The ‘Sliding Scale’: Setting Equitable Thresholds to Drive Global Steel Decarbonisation
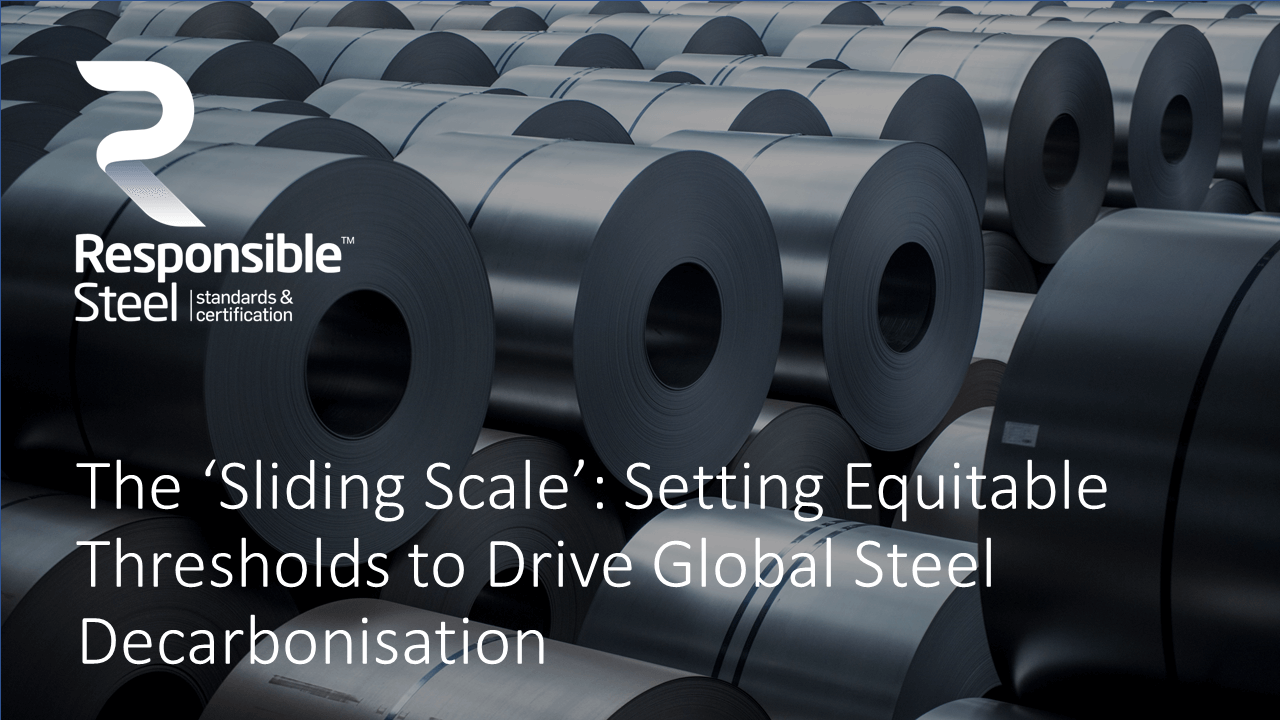
This September the ResponsibleSteel International Standard Version 2.0 was launched following almost three years of development by ResponsibleSteel and its multi-stakeholder membership. It included exacting new criteria on both the responsible sourcing of input materials and on climate change and greenhouse gas (GHG) emissions. Recent years have seen numerous approaches suggested for how best to define the GHG emissions of steel production. This briefing paper situates the use of a ‘sliding scale’ to evaluate a steel production site’s progress on GHG emissions as a key measure to decarbonize the global steel industry. The ‘sliding scale’ is one component of the ResponsibleSteel International Standard.
Steel is one of the world’s most widely used materials. From buildings to bridges, from cargo ships to cutlery, electric vehicles to wind turbines – steel is at the foundation of contemporary societies and in the infrastructure needed to transition to more sustainable ones. Steel has pertinent impacts on both people and planet across environmental, social, and governance issues.
One such issue that is increasingly in the global spotlight is the steel sector’s contribution to climate change. Steel production is estimated to directly emit between 7% and 9% of global anthropogenic carbon dioxide emissions. Diverse actors and stakeholders are taking action to catalyze change and reduce the GHG emissions of the steel sector – civil society, governments, multilateral bodies, steelmakers, steel buyers, financiers, think tanks, academics, and many more.
While the proliferation of actors engaging in this issue is welcome and essential to achieving optimal outcomes, the challenge of steel decarbonisation is best served by the non-proliferation of standards. Common, consistent, and globally comparable definitions are needed.
Decarbonising steel and the ‘sliding scale’
Reducing the steel sector’s global greenhouse gas emissions to net zero will need the world to use less steel, use steel more efficiently, switch to alternative less emissions-intensive materials where possible, maximise the reuse and recycling of steel and, critically, decarbonize steel production itself.
Steel is made with iron-bearing input material through the reduction of iron ore and the recycling of scrap metal. Steelmaking sites use differing shares of these two input materials and consequently different sources of energy input. Iron ore based production – which makes up around 70% of today’s steelmaking – is far more emissions intensive than scrap based production, since stripping oxygen from iron ore is extremely energy intensive and today relies on fossil fuels. Innovative production methods, including those that use cleaner fuels such as hydrogen, are poised to reduce this emissions intensity, but the scale and cost of the transition has historically been prohibitive. In scrap based production, electricity is used and emissions are lower, meaning emissions can be reduced through the procurement of renewable electricity.
Significant demand side measures will be needed to reduce the consumption and therefore production of steel, but 1.5C scenarios still demonstrate the need for significant decarbonisation of steel production. For instance, the International Energy Agency’s (IEA) Sustainable Development Scenario, which outlines a trajectory compatible with the goals of the Paris Agreement, is based on the assumption that two-fifths of the emissions reductions from steel until 2050 occur from material efficiency.
Estimates suggest that about 85% of globally available scrap steel is recycled today. This number must be increased to as close to 100% as possible and the quality of steel reuse and recycling vastly improved, but it also reflects the fact that there is limited and constrained room for growth of scrap steel, at least in the short term. It is well established that there is simply not enough scrap steel to meet demand today nor is there likely to be in 2050. For example, the IEA’s Sustainable Development Scenario, despite its assumption of significant material efficiency, projects total demand increasing from today to around 2 billion tonnes annually in 2050. In this scenario, scrap makes up 46% of iron bearing material, leaving the remainder to be met through iron ore. Additionally, some grades of steel currently require iron ore based production methods. This is not to say that both quantity and quality of scrap steel recovery, processing and use should not be systematically addressed and ameliorated. Rather, that new iron ore based steel will be needed to meet socio-economic needs and to transition to a low carbon future.
The scarcity of scrap combined with its lower emissions profile and the ability of steel plants to incrementally increase scrap input together mean that emissions intensity alone is an insufficient measure to drive the decarbonisation of the steel industry. Incremental increases in scrap usage can significantly lower the emissions profile of steel production at a given steelmaking site, but it is important to be mindful of only serving to shift around the finite supply of scrap from one producer to another.
For the steel customer aiming to contribute to decarbonizing the industry, how can they help to drive industry wide decarbonization? Of course the first principles of design and material efficiency are central, as is driving and enacting genuine high-quality circularity within their operations and supply chain. Selecting steel products according to their emissions intensity alone would drive demand towards steel with higher scrap shares. This could simply cause the finite volumes of scrap to be reallocated, without decarbonizing the industry as a whole.
Setting variable thresholds for embodied GHG emissions that take account of the share of scrap input resolves this issue, and provides effective benchmarks for steelmakers whatever level of scrap they use, and so drives the structural, physical decarbonisation of the steel industry. The ResponsibleSteel Standard V2.0 defines quantitative performance levels for the GHG emissions intensity of crude steel production. It gives four levels ranging from the basic threshold to the near zero threshold. Approaches taking account of the variable amounts of scrap used in production have been dubbed the ‘sliding scale’.
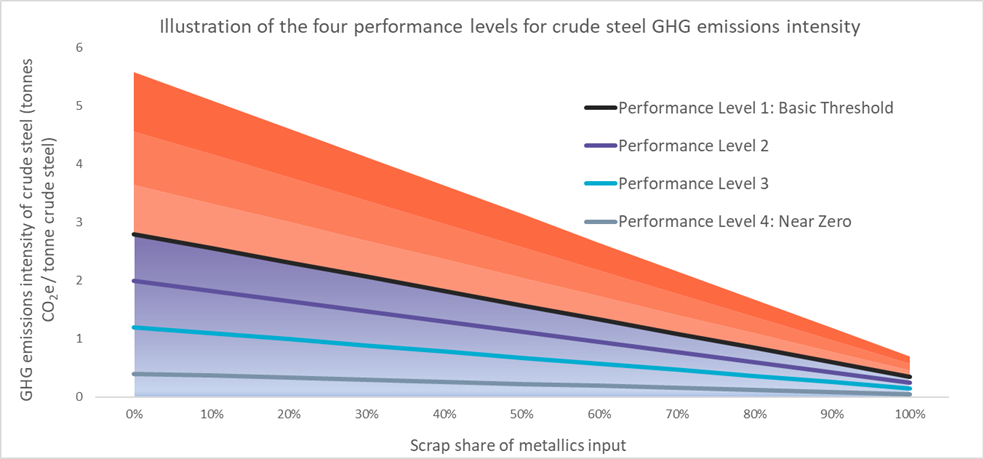
Illustration based on ResponsibleSteel International Standard Version 2.0
Underpinning the ResponsibleSteel scrap-variable GHG thresholds are the accounting rules within its International Standard V2.0 which ensure the consistent and transparent measuring of GHG emissions at the site level. These rules, together with the thresholds, provide a tool for decision makers that reflect a number of principles ResponsibleSteel believes are essential to the establishment of an international standard to drive global steel decarbonization:
Comparable. Specifying the emissions from mine to crude steel production, the standard uses a boundary common to every steelmaker, to ensure comparability of steel production from one producer to another, anywhere in the world and no matter their level of integration. Consistent accounting rules enable ‘apples for apples’ consideration of the GHG emissions embodied in steel.
Stable but adaptable. The ResponsibleSteel International Standard V2.0 also includes a five-yearly review of the specified thresholds, enabling them to be revised with the objective “to achieve the fastest global transition to a near zero steel sector”. This ensures a level of predictability and stability to the thresholds, whilst also leaving flexibility to tighten the requirements and the level of ambition as our understanding of the 1.5°C challenge evolves. The ‘sliding scale’ itself does not prescribe how much steel should meet what level by when. Rather it provides simple graduated measures of progress towards near zero that can be used as an effective tool by customers and governments to achieve their ambitions. Various scenarios provide indications of what is needed, the Mission Possible Partnership’s Carbon Cost scenario for example, identifies the need for 170 million tonnes of annual near zero iron ore based production to be online by 2030 if the industry is to stay on track for a 1.5°C future.
Technology agnostic. The ‘sliding scale’ approach is technology agnostic – it assesses performance by the progress a site makes on GHG emissions. It rewards sites making decarbonization investments across technology measures and means that, regardless of the availability of scrap metal or production technology route, producers can be incentivised to reduce emissions through ever higher levels of recognition.
Equitable. Furthermore, the sliding scale ensures that the standard is globally comparable and non-discriminatory. Steel is produced – and needed – across the world and yet the availability of scrap is geographically uneven. Countries with longer histories of large scale steel production and so greater existing stocks of steel – in cars, buildings, ships – have greater opportunities to recycle steel and therefore produce steel from scrap. In practice, this means that countries that today have growing steel demand – which historically has been closely linked to social and economic development – face the greatest obstacles to meeting demand with steel from scrap. While scrap is an internationally traded commodity, it is increasingly seen as a strategic resource and can be subject to export restrictions.
For further information on the rationale for a ‘sliding scale’ approach, see the article ‘Achieving Net Zero in the Steel Sector’ in Chatham House’s Sustainability Accelerator, and the IEA’s (2022) recent report to the G7.
A vital piece of the puzzle
Sustainable development focused. The ‘sliding scale’ is not a silver bullet. ResponsibleSteel’s strategic mission is to drive the production of net zero steel globally that is both environmentally and socially responsible. The ResponsibleSteel International Standard Version 2.0 requires steelmaking sites to operate responsibly across 13 principles that incorporate the full spectrum of environmental, social, and governance issues relevant to the steel sector. The Standard was developed by ResponsibleSteel and its multi-stakeholder membership aiming to follow ISEAL Codes of Good Practice. Certification against the Standard is backed by a robust assurance programme. To date, steelmaking sites across five continents representing over 100 million tonnes of production capacity and over 157,000 workers have been site certified.
Complementary. An effective ‘sliding scale’ complements rather than replaces other measures and performance requirements on decarbonisation and greenhouse gas emissions. The ResponsibleSteel International Standard V2.0 takes a multifaceted approach to climate change and greenhouse gas emissions. Alongside variable performance thresholds and among other requirements, it mandates both science-based targets at the corporate level (with strategies and plans at the site level) and, at higher levels of certification, it requires product carbon footprints for steel sold from a site. Net zero targets drive and reward forward planning, and science-based targets ensure the early investments required to deliver GHG emissions reductions within 5-10 years. Data on product carbon footprints can be used by customers to measure emissions in their supply chain and reduce emissions on a company, project and product level, while the ‘sliding scale’ ensures those products are contributing to global climate goals. It can also complement minimum scrap thresholds for products and measures to maximise material efficiency, the reuse, and the recycling of steel.
Scrap-variable thresholds have been included in ResponsibleSteel’s climate change and GHG emissions approach to ensure that the Standard is comparable, enabling apples for apples consideration of steel production globally, stable but adaptive, technology agnostic, equitable, sustainable development focused, and complementary to other measures and performance requirements. These principles, among many others, are vital to setting effective and common definitions. The ‘sliding scale’ enables policy makers, steel buyers, and financiers to match ambition with real, physical decarbonisation of the steel industry – globally. It should be used as a key measure of GHG emissions performance for steelmaking.