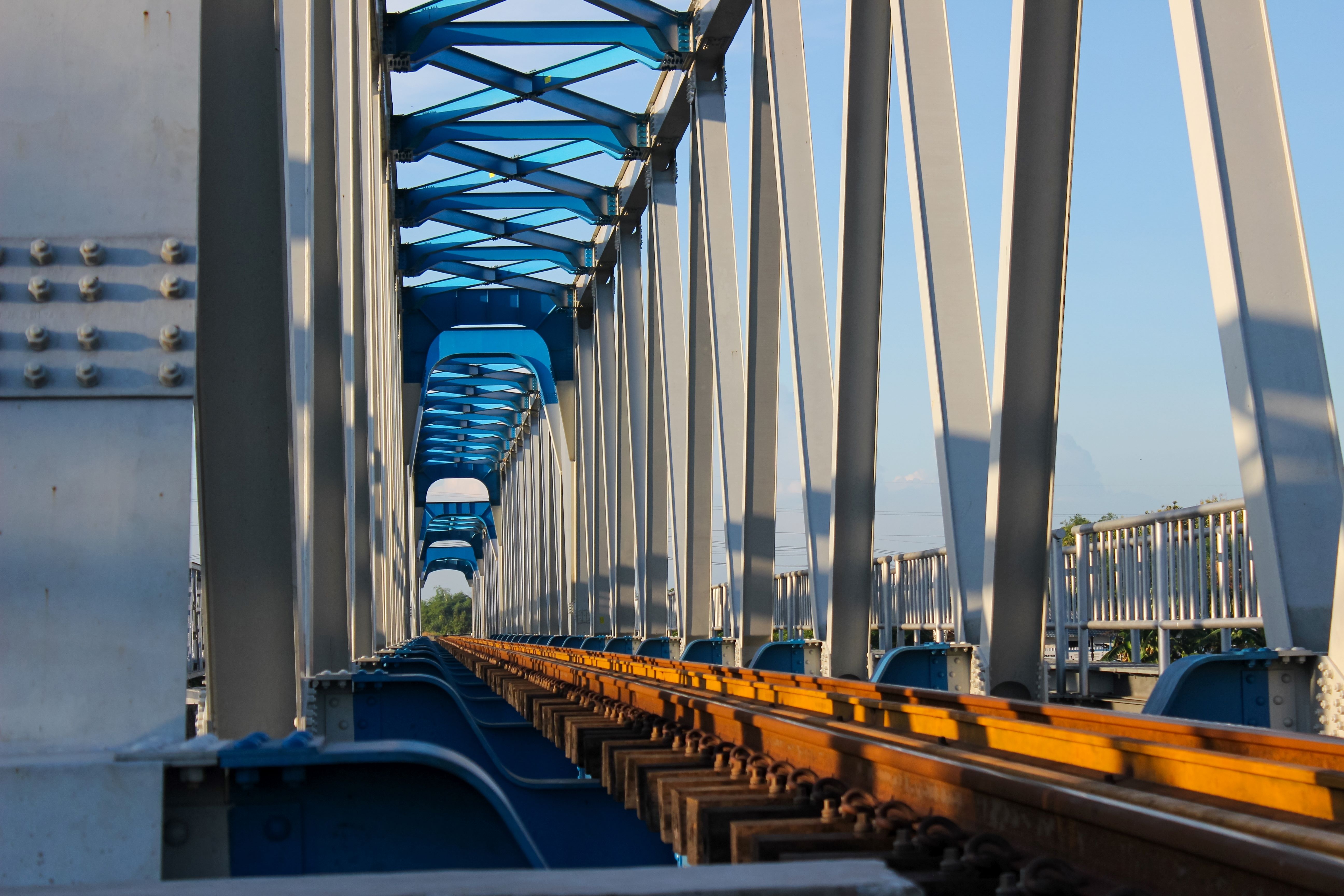
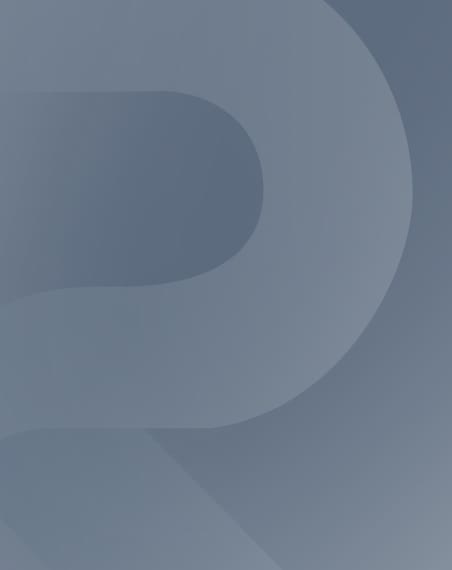
March 2025 Newsletter
This month, we were delighted to see JSW achieve its first ResponsibleSteel certifications for four sites in India, covering 83% of the company’s national steel production—an important milestone for Indian steel. And as steel policy continues to evolve rapidly worldwide, we've provided a summary of key developments from the EU, UK, China, and beyond.
We also celebrated International Women’s Day by highlighting the women driving change across the steel supply chain. In recognition of Global Recycling Day, we reflected on the history of steel recycling and the valuable lessons it offers in the journey toward responsible near-zero steel.
Additionally, we’re pleased to welcome three new members to the ResponsibleSteel community—PRCO America, ABS, and Yeşilyurt Demir Çelik. Welcome aboard!
In this newsletter, you will find updates on:
- New certifications
- New members
- Policy developments
- Upcoming audits and training
- Member survey results
- And more...
Click here to read the full newsletter.
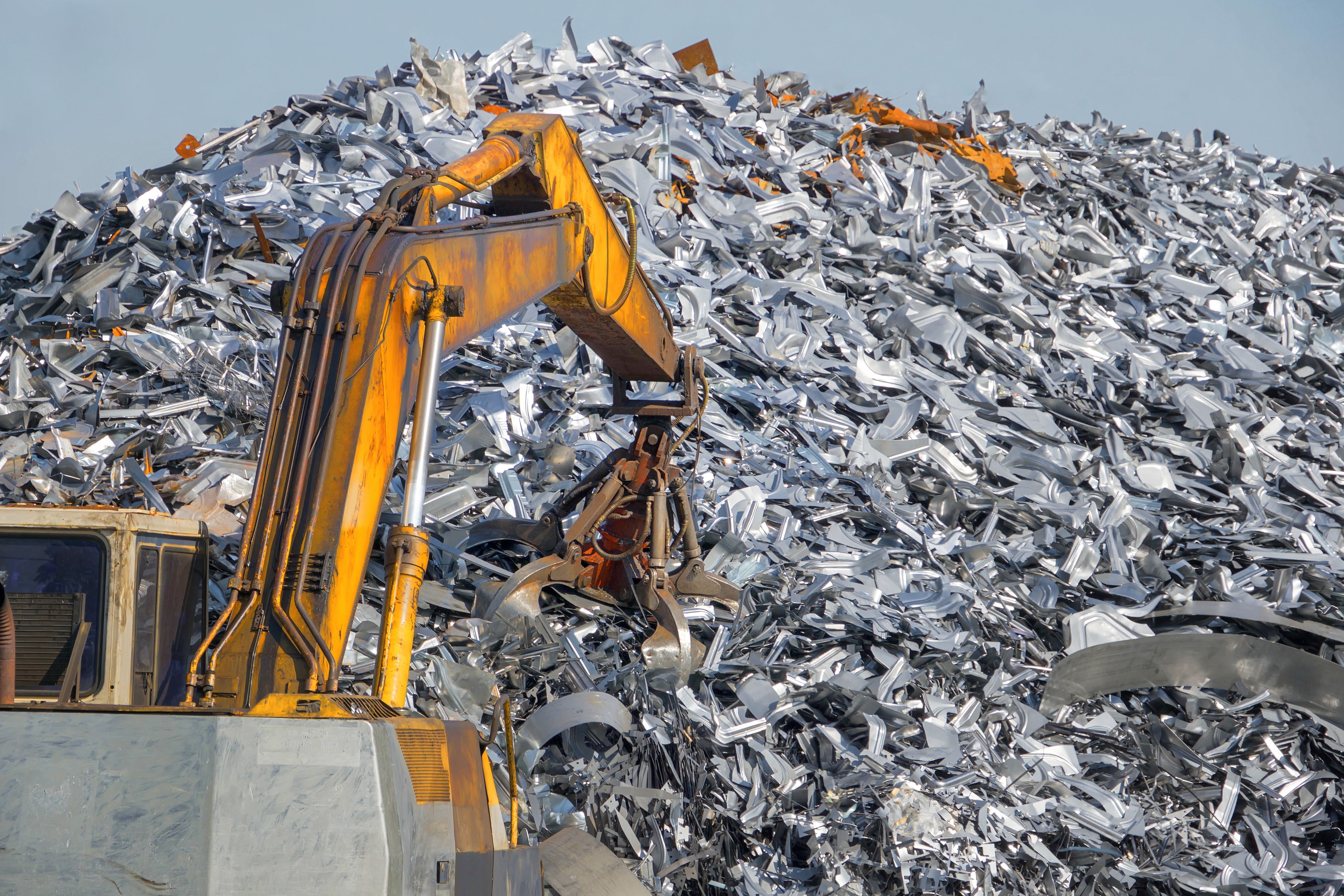
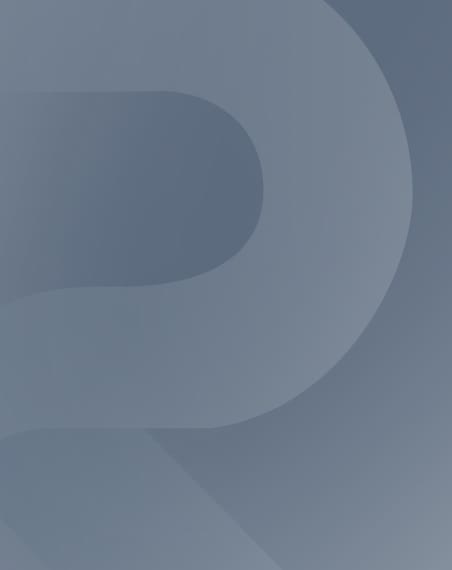
Global Recycling Day: Analysing the role of scrap in steelmaking through the years
To mark Global Recycling Day, Matthew Wenban-Smith reflects on the history of steel recycling and what it tells us about the transition to a net-zero steel economy in the future.
When it comes to recycling, it is worth taking the long view. For the first few thousand years, iron and steel recycling meant reworking rather than re-melting. The development of the blast furnace around one thousand years ago made it possible to convert steel scrap into liquid metal. And the first commercial Electric Arc Furnace (EAF), capable of using 100% scrap, was built in 1906.
Smaller, less costly to build, and more flexible to operate than blast furnaces, the spread of EAFs through the 20th century was limited only by the availability of scrap and electricity.
In the US, as demand for new steel approached saturation and as the steel in infrastructure and buildings constructed 40 or 50 years previously became available for recovery and recycling, scrap-based EAF production began to replace blast furnace steelmaking, even as the blast furnaces themselves used more scrap. Blast furnace production peaked in 1969, and no new blast furnace has been built in the US since 1980 (Construction Physics, 2023). Today, around 70% of steel in the US is made in EAFs (American Iron and Steel Institute, 2021).
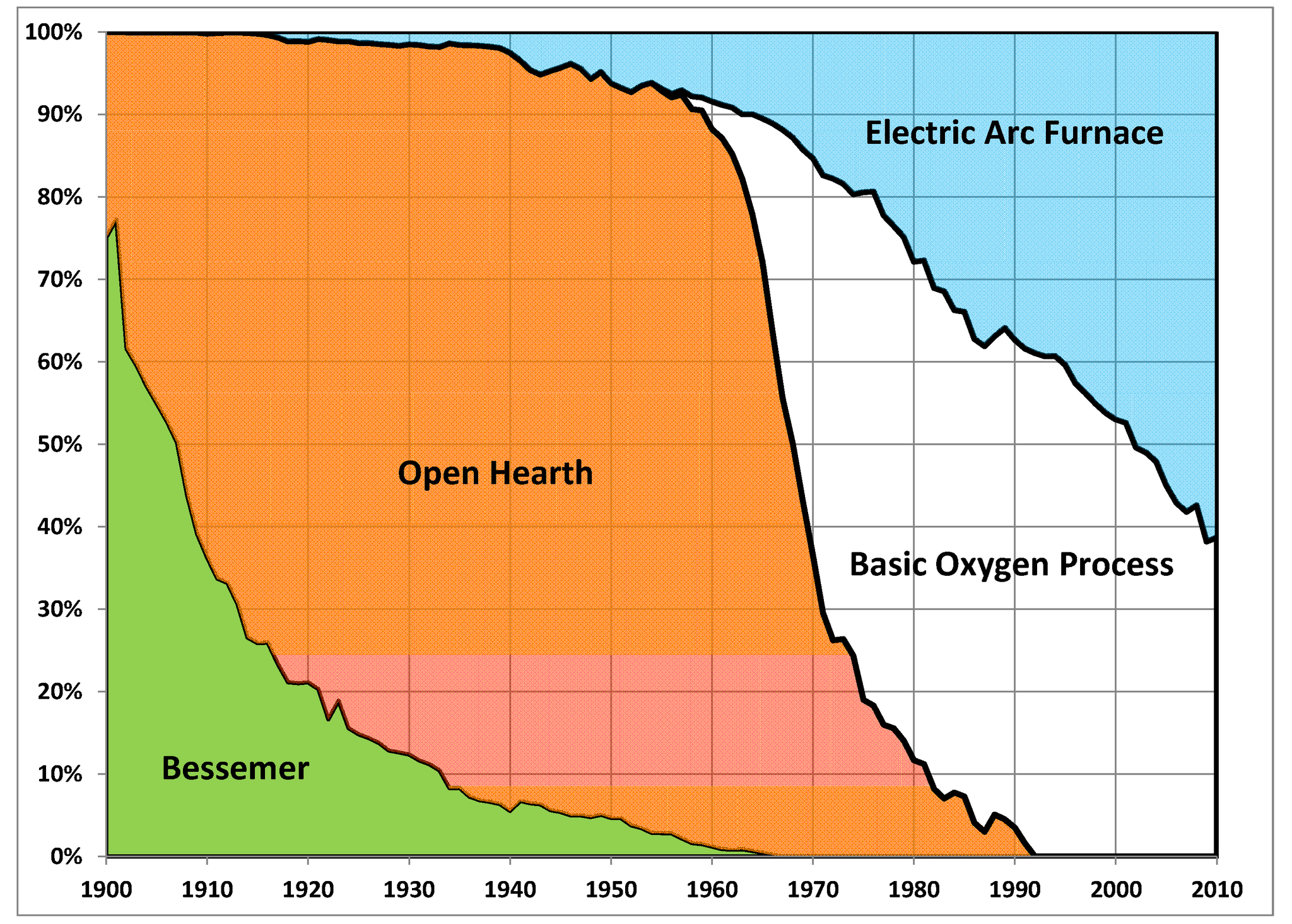
The same pattern of increasing demand, met initially from primary production and then later through a growing reliance on scrap, is now playing itself out in Europe and China, is set to take off in south Asia, and it is to be hoped will roll out across Africa. Steel production globally is projected to peak in the second half of the 21st century, with scrap supply following 30 or 40 years after that.
The growth of scrap-based production has been driven by economics, of course, rather than by any concerns about the climate or greenhouse gas emissions – but that doesn’t make it any less welcome. A tonne of steel made entirely from scrap has around one-fifth of the greenhouse gas emissions of a tonne of steel made from iron ore.
Does that mean we can all relax, and recycle our way out of the climate crisis? Sadly not.
The American Iron and Steel Institute (AISI) estimates that the USA now recycles between 70% and 80% of all of its potentially available scrap (AISI, 2021). The World Steel Association (worldsteel) puts the global recycling rate even higher than that, at around 85% for end-of-life scrap.
Then why, despite these impressive recycling rates, is there currently only enough scrap to meet around one-third of the global demand for steel? The main reason is that scrap availability reflects the level of steel production a generation ago, rather than today. Steel production in 1985 was around 720 million tonnes. Today it is around two billion tonnes. Even without taking account of end-of-life recovery and furnace yield losses there is no way to make those numbers add up.
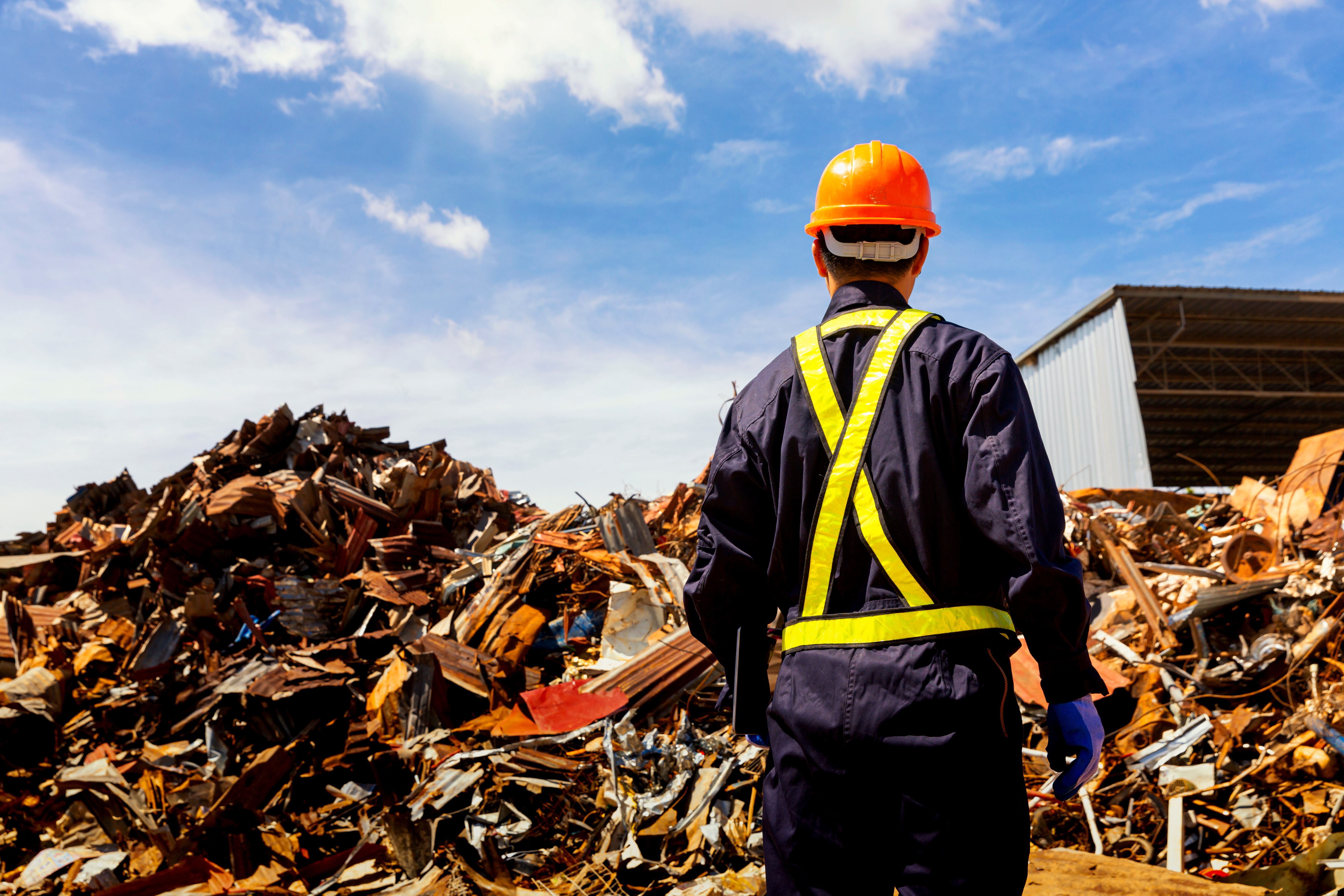
As demand for steel levels off in the future, a higher proportion of that demand will be met from scrap. In its ‘Sustainable Development Scenario’, in which the end-of-life recycling rate rises to 90%, the IEA estimates that there would be enough scrap to meet 45% of the demand for steel in 2050 (IEA, 2020). That is something to celebrate. But to put it the other way around, it would mean that 55% of the world’s steel – perhaps 1.2 billion tonnes of it – would still be made directly from iron ore.
To have any chance of limiting climate change to ‘well below 2 degrees’ and at the same time respecting the aspirations of 9 to 10 billion people, two things therefore need to happen. Firstly, the vast majority of primary steel will need to be made using ‘near zero’ emission sources of iron – using hydrogen-based direct reduction iron (DRI), direct electrolysis, biofuels, carbon capture or other new processes. And secondly, the electricity used in steelmaking will need to be generated with near zero emissions, whether it is used to power electric arc furnaces, hydrogen production, or direct electrolysis.
Those are the twin challenges for policy makers, steelmakers and steel users, and they apply across the whole sector.
To meet those challenges, they, and we, need to be able to compare the GHG emissions performance of all steelmaking on a like-for-like basis, whether steel is made from 100% scrap, 100% primary iron, or from any ratio of inputs in between – an approach pioneered in the ResponsibleSteel Production Standard, and recommended by the IEA, German Steel Association and others.
So let’s hear it for the recyclers, but also for the ‘near zero’ power generators, and the ‘near zero’ iron innovators.
And for a successful transition to a net-zero steel economy.
By Matthew Wenban-Smith
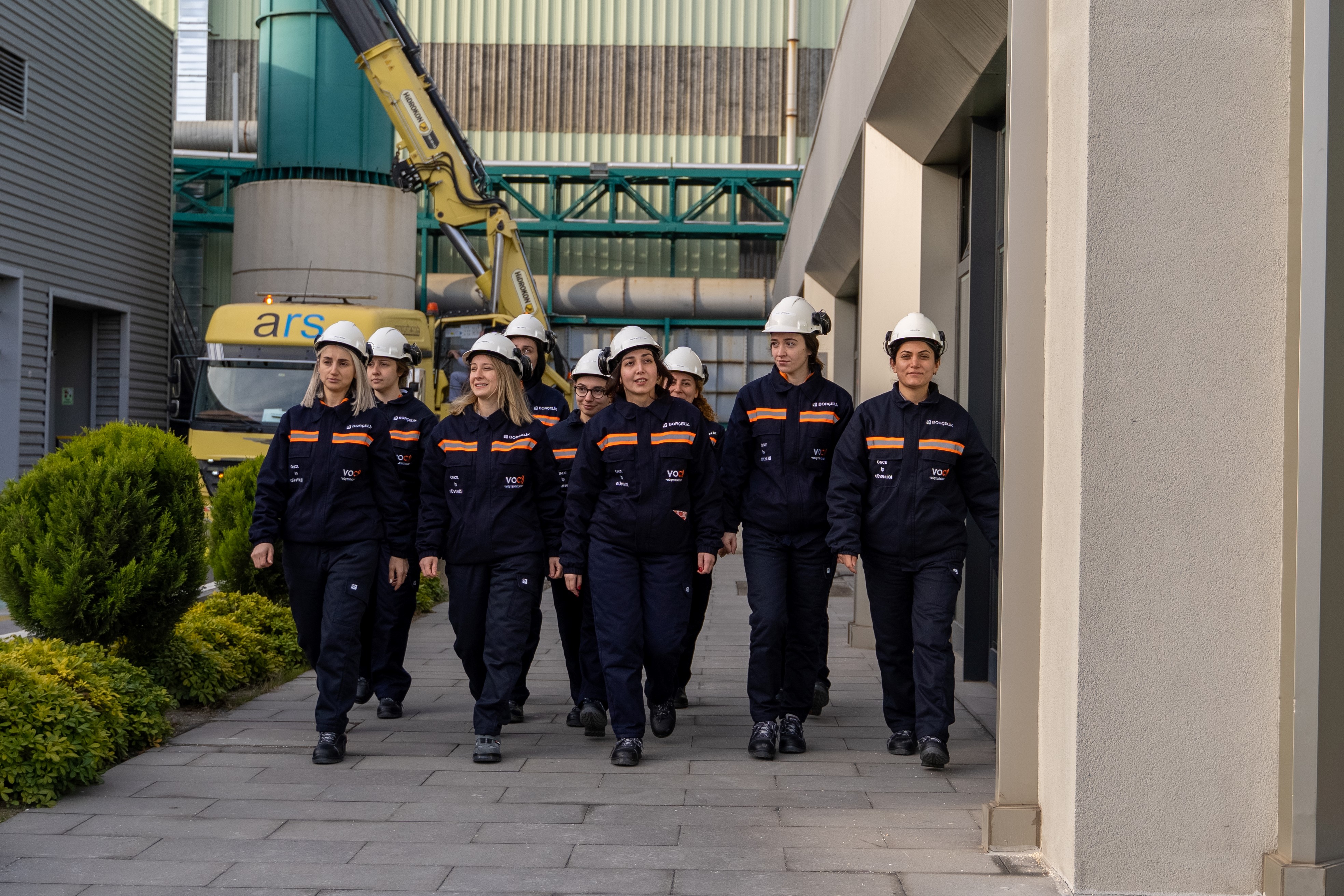
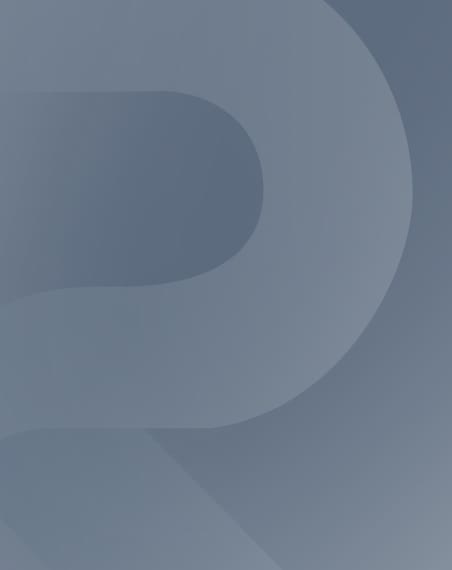
International Women's Day: Celebrating women working across the steel supply chain
In the second half of the twentieth century, women's participation in the global workforce grew remarkably. In the United States, female participation in the workforce surged from around 33% in 1948 to over 50% by the late 1970s (U.S. Bureau of Labor Statistics). Similarly in Europe, countries like France and Germany saw a rise from around 45% in the 1960s to over 60% by the 1980s (OECD, 2021). And in South America, Brazil also witnessed significant progress, with participation growing from approximately 18% in 1960 to 40% in 1980 (World Bank, 2020).
Despite these advancements, industries like steel, mining, and metals remained predominantly male-dominated. A 2019 broad analysis of 66 global steel, metals, and mining companies revealed that women made up between just 3% and 29% of the workforce (S&P Global). Within the steel industry specifically, women account for only about 15% of the workforce, a figure that has remained largely unchanged over the past decade (World Steel Association, 2020). These figures illustrate the persistent challenges to achieving gender diversity within the steel and metals sectors, underscoring the need for continued progress.
As workplaces evolve and diversity initiatives gain momentum, more women are entering and excelling in traditionally male-dominated sectors. Their contributions are driving innovation, improving workplace culture, and challenging longstanding societal barriers.
In recognition of International Women’s Day, ResponsibleSteel is spotlighting a few of the women who are driving change across the steel supply chain – celebrating their impact, resilience, and leadership and emphasising the need for greater diversity and inclusion in the metals sector.
Above image courtesy of Borçelik
.png)
Elle Gatto
Assistant Team Leader - Finished Product Shipping, ArcelorMittal Dofasco
Elle has been with ArcelorMittal Dofasco for just over five years. As an Assistant Team Leader in Finished Product Shipping, she's passionate about working on the floor and ensuring steel moves efficiently. Her department is the last line of defense - she takes great pride in knowing that her role contributes to guaranteeing that only the highest-quality steel reaches customers. For Elle, being part of a team that keeps production running smoothly is rewarding and motivating, and she's looking forward to continuing to grow in the industry.
What is it like to be a woman in the steel industry?
"Being a woman in the steel industry has its challenges, but also presents unique opportunities for growth and leadership. It's empowering to contribute to an industry that is traditionally male-dominated, proving that diversity leads to stronger teams and more creative solutions. While there may be moments of being one of the few women in the room, I see it as a chance to break barriers and inspire the next generation of women in manufacturing and engineering fields."
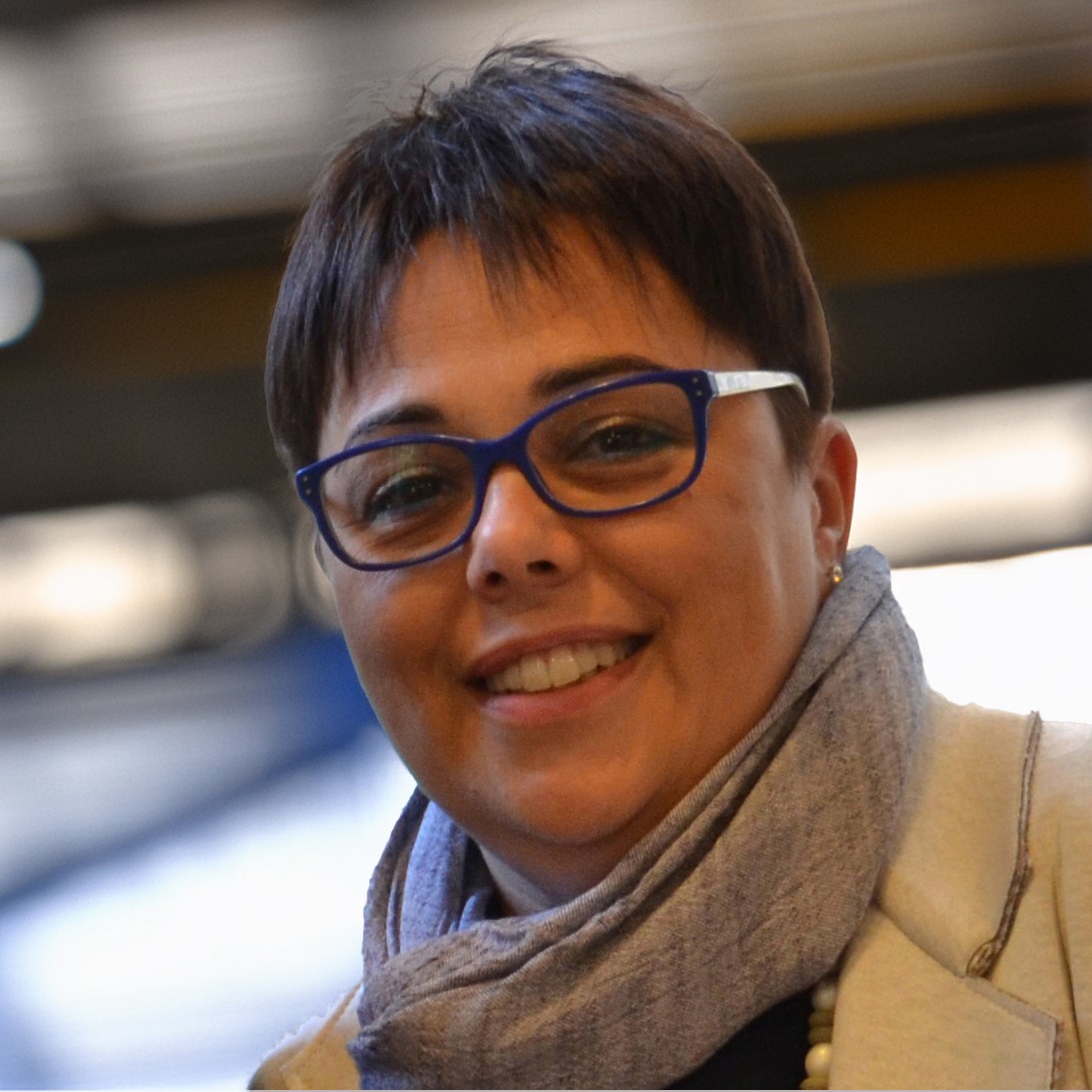
Stefania Bonaiuti
Supplier Carbon Neutral, SKF
Stefania began her 28-year journey at SKF working in bearing product lines and later serving as the marketing manager for steel-related offerings. Currently, she focuses on Supplier Carbon Neutral deployment. Her career spans sustainability projects aimed at achieving net zero carbon emissions. Her experience in the steel industry and commitment to promoting sustainable practices continue to play an important part in advancing SKF's sustainability initiatives. She values the diverse perspectives women bring to the industry and actively supports gender balance and leadership development programmes at SKF.
What are your hopes for the future of the steel industry?
"Over the years, I have encountered many women in this field who brought diverse perspectives and innovative solutions, which are valuable in an evolving industry. Therefore, ensuring gender diversity remains crucial.
The future of the steel industry holds immense potential, rooted in sustainability, innovation, and inclusivity. Embracing cutting-edge technologies will enhance efficiency and reduce environmental impact. At SKF, we drive innovation with steel products that support our customers' sustainability goals. Collaboration within the industry and with other sectors is essential for sustainable change. We are proud to be part of initiatives like ResponsibleSteel, SteelZero, and RE100. By sharing knowledge and leveraging each other's strengths, we can tackle challenges effectively and drive the industry towards a more sustainable and prosperous future."
It's empowering to contribute to an industry that is traditionally male-dominated, proving that diversity leads to stronger teams and more creative solutions. - Elle Gatto, ArcelorMittal Dofasco
Tuana Çabuk
Production Engineer - Continuous Galvanizing Line, Borçelik
Tuana graduated with a degree in Mechanical Engineering. She has been working as a Production Engineer in the Continuous Galvanizing Line at Borçelik for two years. As a production engineer, she takes part in projects related to occupational safety, production processes, and quality performance of the lines she is responsible for.
What is it like to work in the steel industry?
"The steel industry is highly competitive and involves production processes that require advanced technology. As a result, it demands strong expertise in both engineering and production. Being actively involved in production processes and participating in various projects helps me to develop myself to be a better engineer. Since the steel industry is dynamic and requires technical proficiency, I believe that taking an active role in the manufacturing field, especially as a production engineer, provides a significant advantage.
Although the workforce is predominantly male, I take pride in contributing to the industry and promoting diversity as a female engineer. Gender diversity is a crucial issue, but I believe it should not be measured by having an equal number of men and women in every setting. Instead, it should be achieved by ensuring equal opportunities and a fair working environment for everyone. I feel fortunate to work in an organisation that supports this principle."
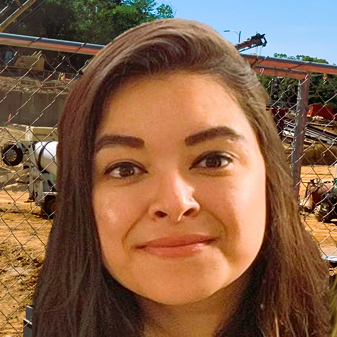
Dr. Ankita Gangotra
Senior Manager, World Resources Institute US
Ankita leads WRI's efforts to decarbonise the industrial sector through technology and policy innovation. Her work focuses on decarbonising the cement and steel industries, climate-oriented trade policies, green procurement standards, and fostering international cooperation. Ankita’s work includes advising U.S. policymakers and supporting industrial decarbonisation efforts in countries like India. Previously, she was a postdoctoral research fellow at Georgetown University, where she researched technology and policy options for industrial decarbonisation in the U.S.
What is it like to be a woman working on steel and heavy industry?
"I was apprehensive when starting work on the steel and industrial sector more broadly due to its male-dominated nature, but I’ve been inspired by the incredible women working on steel decarbonisation and their fierce advocacy. It’s been empowering to be surrounded by such passionate colleagues who are driving meaningful change. I hope we can accelerate the pace of steel decarbonisation while ensuring a just and equitable transition that benefits both communities and workers in the sector."
It's been very nice being a mentor and a point of call for other women. I like to think I've made other women in the industry proud. - Ashlea Muscat, BlueScope
Ashlea Muscat
Operations Manager Painting and Finishing Department, BlueScope
Ashlea joined the industry as a cadet in 2014 straight from university. After eleven years in the industry, she now runs the coil painting and finishing department at BlueScope’s Port Kembla Steelworks, looking after 126 people across 3 units and leading on day-to-day management, development, and process improvement across the department. Women now make up over 22% of BlueScope's site operators, a significant increase from 3% in 2017.
How did you get started in the steel industry?
"I first began in the industry as a cadet and I love all of the problem solving and challenging roles that I've held. It's been very nice being a mentor and a point of call for other women. I like to think I've made other women in the industry proud."
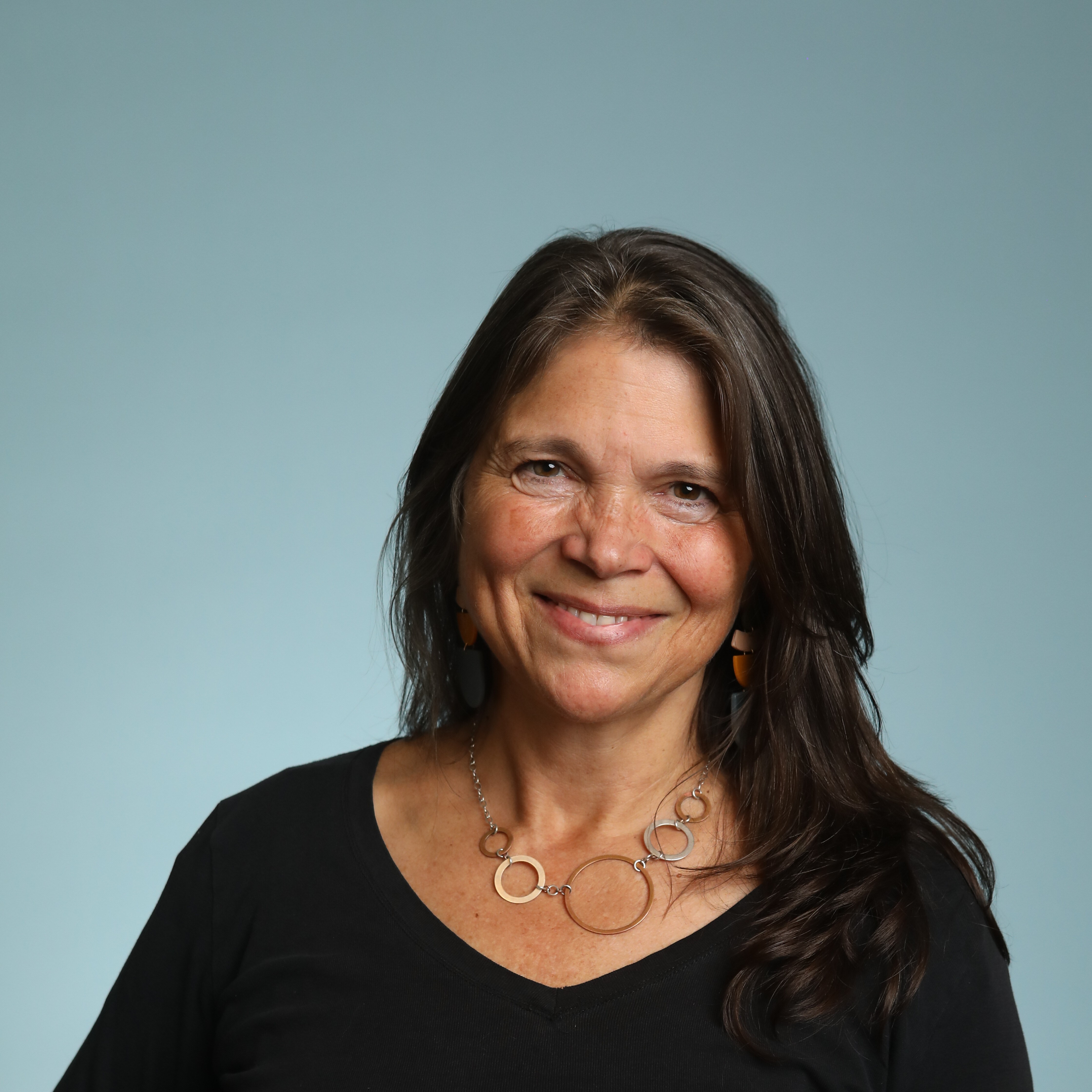
Aimee Boulanger
Executive Director, Initiative for Responsible Mining Assurance
Aimee has worked on mining issues for over 25 years, with substantial experience in directly affected communities. She has served IRMA’s leadership since 2011 and her role is to guide an organisation which is fully accountable to multi-stakeholder leadership, creating market value for more responsible business practices while ensuring credibility and accountability to all stakeholders.
What are your hopes for the future of the steel and mining sectors?
"I hope for a future where companies that create the products we rely on every day are valued not just for what they make, but for how they make it, ensuring that people, their lands, and their wellbeing are respected at every step. This means greater transparency in industries like mining and steel, so we acknowledge our shared impact and work together to reduce harm. And as we do, I hope we centre the voices of women—whose leadership, labour, and lives are so often overlooked—so that the benefits of industry are shared more equitably by all."
I hope for a future where companies that create the products we rely on every day are valued not just for what they make, but for how they make it... And as we do, I hope we centre the voices of women—whose leadership, labour, and lives are so often overlooked—so that the benefits of industry are shared more equitably by all. - Aimee Boulanger, IRMA
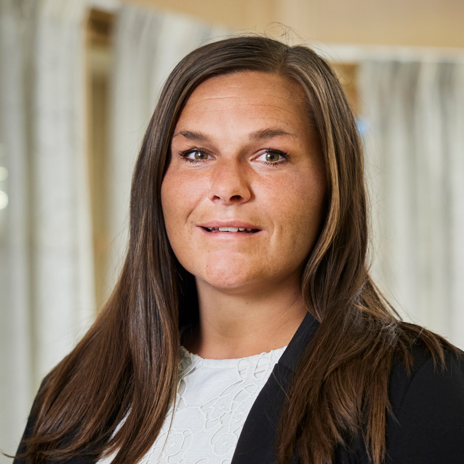
Angelica Olsson
Manager - Safety and Sustainability, Outokumpu
Angelica has worked her whole career in different types of industries. Before joining Outokumpu, she worked for several years in the paper industry as well as in the sawmill industry. She's held various positions, but she has the most experience in Supply Chain Management. She joined Outokumpu in 2018 and her first role was as a Safety Engineer for fire and security issues. Since 2022, she has worked as a Safety & Sustainability Manager.
What is it like to work in the steel industry?
"The steel industry has been by far the most interesting and challenging industry that I’ve worked in. The products we produce are fascinating and we all need to work every day to ensure that the way we produce steel is safe and sustainable. In my role as a Safety & Sustainability Manager, I’m fortunate to work with a great team of safety and sustainability engineers, and together we work hard every day, enabling our mills to produce safe and sustainable stainless steel. I really feel that the work we do makes a difference."
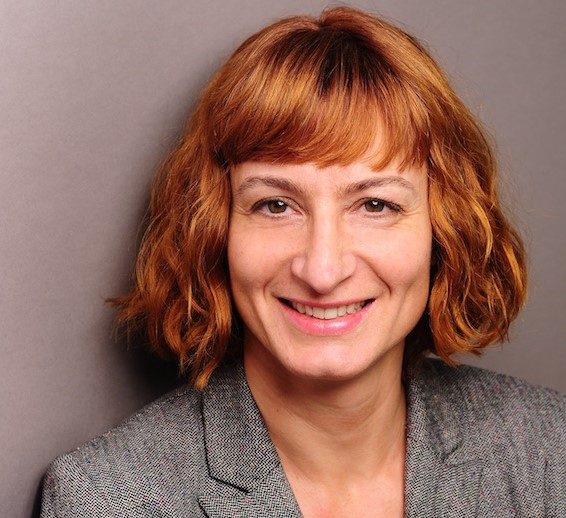
Marnie Bammert
Independent Consultant to ResponsibleSteel
Marnie is an independent consultant with 20 years of experience in developing, implementing and communicating sustainability certification and verification programmes. She has worked with ResponsibleSteel since early 2018. Marnie started her journey in the field of sustainability with oekom Research AG, a rating agency specialised in sustainable and ethical investments. She then moved to the Marine Stewardship Council (MSC), holding various positions including Deputy Director Europe. Since then, Marnie has worked as a consultant on projects ranging from protected areas to infrastructure, mining and nature-based solutions.
Why did you first begin working on the steel industry?
"People tend to focus on GHG emissions when discussing sustainability challenges of the steel sector. But the climate crisis cannot be solved in isolation. Working with ResponsibleSteel, I wanted to raise awareness for other important issues that the sector faces - human and labour rights, biodiversity, water stewardship, to name just a few. They are all connected to the climate question. I am proud to have played an instrumental part in creating the ResponsibleSteel Standard since it brings all of those issues together."
I envision a future for steel where much greater systems thinking, as well as intra- and inter- sector collaboration, drives progress - all enriched by the leadership of women. - Jen Carson, Climate Group
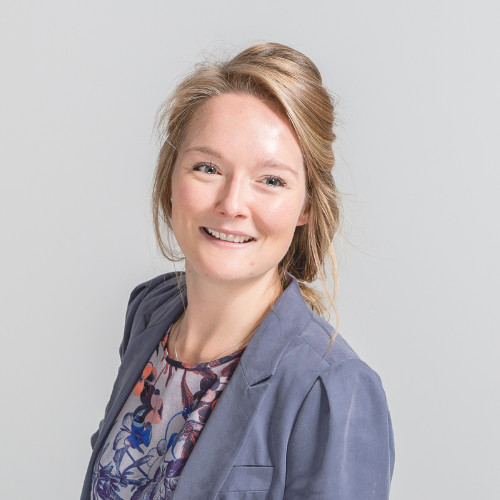
Jen Carson
Head of Heavy Industry, Climate Group
Jen Carson leads the strategy and growth of Climate Group's SteelZero and ConcreteZero. With a decade's worth experience working in the sustainability sector, she works to accelerate heavy industry decarbonisation. Jen joined Climate Group in 2021 after leading energy market research as an Associate at Delta-EE in Australia. Previously, she held various roles at Delta-EE, including creating its first cross-technology research service, as well as at The Carbon Trust, Dunelm Energy, and Kier Group.
What are your hopes for the future of the steel industry?
"I envision a future for steel where much greater systems thinking, as well as intra- and inter- sector collaboration, drives progress - all enriched by the leadership of women. By elevating the contribution of the demand side, and championing a competitive, decarbonised future, we will build a resilient steel industry that sets new standards for what is and isn't acceptable."
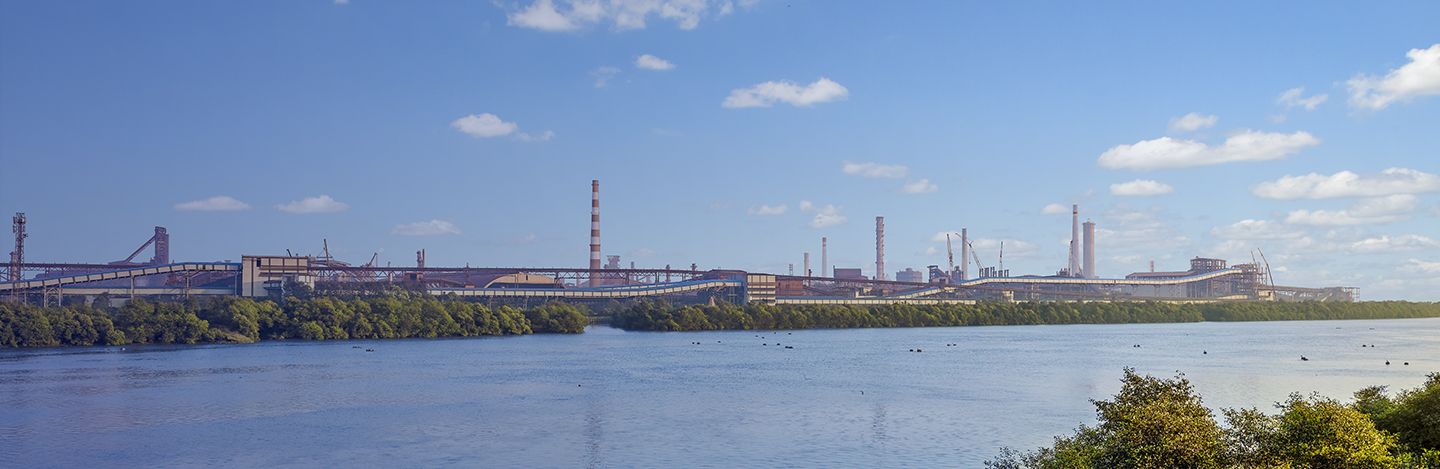
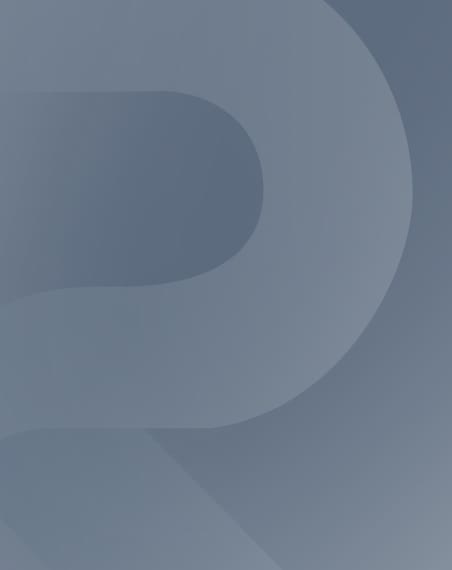
JSW Steel achieves its first ResponsibleSteel certifications for four sites
JSW Steel has achieved Core Site Certification for its Vijayanagar, Dolvi, Salem and Tararpur sites - the group's first certifications against the ResponsibleSteel International Production Standard.
Over the last four decades, JSW Steel has gone from a single unit to a leading steel producer with operations across India and the US. The company's Vijayanagar site has the largest single-site steelmaking capacity in India, able to produce up to 13 million tonnes per annum. The certification of Vijayanagar along with three other sites means that JSW Steel now has 83% of its steel production in India covered by ResponsibleSteel Core Site Certification.
Jayant Acharya, Joint Managing Director of JSW Steel, commented, "The ResponsibleSteel Certification for our 4 sites is a testament to our unwavering resolve to future proof our business by addressing the emerging global challenges while we transition to a sustainable world. I congratulate the team of ResponsibleSteel, the certification body, the assurance panel, and the entire family of JSW Steel for achieving this milestone. We are committed to certifying all our steelmaking sites by 2028."
JSW Steel serves customers across the automotive, machinery, construction, and engineering industries. Together, the four sites employ over 13,000 workers and 29,000 contractors.
Annie Heaton, CEO of ResponsibleSteel commented “Congratulations to JSW for achieving these four ResponsibleSteel certifications. By choosing to adopt an international standard which addresses not only emissions but a wide breadth of environmental and social issues, JSW is demonstrating ambition, foresight and leadership as a global industry player. This means being open to external monitoring, being ready to engage on opportunities for improvement with local stakeholders and laying the foundations for a responsible transition to near zero. As the second largest steel producing country globally, India has a real opportunity to emerge at the helm of the industry’s shift to sustainable practices. JSW's certifications mean that today we’re proud to have some 29% of India’s steel capacity certified against the ResponsibleSteel International Production Standard. We look forward to their next steps in deepening this journey.”
In addition to consulting workers and contractors as part of the audit, several external stakeholders were involved in the process. Representatives from local police, government, NGOs, schools, colleges, hospitals and citizen forums were invited to give input to the audit. Stakeholders had the opportunity to discuss the performance of the site in relation to health and safety, training opportunities, environmental issues, and the site's impact on the local community.
Take a look at the certificates and public audit summaries here.
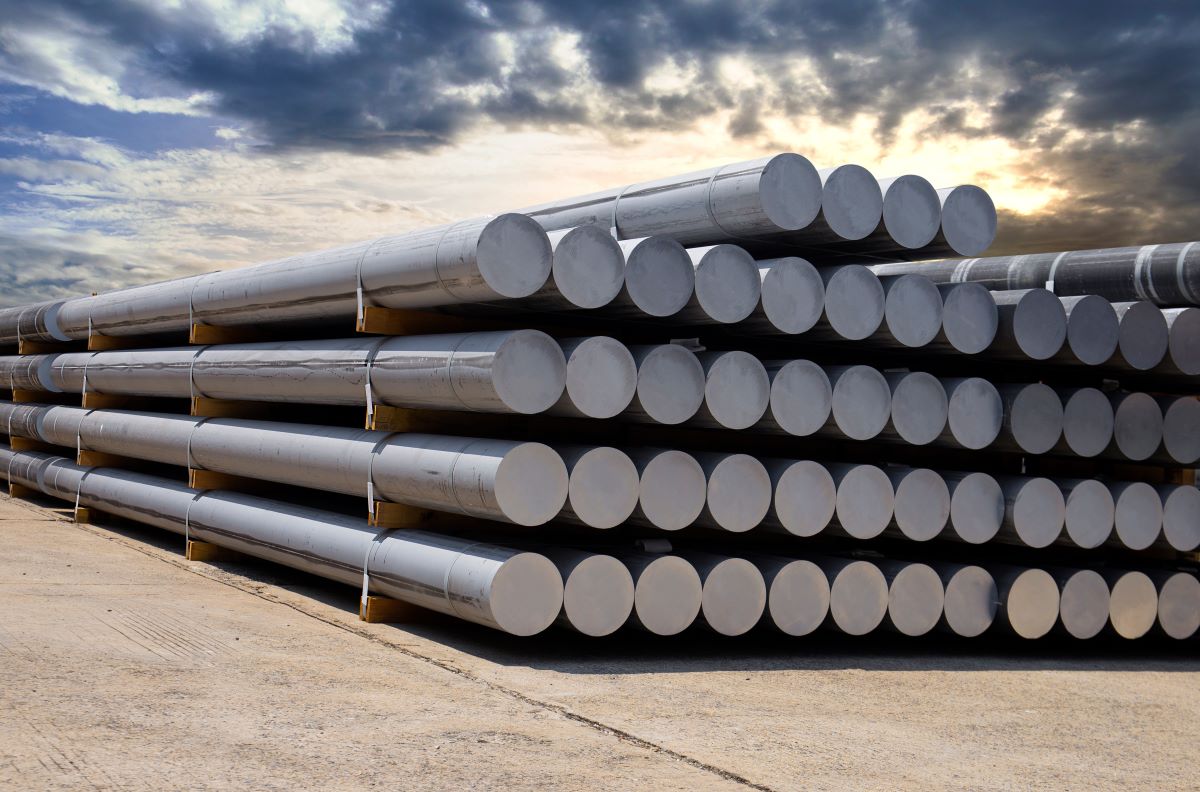
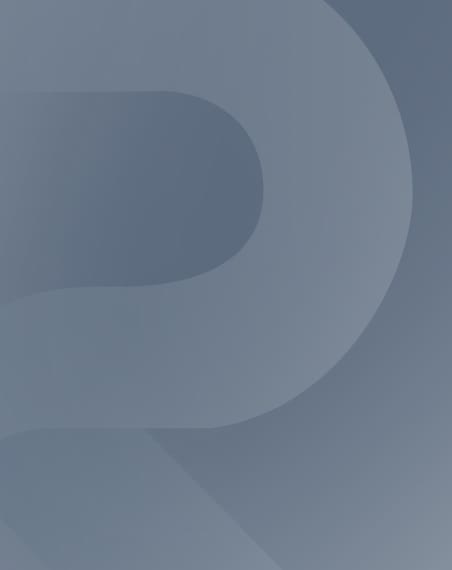
February 2025 Newsletter
This month, we’re excited to share valuable new resources with members and stakeholders to help you talk about ResponsibleSteel. Our new explainer video highlights the value of our programme, and we’ve published several guides on key areas - perfect for sharing with your internal and external stakeholders.
The survey results are in, offering insights to shape our priorities for the year ahead. Auditors can now join our first training sessions of the year for a deeper dive into the Core and Progress Level requirements, and we have published a blog examining our project on standards' role in a just transition.
In this newsletter, you will find updates on:
- Our new animated explainer
- Upcoming auditor training dates
- Events we are attending
- Our new guides to ResponsibleSteel
- Member survey results
- And more...
Click here to read the full newsletter.
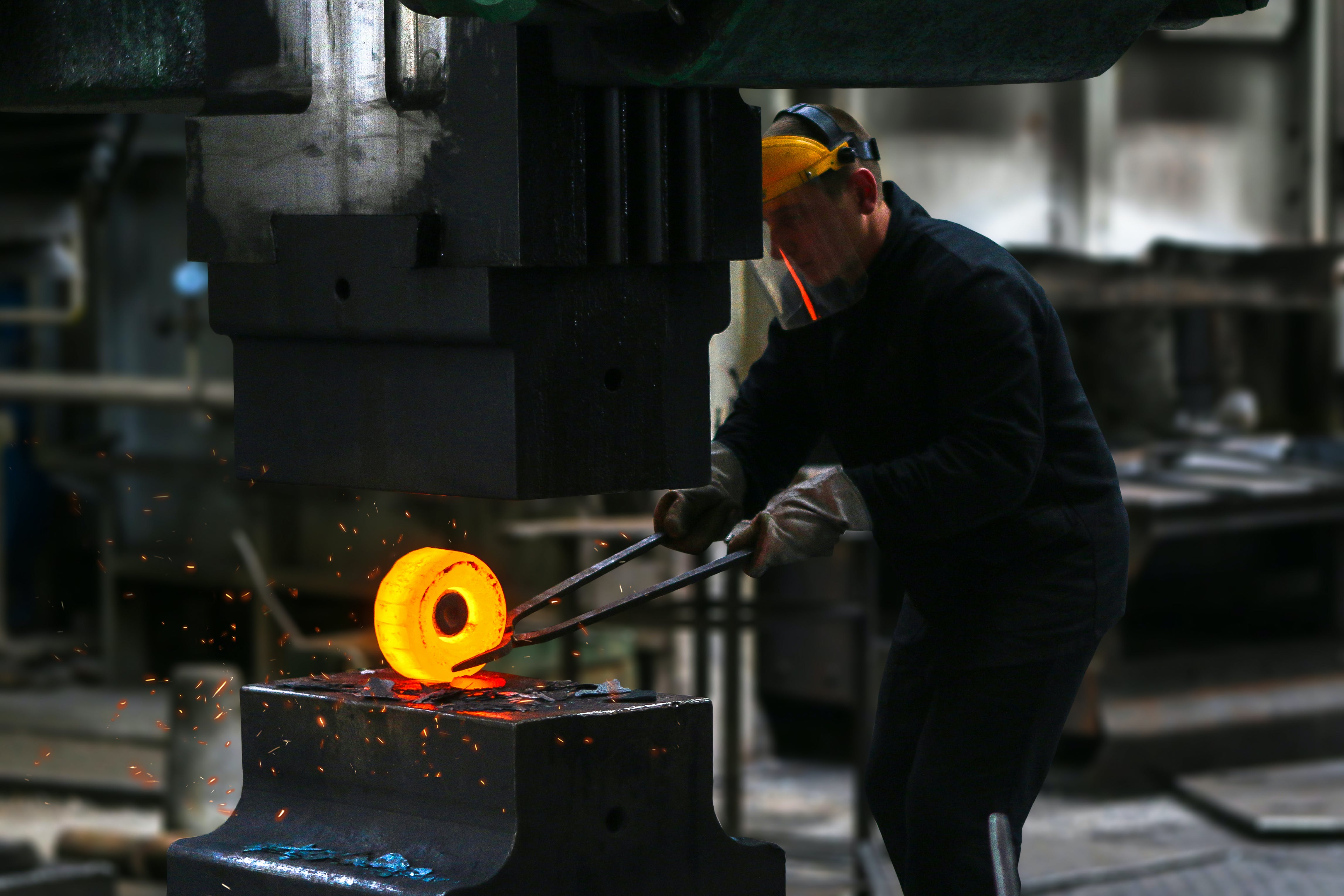
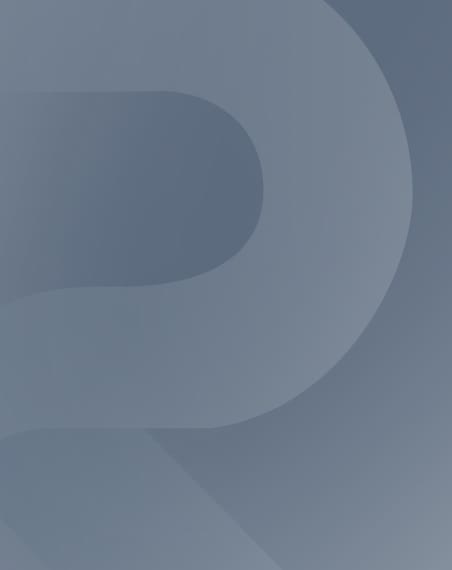
In conversation with IRMA and ResponsibleSteel: Exploring the role of standards in driving a responsible transition in steel and mining
ResponsibleSteel and the Initiative for Responsible Mining Assurance (IRMA) are collaborating on a joint project to better understand the social impacts of the net-zero transition for the steel and mining sectors and how standards can help guide good practice. This project is possible thanks to a grant from the ISEAL Innovations Fund, which is supported by the Swiss State Secretariat for Economic Affairs SECO.
We have asked the two project leads, Haruko Horii, Standards Manager at ResponsibleSteel, and Davidzo Muchawaya, Africa Regional Lead at IRMA, to answer a short Q&A for readers to better understand the project itself.
Q: Haruko, what is the vision for the project?
With this project, we want to understand the social impacts of the transition to net zero and what role standards can play in guiding good practice.
The term ‘just transition’ is used by different people in different ways. We need to determine what this looks like for the mining and steel sectors. What exactly is a just transition? Whose transition are we discussing? Workers, local communities or supply chains? What is the scope of transition? These are some of the questions we need to consider.
Decarbonisation could have adverse social impacts such as job losses or displacement and significant effects on weakening the economic viability of affected communities. Initial research has shown that communities are facing significant social impacts caused by the transition to low-carbon practices. For instance, thousands of people have lost their jobs as a result of shifting from blast furnace technology to electric arc furnaces. These job losses have in turn impacted the wider community’s economic stability, community identity, and overall well-being.
These are the types of issues we aim to identify through this project, assessing how voluntary sustainability standards (VSS) can address them, identifying gaps, and outlining steps for future, more detailed work that could lead to larger-scale initiatives. We’ll test our findings by engaging with workers, unions, business leaders, community organisations, and other relevant stakeholders to identify an agreed approach and create practical guidance for players in the mining and steel industry.
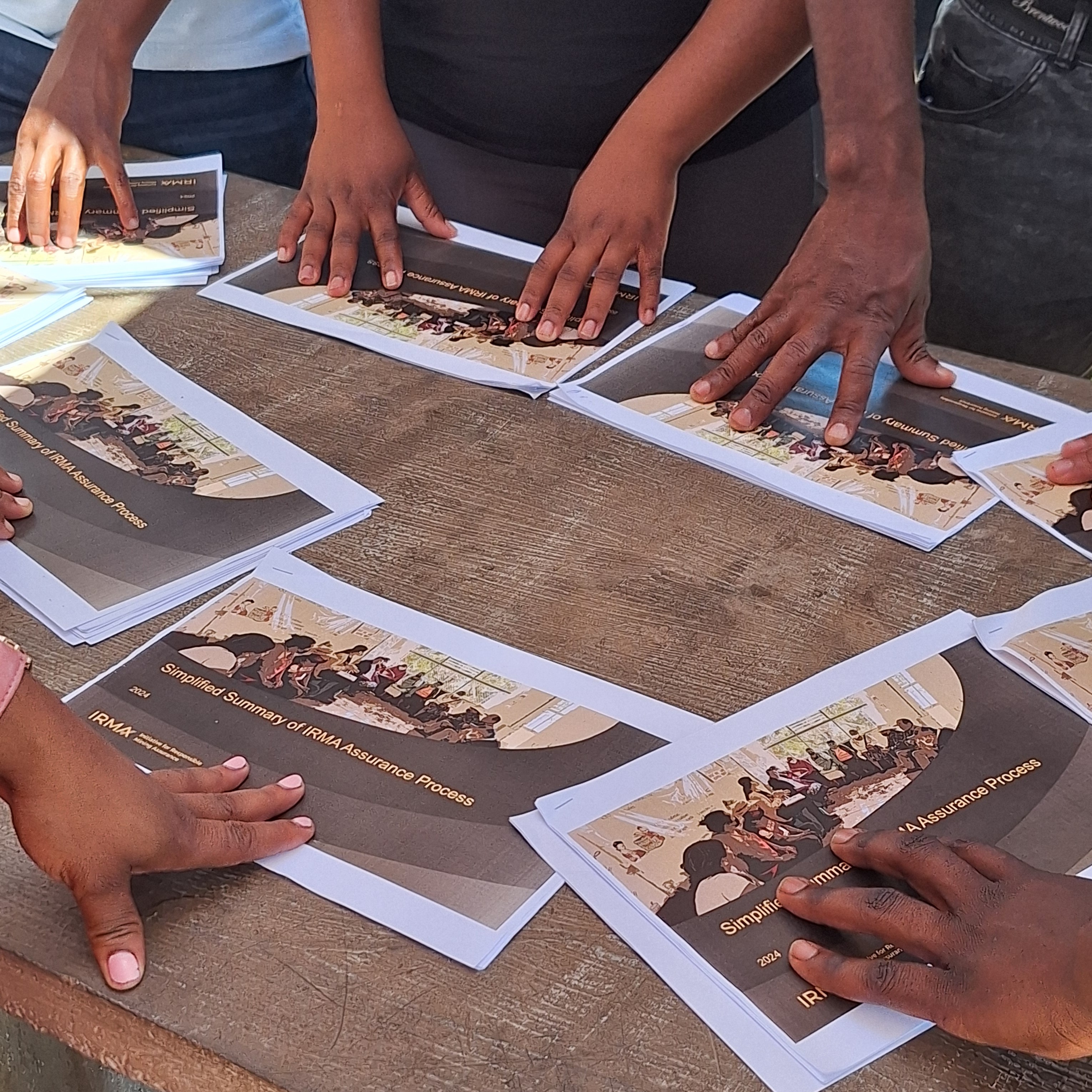
Q: Davidzo, what do ResponsibleSteel and IRMA have in common, and why are they collaborating on a just transition?
We believe in the power of collaboration and mutual recognition. This project is just one of many examples of how different voluntary sustainability standards can complement and leverage each other's work. Specifically, ResponsibleSteel leverages the assurance system of standards such as IRMA’s at mine site level, while focusing on the steel production aspects. Importantly, both ResponsibleSteel and IRMA were founded on a multi-stakeholder governance system, which has been recognised as a leading practice both by industry and NGOs. This model is recognised as best practice to ensure transparency, accountability, and inclusivity.
The collaboration specific to a just transition is born out of the necessity to ensure two hard-to-abate sectors, steel and mining, address the realities workers and communities are facing in our changing world as many existing mine and steelmaking sites face adaptation or closure. Given the varying impacts of decarbonisation across regions, IRMA and ResponsibleSteel are uniquely positioned to provide frameworks that apply across these different contexts since they are both standard-setting organisations operating globally. What is more, they are able to consider both decarbonisation and the potential social impacts of the transition at the same time.
Q: How do each of you respectively integrate just transition into your standards?
Haruko: Standards are going to play a critical role in promoting accountability during the transition ensuring they are fair and equitable. Although there is no explicit reference to a just transition in the current ResponsibleSteel International Production Standard, there are some elements to address the transition under Principle 4: Decommissioning and Closure, which requires consultation with key stakeholders to minimise any adverse impacts of site closures. In future, the scope of this principle could be expanded to address issues related to site closures, or the Production Standard could adopt a different approach by providing a just transition framework giving steel producers guidelines and tools to navigate an equitable transition with workers and affected communities. We plan to discuss these approaches with stakeholders in the next phases of the project. Integrating practices into the Production Standard will help ensure the industry’s transition is both environmentally and socially just.
Davidzo: As for the IRMA Standard for Responsible Mining, multiple chapters and requirements articulate what best practices could and should be for mining operations wishing to ensure a just transition for workers and affected communities. A prominent example is the requirement to involve affected communities and stakeholders in the development, design, and implementation of the mine rehabilitation and closure plan. Going beyond minimum transparency, the IRMA Standard outlines a series of requirements dedicated to the adequate estimation and financing of mine closure and post-closure. Research shows that mining operations often leave behind environmental and social liabilities, without taking charge of costs associated with the rehabilitation or appropriate closure of the sites thereby foregoing an adequate transition.
Crucially, the role played by both ResponsibleSteel and IRMA would not be the same without their multi-stakeholder governance systems. Thanks to the decision making process that takes into account private sector players as well as rights holders and labour unions, they can ensure that the voices of all parties are heard and taken into account in an equal way - hopefully adding the “just” element to “transition”.
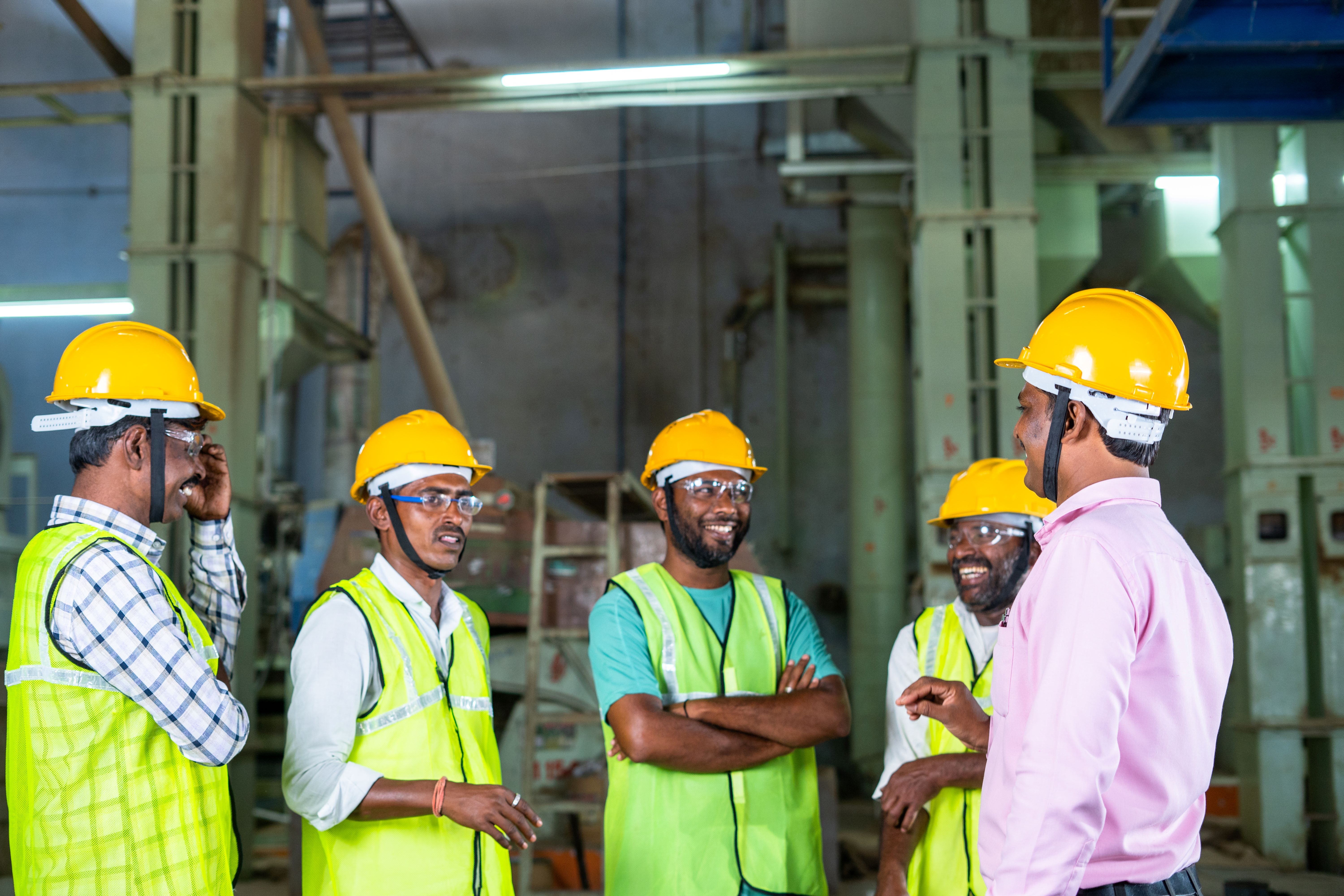
Q: Davidzo, who is the main audience for this project?
The main audience for this project is workers and labour unions, as workers are most directly affected by the transition. Operators, from mining companies to steelmakers, are also key since, as employers, their actions and decisions will be critical to the social impacts of the transition, alongside national and subnational governments. Local communities impacted by the transition, NGOs that aim to act in their interests and standard-setting organisations are also key stakeholders.
Q: Haruko, is there a specific geographic focus for the project?
While just transition challenges and opportunities vary from country to country and even from site to site, the project is truly global as it strives to bring the complexities of these different realities to light. We aim to engage with stakeholders across different regions during the project to hear about the realities of the transition in different contexts. More information on this to come!
To find out more about IRMA, visit responsiblemining.net. To find out more about the project background, visit this page on the ISEAL website.
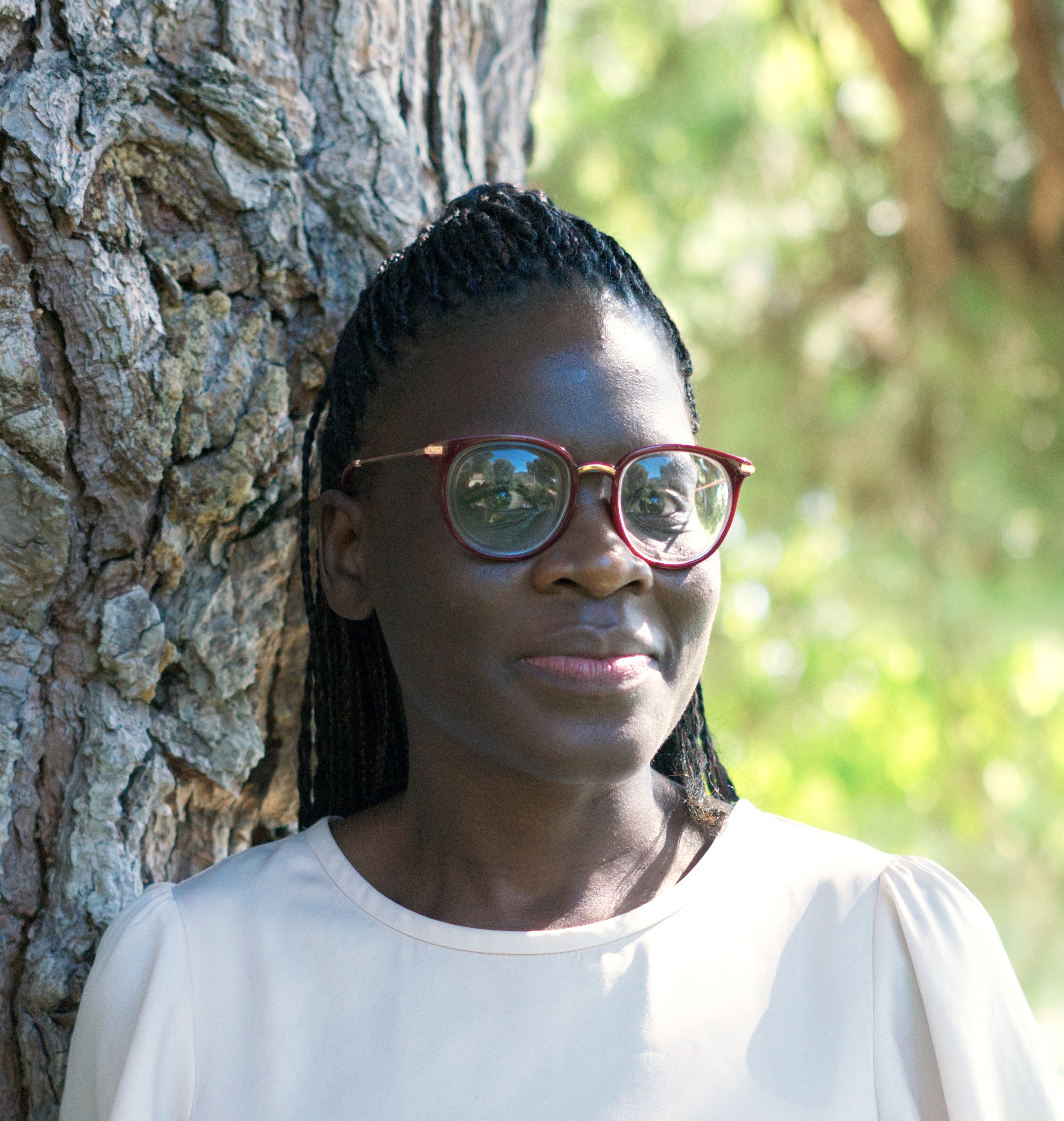
Davidzo Muchawaya is the Regional Lead for Africa at the Initiative for Responsible Mining Assurance (IRMA), where she leverages her extensive 15-plus years of experience in responsible sourcing and sustainability to further IRMA's vision. This vision aims to create a world where the mining industry respects the human rights and aspirations of affected communities, provides safe, healthy and supportive workplaces, minimizes environmental harm, and leaves positive legacies. Davidzo's responsibilities include leading the development and implementation of strategies for regional outreach to extend and deepen engagement with a broad spectrum of stakeholders, such as civil society organizations, labour unions, and communities impacted by mining activities. Davidzo plays a role in facilitating the dissemination of IRMA's audit reports and implementing awareness initiatives to enhance understanding of the IRMA system among stakeholders.
Davidzo is currently co-leading an ISEAL-funded project that explores how voluntary sustainability standards can drive a responsible transition in the steel and mining sectors. The project aims to understand the social impacts of the industry's shift toward a low-carbon economy and the role of multi-stakeholder systems initiatives in ensuring a socially responsible transition.
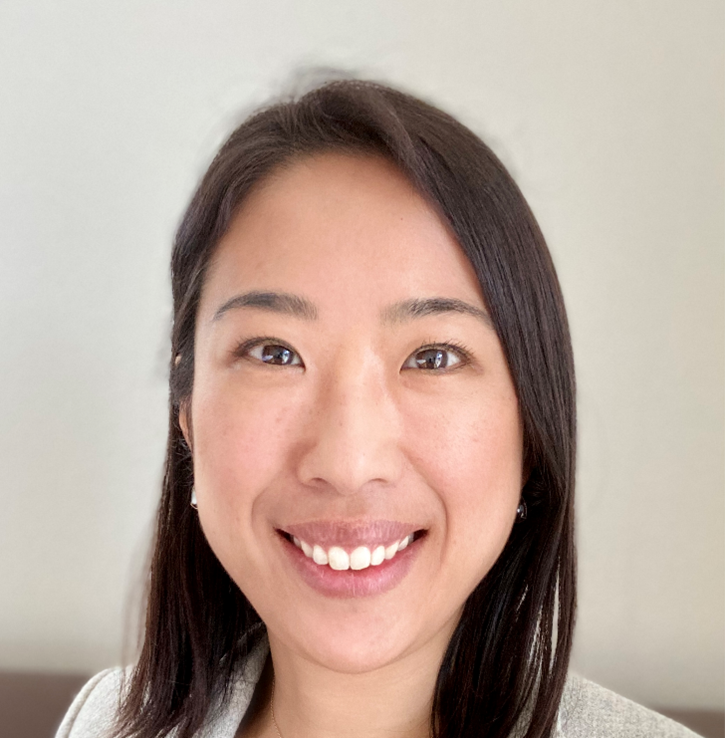
Haruko Horii has 9 years of experience in the sustainability sector, including work with NGOs and a social auditing consultancy firm. In her previous roles with standard-setting organisations, she has worked on various social topics such as living wage, social impact assessment, and gender equality, while ensuring the team’s compliance with standard-setting best practices. Haruko is trained in social auditing (SA8000) and social impact assessment (IAIA). She has worked as a social auditor and consultant, assisting global companies in promoting human rights by developing social responsibility policies and strategies, and establishing assurance mechanisms through capacity-building activities, social audits, and assessments.
Haruko holds a Master’s degree in International Development from Wageningen University in the Netherlands.
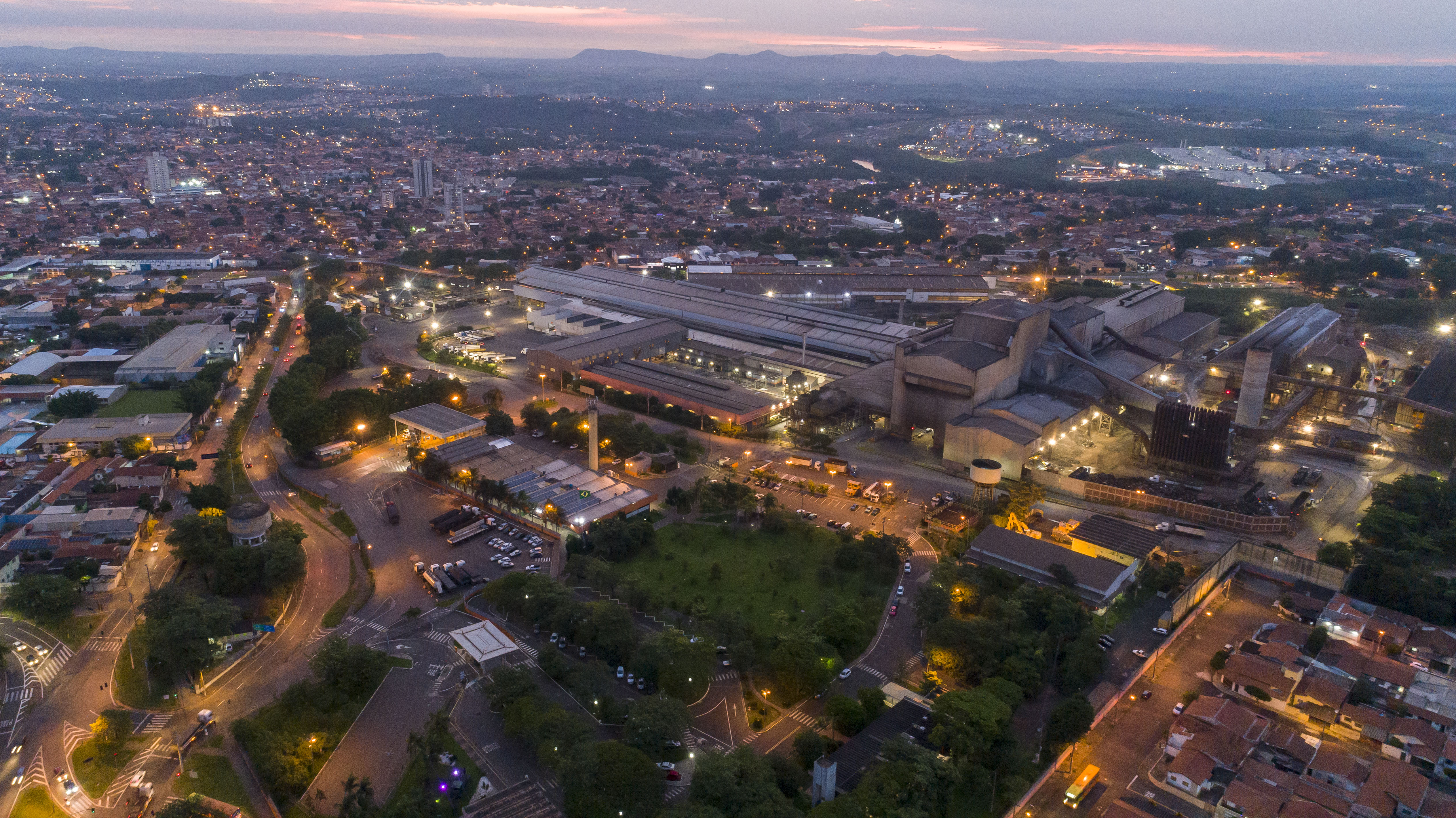
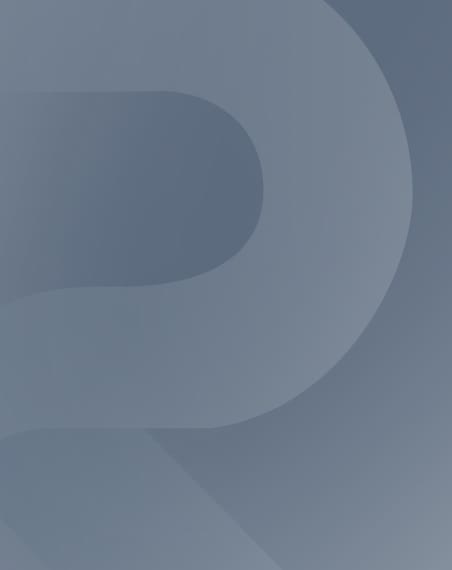
January 2025 Newsletter
After a jam-packed 2024, ResponsibleSteel is heading into another busy year, with key projects already well underway.
In this edition, you'll see a strong focus on advancing our standards, including the upcoming Chain of Custody Standard, the High Alloy and Stainless Steels working group, and the Just Transition project.
We’re also celebrating the certification of six new ArcelorMittal Brazil sites and welcoming four new members. Additionally, we welcome Dale Seymour to our Board and extend our gratitude to Leeora Black for her dedicated service. Exciting opportunities are also available within the Secretariat, with policy and GHG roles currently open for applications.
I'm looking forward to sharing the results of the 2024 membership survey in the coming weeks—thank you to everyone who contributed. We also plan to announce a full programme of in-person and online engagement opportunities for members throughout the year very soon.
In this newsletter you will find updates on:
• Leadership transitions on the Board
• New audits and certifications
• Upcoming standards development projects
• Current vacancies
• And more...
Click here to read this month's newsletter.
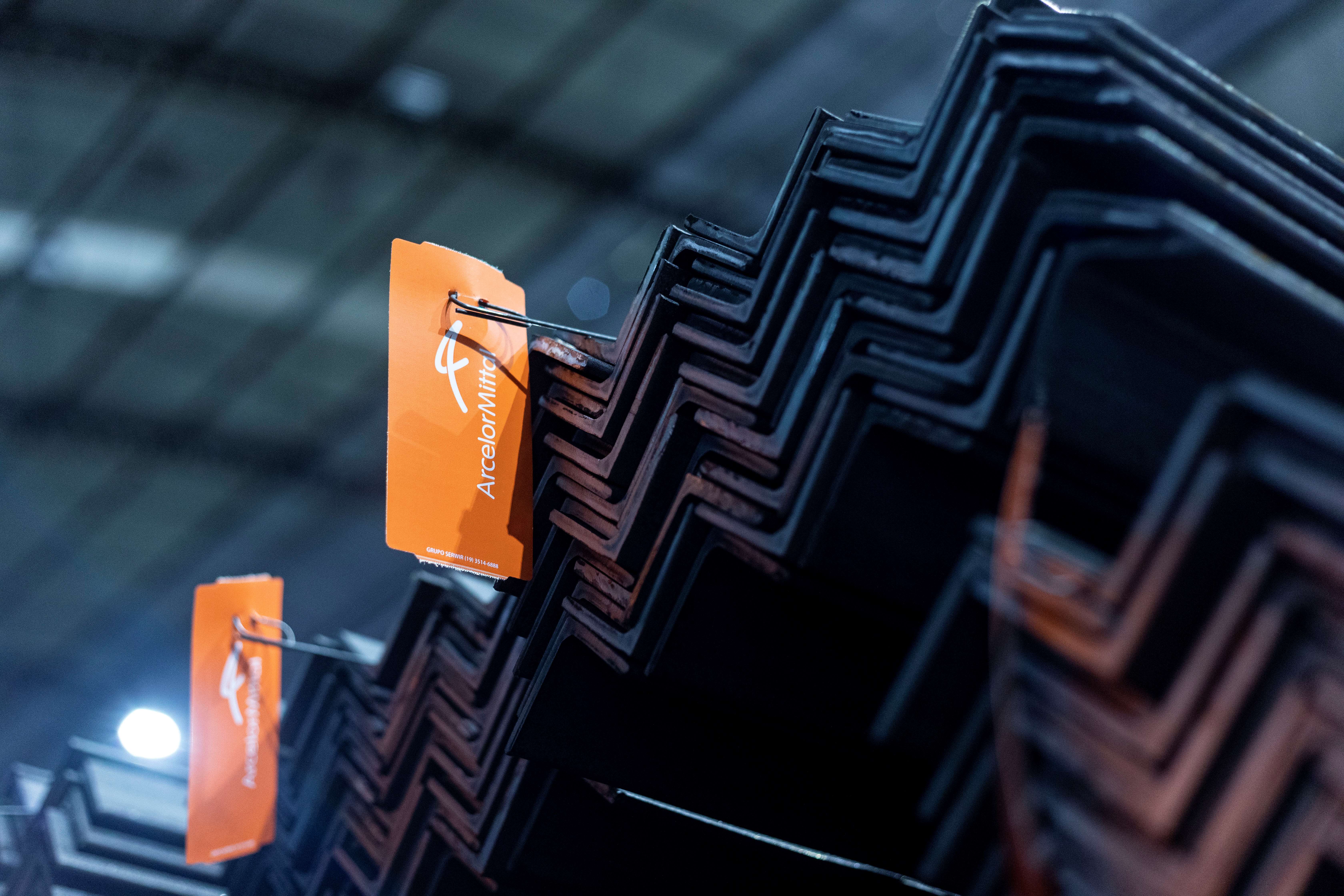
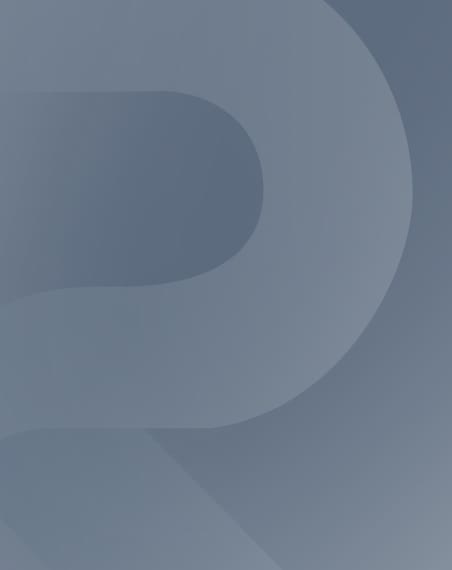
ArcelorMittal Brazil achieves certifications covering six new sites
ArcelorMittal Brazil has achieved ResponsibleSteel Core Site Certification covering six sites: Juiz de Fora, Resende, Barra Mansa, Piracicaba, Sabará, and São Paulo. This achievement follows three previous certifications in 2022 and 2023 for the company's Tubarão, Monlevade, and Vega sites.
ArcelorMittal Brazil is the largest steelmaker in the country, producing long and flat carbon steel products for the automotive, household appliances, packaging, construction, and shipbuilding industries. These six newly certified sites collectively have a production capacity of around 5 million tonnes of steel annually and employ over 5,800 workers and subcontractors.
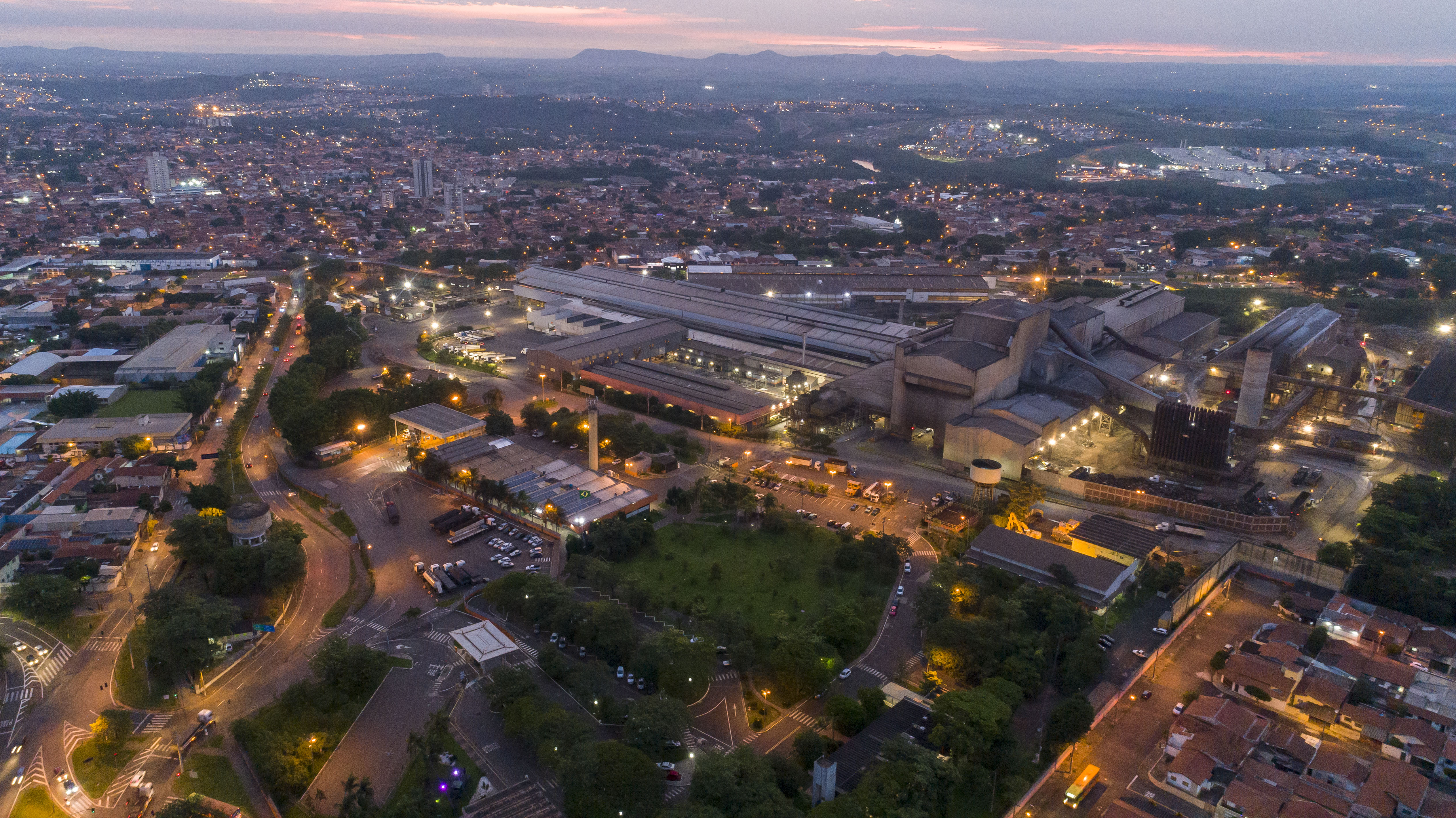
ArcelorMittal Brazil's President and CEO of ArcelorMittal Long Products and Mining LATAM, Jefferson de Paula stated, “We expect to have 100% of ArcelorMittal’s steel production operations in Brazil certified to site level by next year, meeting the highest standards and sustainability criteria. Thus, we will ensure 40% of sustainable steel production in Brazil.”
ArcelorMittal was the first company in Brazil and the Americas more broadly, to achieve Core Site Certification against the ResponsibleSteel International Production Standard. To achieve Core Site Certification, the sites were evaluated against the Production Standard's 13 environmental, social and governance principles, covering everything from the sites' operating infrastructure and production processes to the way the sites manage their employees and relate with the community.
Annie Heaton, ResponsibleSteel's CEO, commented, “This announcement is significant, given Brazil's strategic position in both steelmaking and iron ore production, and these certifications mean that around a third of the industry's capacity in country is now ResponsibleSteel-certified. As Brazil prepares to host COP30 later this year, it is important to see the steel industry put its sustainability commitments into action, not only to decarbonise but to do so whilst taking responsibility for people and nature. ArcelorMittal Brazil’s ongoing accountability to the world's most rigorous, broad-based sustainability standard demonstrates real leadership in driving the industry's journey to more sustainable practices.”
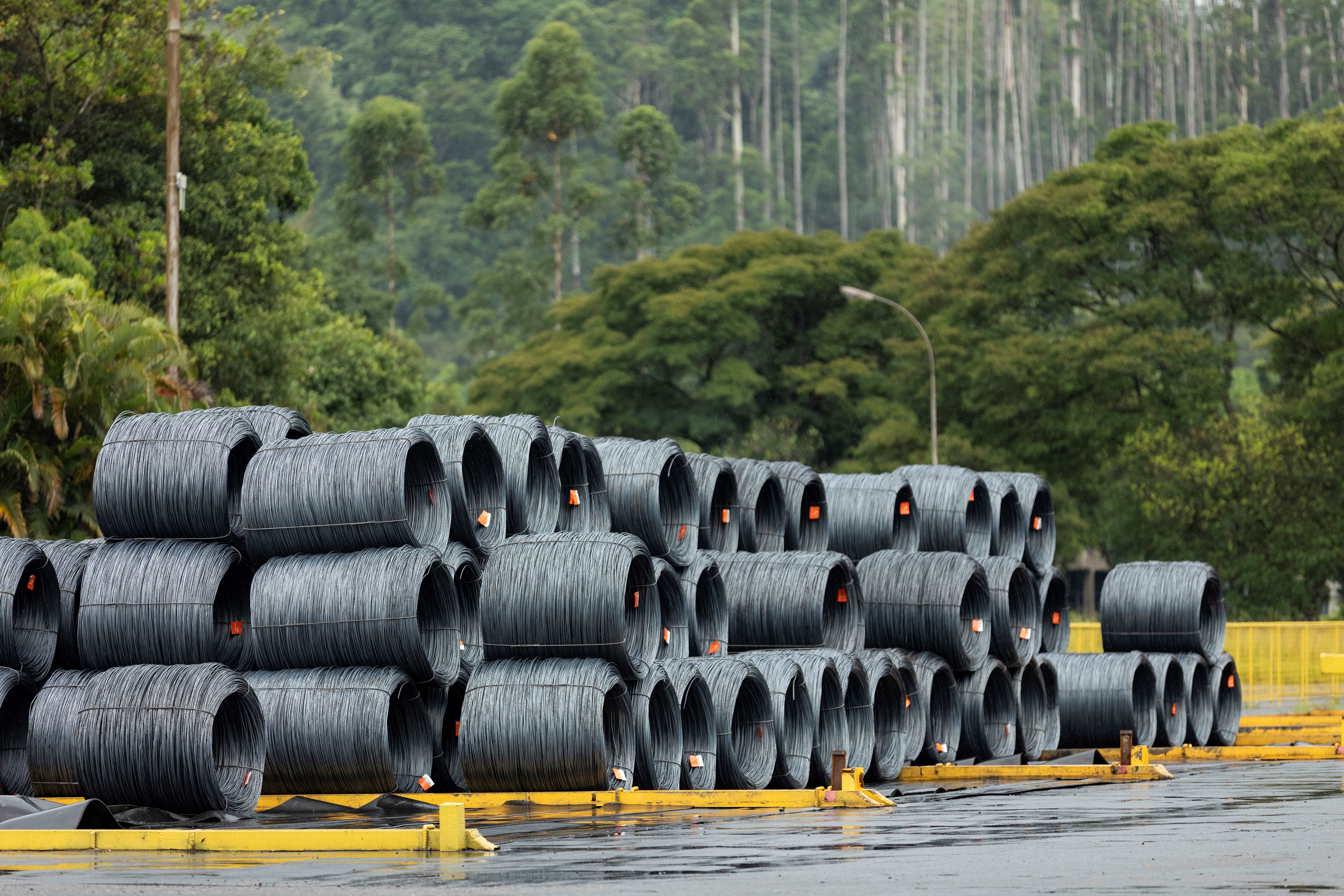
The certification body in charge of the audits, DNV Brazil, assessed the sites against a range of criteria relating to responsible business conduct, occupational health and safety, stakeholder engagement, control of socio-environmental impacts, water resource management, greenhouse gas emissions, and biodiversity protection, among others. This included reviewing the Biodiversity Master Plan, the Basin Predictability Study, the promotion of projects supported by the ArcelorMittal Foundation, and structural improvements in the common areas of the sites to improve worker safety. The audit process also included visits to each of the sites and interviews with workers and local stakeholders.
Learn more about ResponsibleSteel certification here or view the certificates and public audit summaries for sites currently covered by certification here.
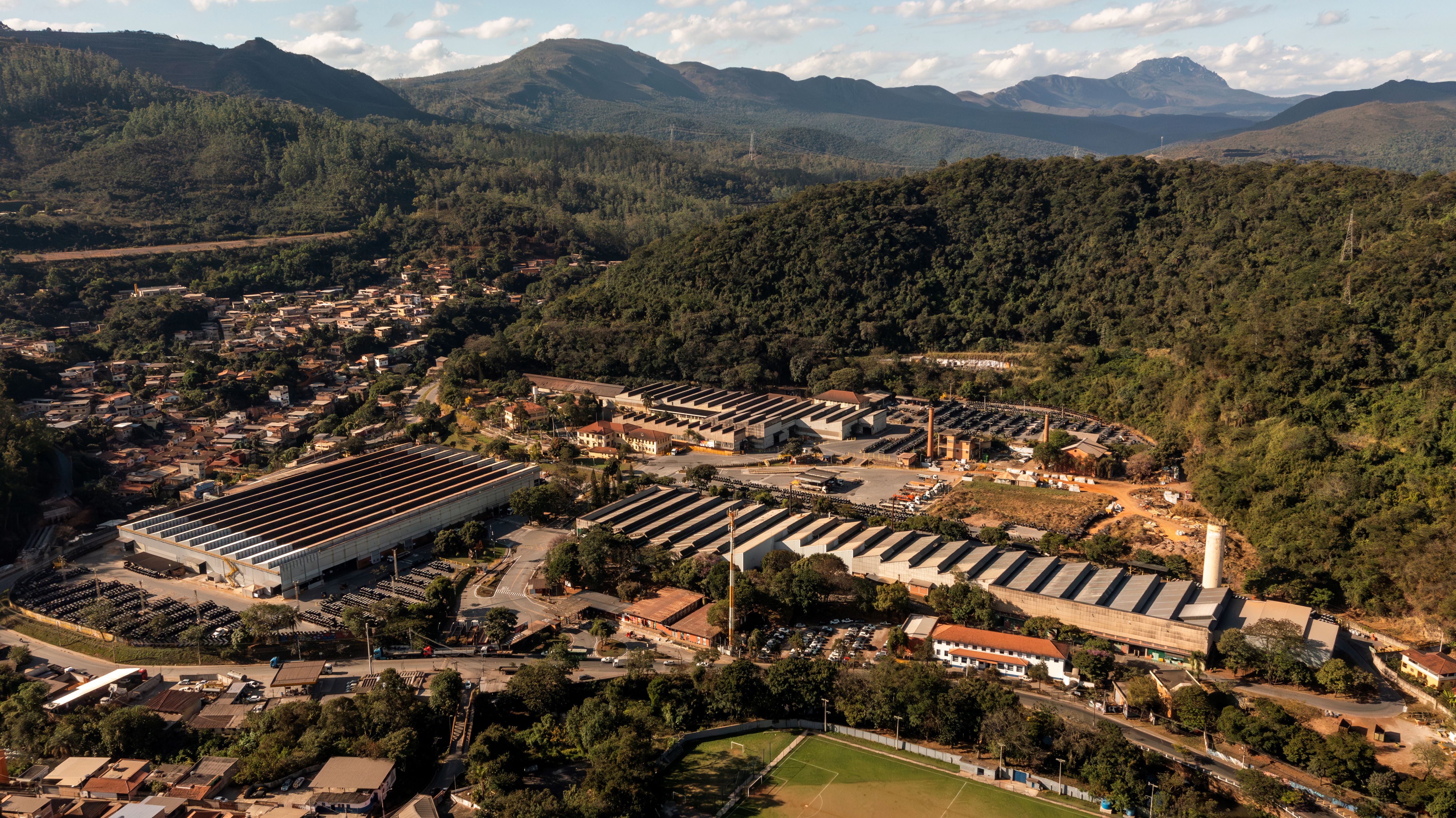
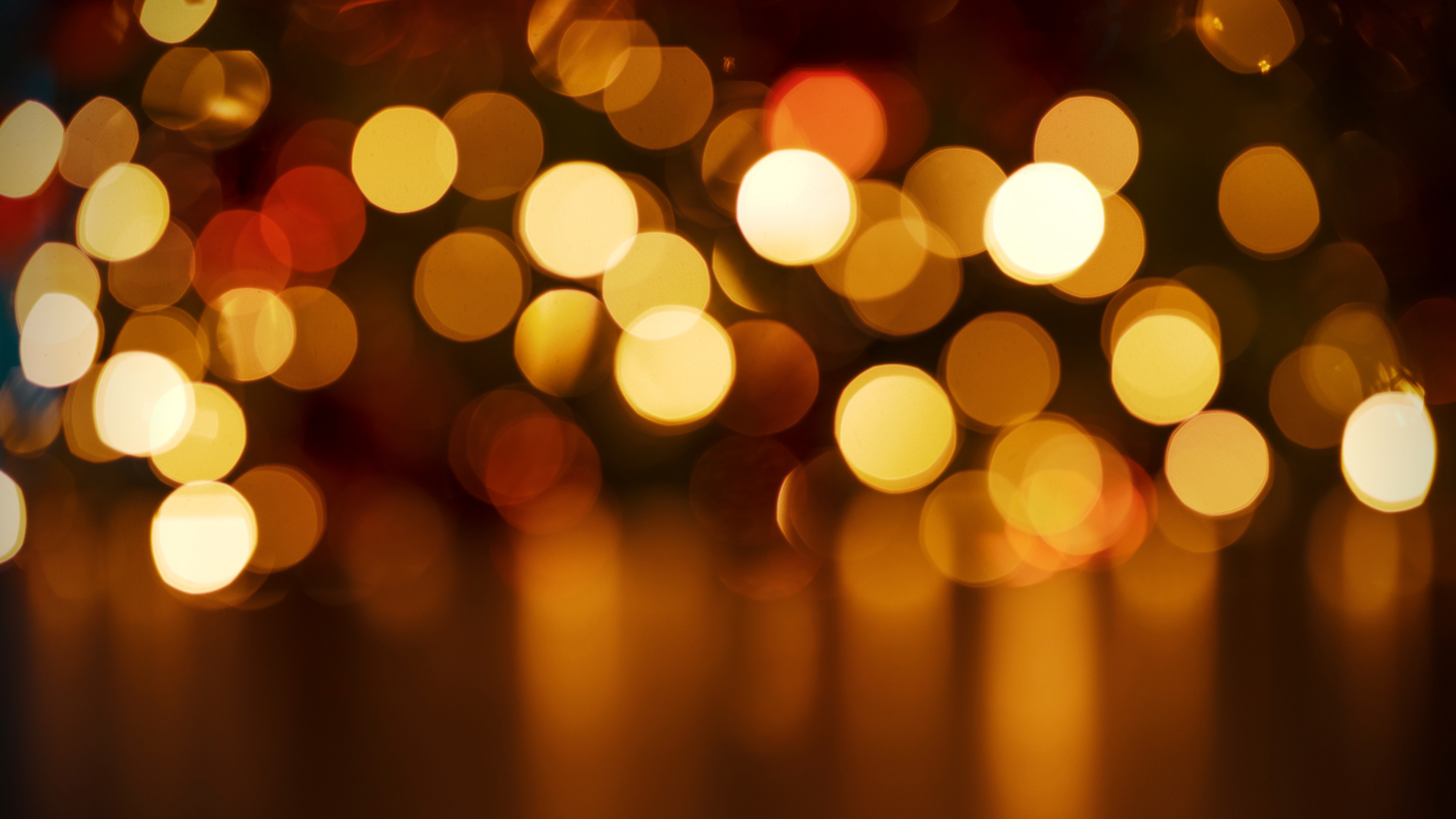
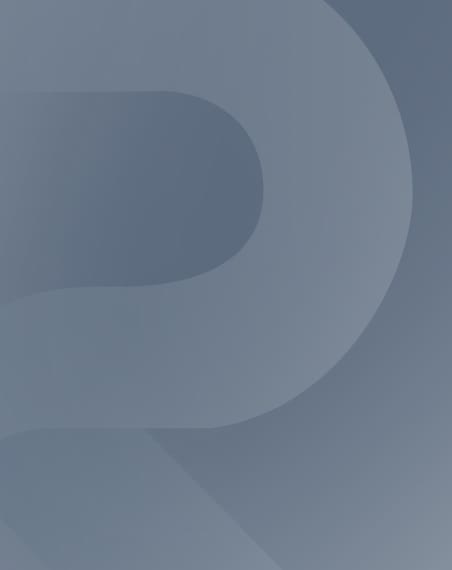
A Year of Transformation: Reflections From Our CEO
In a year defined by developments that pose serious threats to global stability, both geopolitically and for our climate, many are wondering what we have achieved towards a sustainable future in 2024.
It is tempting to despair as progress on decarbonisation appears stalled, economic conditions render projects less feasible and our political leaders appear distracted. And yet I see many signs that we are building unstoppable momentum towards a transformed industry that can withstand these challenges.
There are change-makers amongst us that are showing resolve, energy and creativity to build the road to a sustainable future. These are the collaborators, the innovators, and the systems thinkers providing the impetus for the long-term transition.
Many, I am proud to say, are members and partners of ResponsibleSteel, who see the powerful potential of our global standards and certification system to help drive us toward a more responsible, fair, and just future. They have sought to work with us, to demonstrate their commitment through certification, and to collaborate to build coherent new systems fit for a better world.
Celebrating certification achievements
Let’s start with our members’ certification achievements. Six months after we published our first-ever Progress Report to track the impact our collective endeavour has delivered, we now have:
- Over 160 members headquartered across 36 countries,
- Over 85 sites with Core Site Certification, covering 7% of steel produced annually, both via blast furnaces (42) and electric arc furnaces (17),
- More than 236,000 workers covered by our independent audits that include extensive stakeholder interviews.
- The first site certifications in Vietnam, Canada, Slovenia, Italy, Finland and Sweden as well as new certifications in Germany, France and India.
A significant milestone
Most significantly, at Climate Week NYC we announced the world’s first ResponsibleSteel Certified Steel, achieved by U. S. Steel’s Big River Steel site in Arkansas, sending a clear message to the market: progress towards responsible ‘green steel’ is being made, and stakeholders now have a transparent, consistent and credible global system to benchmark it by.
More Certified Steel will follow, and customers that procure it will enjoy a credibility that stands out from the confusing myriad of ‘green steel’ claims. To fortify this, we consulted on our draft Chain of Custody Standard earlier this year that will forge a path to certified physical traceability and allow buyers of Certified Steel to make credible claims for the first time.
Tracking progress towards global climate goals
Tracking the progress of the global steel industry in a consistent way is vital, and our report 'Charting progress to 1.5°C through certification' demonstrated the power of the ResponsibleSteel system to benchmark this progress.
Over 25 respected experts agreed to peer review the report, which concluded that by 2030, 15% of the world’s steel needs to demonstrate real decarbonisation progress (achieving ResponsibleSteel Progress Levels 2 or 3) and 8% needs to reach near zero emissions (Progress Level 4).
More than that, every steelmaking site in the world needs to perform better than the current global average emissions intensity. In other words, today’s average steelmaker will become the industry’s worst by 2030 if they don’t start improving their operations.
Regulators, customers and investors have an important role to play here in setting the expectations of the industry and incentivising the transition. We encourage them all to reference our global benchmarks in charting their path to 1.5°C.
And yet the risk is that more frameworks for steel emerge which do not deliver comparable assessments of progress. It’s critical that we work collaboratively to create an international system of standards that are interoperable, ensuring coherence, credibility and positive impact across the board.
Building interoperability
I have been delighted this year to develop collaborations with a number of initiatives that seek to reflect ResponsibleSteel’s system of embodied GHG measurement and Decarbonisation Progress Levels within their own frameworks, either through alignment, recognition or conversion.
These are all aspects of the interoperability we need to ensure that global trade in low-emissions steel can flourish. ResponsibleSteel has been a leading voice on how to progress this with the 60+ signatories of the Steel Standards Principles and in conversation with the IEA and the Climate Club. I look forward to sharing more news with you in 2025 on how and where we are putting this into practice.
Alongside this, we are also working at the national level. In the US, ResponsibleSteel’s Progress Level 4 was identified as a benchmark for measuring and defining near-zero steel in the Modern Steel Act. In Germany, we recently welcomed the German Steel Association (WV Stahl) into membership and we continue to build relationships with associations and policymakers in India and China. As regulators at national level develop policy and definitions to incentivise decarbonisation, ResponsibleSteel can support both steelmakers and policymakers to convert their national assessments into a globally coherent and credible system. This year, interoperability became a favourite topic. Next year, we need to turn it into reality.
Looking ahead to 2025 with optimism
All this is evidence of the international ecosystem we are building to effectively support the production and trade of low-emission and near-zero steel. That’s why, amidst the growing scepticism and disappointment permeating climate discussions, I have nothing but hope for the year ahead.
I am fuelled by the enthusiasm of our members and stakeholders and their commitment to working across industry, policy, and finance to drive production of and demand for near-zero steel. I want to thank you for your continued thoughtfulness and support.
While 2024 has brought stark reminders of the climate crisis, it has also demonstrated the power of intelligent collaboration. Now is the time to identify common ground and collaborate to turn our commitments and plans into tangible outcomes. Real-world order books, financial arrangements, and large-scale technology implementation. On behalf of the ResponsibleSteel team, I want to wish you and your families much health and happiness, and a peaceful end to the year. We look forward to working with each of you as we take the next steps toward achieving our shared goals in 2025.
Best wishes,
Annie Heaton
CEO, ResponsibleSteel
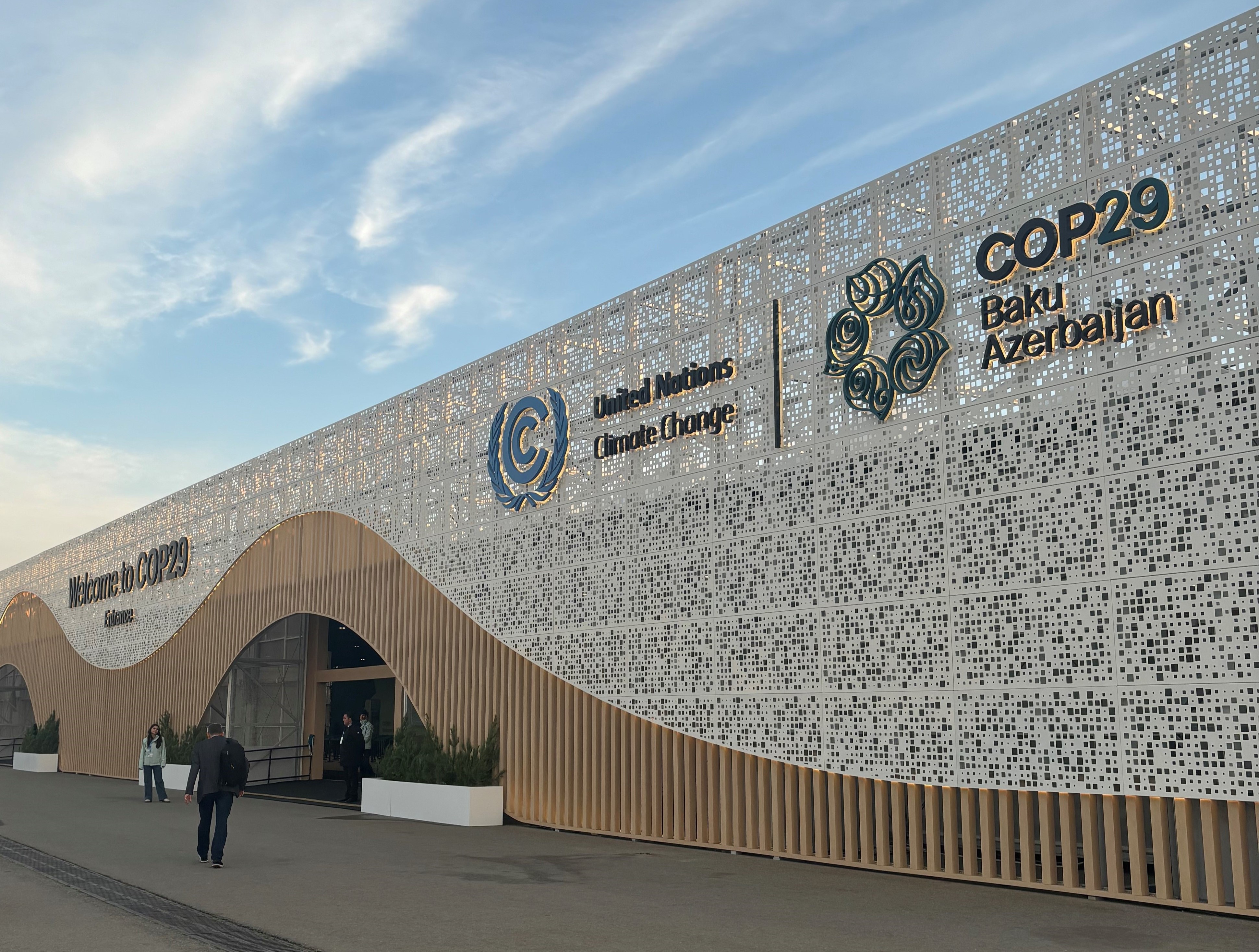
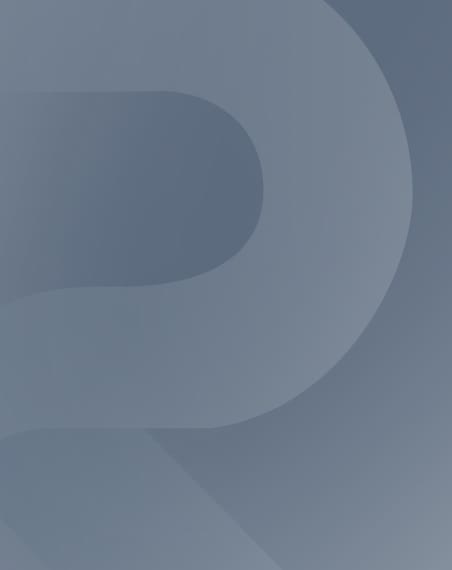
November 2024 Newsletter
As we near the end of the year, we are working on a number of key projects for the organisation. Firstly, the consultation on the Production Standard has been extended to December 8th - this extension provides more time for stakeholders to provide valuable feedback.
Secondly, all members will have received the membership survey via email, offering members a fantastic opportunity to help shape the future of ResponsibleSteel. We strongly encourage all members to fill it out - it really does help us to understand what we are doing right, and what can be added or improved.
Finally, we were on the ground at COP29. Read our blog as we analyse the progress made, the challenges that remain, and the critical steps needed as we look ahead to COP30 and beyond.
In this month's newsletter, you will find key updates including:
- Membership survey
- Insights from COP29
- Production Standard consultation
- New audits and certifications
- New 2025 membership fees
- And more...
Click here to view ResponsibleSteel's November 2024 newsletter.
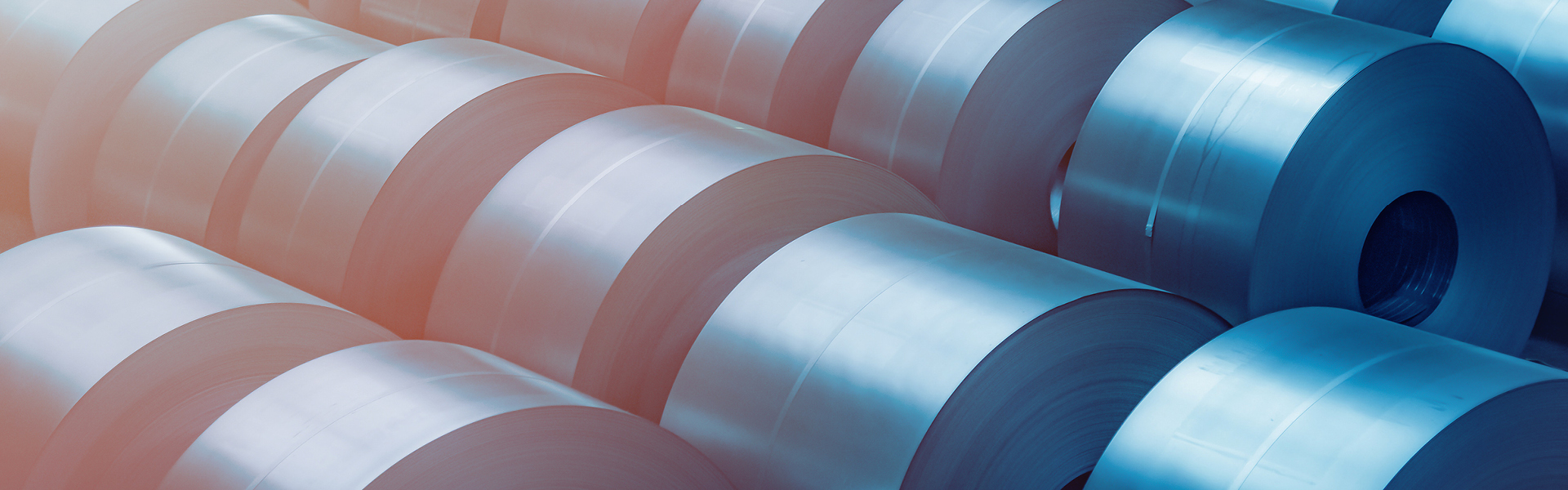
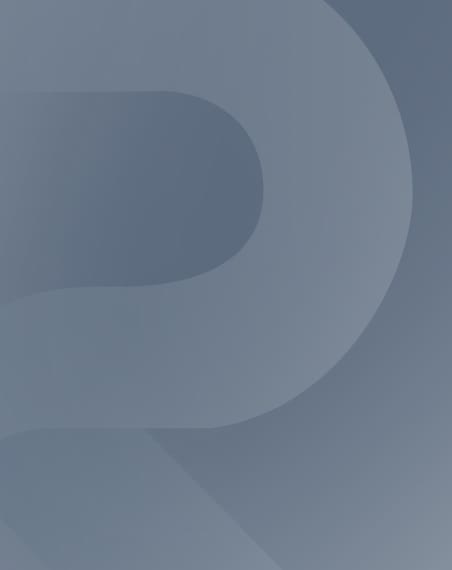
ArcelorMittal Construction achieves Core Site Certification
We are delighted to announce that ArcelorMittal's coil coating plant in Contrisson has been awarded ResponsibleSteel Core Site Certification, underscoring the site's holistic commitment to sustainability and the company's continued progress towards certifying all of its European operations.
ResponsibleSteel certification rigorously assesses the responsibility of steel production. Core Site Certification encompasses over 300 stringent requirements, meticulously verified through an international audit process conducted by trained third-party auditors. The certification adopts a holistic approach, covering key areas such as effective management of water and waste, ensuring health and safety at work, and protecting biodiversity.
The certification also requires a commitment to reducing emissions according to a Paris-aligned pathway, which reinforces ArcelorMittal Construction's C5 Green Commitment, a 5-stage plan that sets out the steps the company is taking to implement sustainable practices and be carbon neutral by 2050.
Jana Meisser, Head of ESG at ArcelorMittal Construction commented: “We’re delighted that ArcelorMittal Construction Contrisson plant located in France has achieved site certification against the ResponsibleSteel International Production Standard. This success underlines our continued dedication to show leadership in responsible production techniques and high ethical standards.”
The site was acquired by Arcelor in 2002 but has a history in steel and iron stretching back hundreds of years. Today the site produces around 300,000 tonnes annually, specialising in the manufacture of continuously rolled, galvanized and pre-painted sheets.
The audit demonstrated the positive relationships the site has built with local stakeholders, strong safety and environment management systems, a well-structured roadmap for the reduction of GHG emissions, and plans to improve the water management policy to name a few.
View the certificate and read the public summary here.
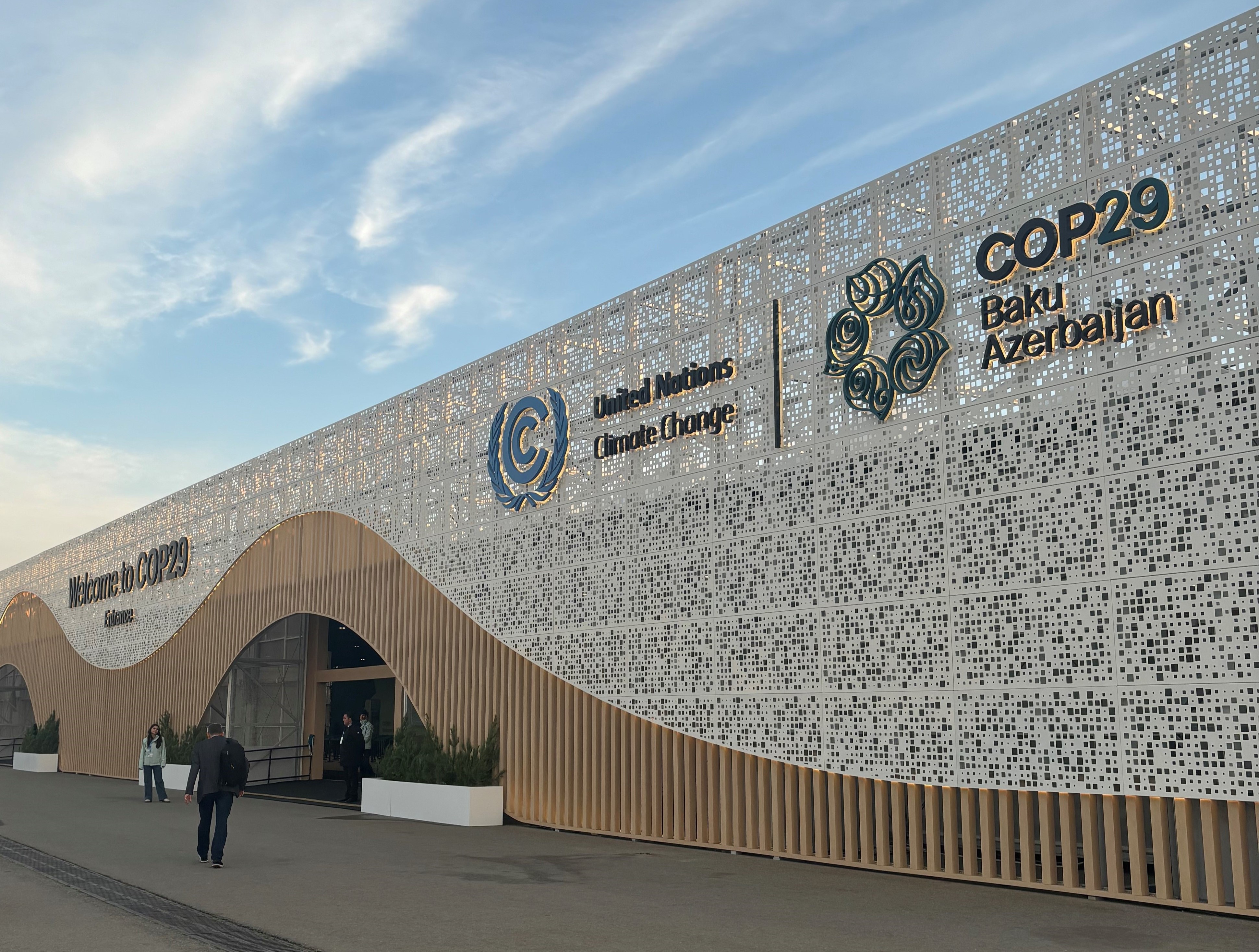
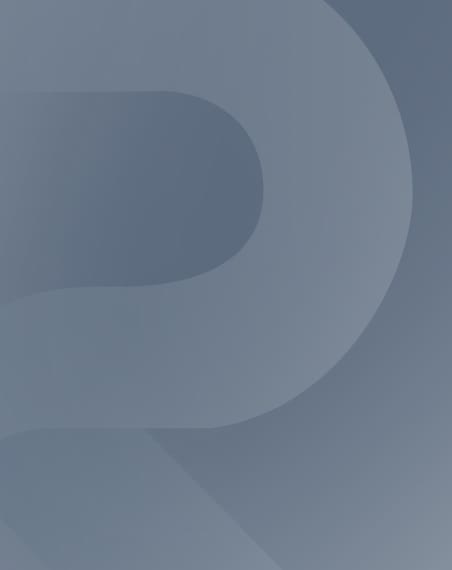
COP29: What has been achieved?
It’s no secret that this year’s COP, dubbed ‘the finance COP’, is leaving many walking away disappointed. COP29 has been plagued by accusations around regression on the agreement to phase out fossil fuels and tensions over closing the financial gap needed for developing countries. The final agreement to supply developing countries with “at least $300 billion” a year is a far cry from the $1.3 trillion goal needed.
So what progress has been achieved? And as we look to COP30, what steps need to be taken to accelerate progress?
The finance question at COP now goes far beyond the requirements under the UNFCCC mechanism for Developed Country Parties to provide and mobilise climate finance for developing countries. Private sources of finance may often be leveraged through government commitments. Whether these can compensate for the slow momentum from developed countries remains a source of great anxiety for developing countries.
More than 500 projects aimed at producing near-zero materials and fuels according to Mission Possible Partnership’s Tracker are awaiting deals for finance across both developed and developing countries. 52 of the announced projects are steel, and only 6 of these have reached a final investment decision.
In Baku, whilst progress on committed finance was disappointing, it felt that collaboration among non-state actor initiatives is beginning to drive a focus on the conditions that will make FIDs in near-zero industry projects possible - carbon pricing mechanisms, the creation of markets and trade in lower emissions steel, and alignment across the standards and carbon accounting mechanisms needed to underpin these.
Financing and technical support for developing countries
The need for technical and financial support for developing economies in this regard is clear. This is after all where the lion’s share of materials demand growth is likely to come, and where the infrastructure for the transition may be most lacking. Here, some headway is already being made.
Earlier this year at the Clean Energy Ministerial in Brazil, the Climate Investment Funds launched a call for expressions of interest for its Industry Decarbonisation investment programme which aims to support low-emission pathways in developing countries for industries such as steel, cement, glass, aluminium and textiles. Up to $1 billion in funding is anticipated to support these projects.
At COP29, one of the biggest wins for heavy industry was the launch of the Climate Club’s Global Matchmaking Platform. First announced last year in Dubai, the Platform is designed to support the heavy industry transition toward net zero. By leveraging international cooperation, the platform aims to match industry players in developing and emerging economies with financers, technology and expertise to create tailored decarbonisation solutions.
Creating market mechanisms
To pave the way for such projects to be viable to mainstream finance, sustainable market policies that provide certainty for long-term investments are urgently needed. In Baku, the momentum on this took a step forward with a letter to governments led by the Industrial Transition Accelerator (ITA) calling on them to create demand for lower emissions materials. The letter was co-signed by over 50 companies and coalitions, including ResponsibleSteel, and a network of more than 700 financial institutions. Importantly, it brought together both private and public sector initiatives, including SteelZero, the First Movers Coalition and the Industrial Deep Decarbonisation Initiative (IDDI).
Some practical tools for policymakers launched in Baku were a welcome addition to the landscape – a Green Demand Policy Playbook from the ITA and with WBCSD, a Green Purchase Toolkit. These provide the start of an innovative school of public policy that is urgently needed to ensure that lower-emissions materials are soon more competitive than their high-emitting relatives.
Driving green public procurement
On the procurement side, pressure is ramping up on governments to make public procurement commitments for lower-emission materials. The IDDI, the First Mover’s Coalition, and the Net Zero Government Initiative all came together to launch a joint statement in Baku calling on governments to increase demand signals through procurement.
The United Nations Industrial Development Organisation (UNIDO) and the IDDI also presented their latest report, "The Scale and Impact of Green Public Procurement of Steel and Cement in Canada, Germany, the UK, and the US." According to the research, implementing policies in line with the IDDI’s Green Public Procurement Pledge Level 3 in these four countries alone could reduce emissions from steel procurement by 81% by 2050. It’s a powerful indication of how governments can leverage their purchasing power to drive industry decarbonisation and help create a market for lower-emission steel.
Underpinning this, IDDI launched its Green Public Procurement Guide series on assessing jurisdictional readiness for procuring low-emission materials, disclosure requirements to support market readiness, and setting commitments, highlighting ResponsibleSteel as a useful framework to meet Pledge Level 3. The Guide offers practical guidance to help governments take actionable steps to incorporate commitments to purchase low-carbon steel and concrete for construction projects into public procurement practices.
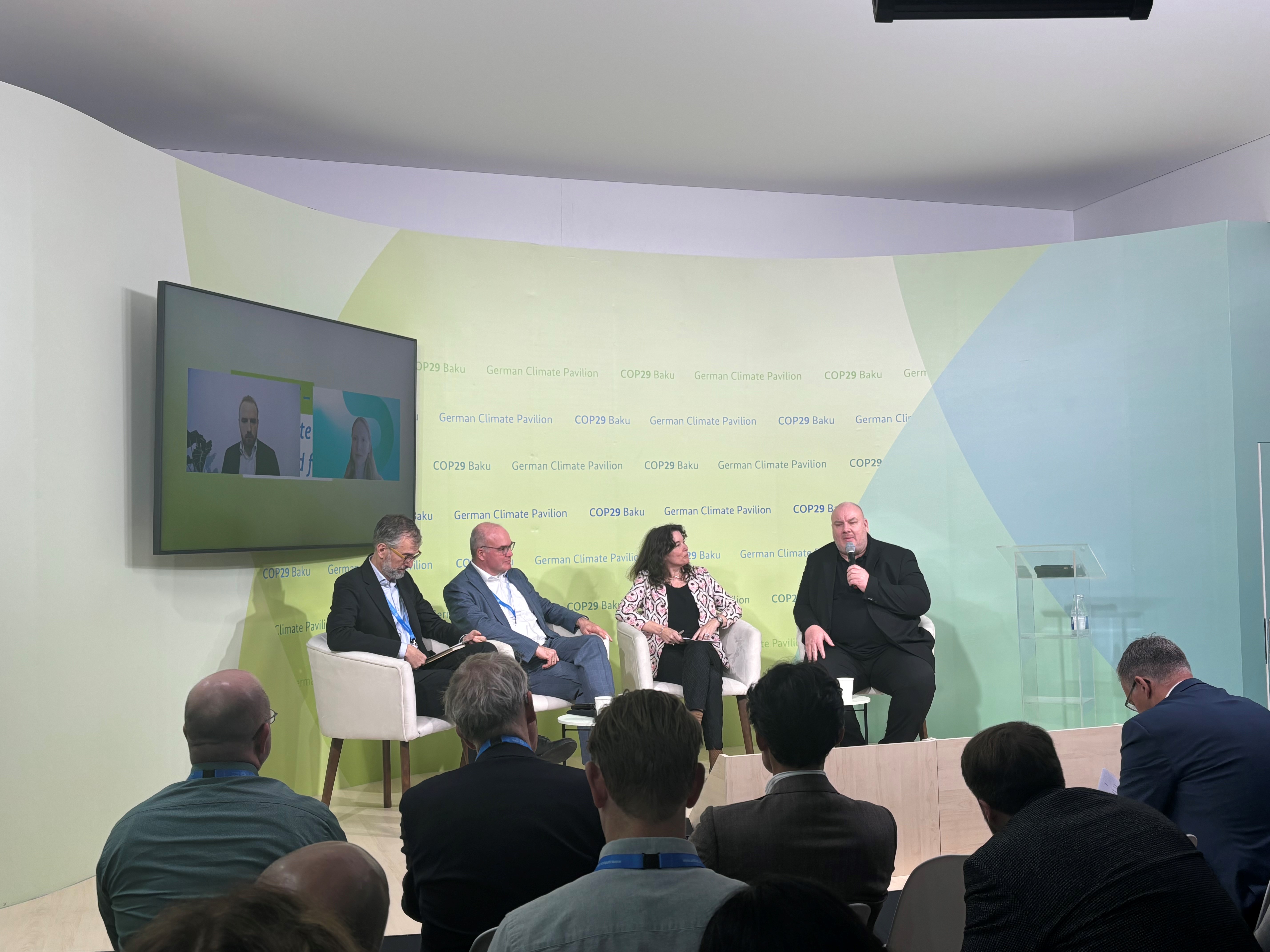
Harmonising standards
Finally, as more standards for steel continue to emerge, everyone can agree on the need for harmonisation, or at the very least interoperability, across these different standards to reduce trade friction and facilitate investment. Anything less will only serve as a roadblock to achieving net zero, a sentiment that was frequently shared during discussions in Baku.
The Steel Standards Principles launched in Dubai at COP28 are playing a critical role in driving alignment across definitions for near-zero steel and ensuring interoperability across GHG measurement methodologies. ResponsibleSteel has played an active role over the last 12 months to help establish the foundations for harmonisation and interoperability. Over 60 organisations have now endorsed the Principles and released a statement at COP29 setting the following objectives for 2025:
• Establishing a common boundary for emissions reporting across the steel value chain
• Enhancing data quality and transparency
• Developing common terminology across standards and initiatives
• Increasing stakeholder engagement globally
As part of this work, the World Steel Association has produced a methodology mapping examining similarities and differences in more than 40 criteria across around 80 standards and initiatives, including ResponsibleSteel. This mapping will be a valuable resource for identifying opportunities for harmonisation and improving transparency in the industry, something ResponsibleSteel is committed to doing.
Looking ahead
2025 will mark the 10th Anniversary of the Paris Agreement and COP30 is already shaping up to be the most critical COP since 2015. Accelerating progress on critical issues such as protecting biodiversity and ensuring a just transition will likely have a key role in discussions and there is already pressure on governments to move up their net zero targets.
It’s clear we’re still a long way from where we need to be, within the steel industry and beyond. ResponsibleSteel’s Charting Progress to 1.5°C report concludes that some 8% of the steel industry needs to be produced by near-zero transition projects by 2030 (i.e. reaching our Decarbonisation Progress Level 4). MPP’s Tracker suggests only 6 projects are currently financed. We need to close this gap. We must also avoid relying on these select near-zero projects alone. At least 15% of steel needs to be produced by lower emissions steel plants by 2030 (our Progress Levels 2 and 3) and 100% needs to be where the average of the industry is today (Progress Level 1).
As governments finalise their NDCs for COP30, they need to consider how to send a serious signal to the market that by 2050 only near-zero steel will be acceptable, and devise the mechanisms and the milestones to drive progress towards that goal.
By Savannah Hayes, Communications Manager, ResponsibleSteel