Carbon Re Talks Creativity and Innovation in the Steel Industry

Creativity and innovation are an integral part of the steel industry. To mark World Creativity and Innovation Day, we asked Buffy Price and Sherif Elsayed-Ali, co-founders and current COO and CEO of ResponsibleSteel member Carbon Re, a few questions about what they think the next steps are for the sector in terms of utilising new technology and artificial intelligence to advance decarbonisation initiatives.
1. Many people might not immediately think of steel when discussing World Creativity and Innovation Day, but these have played a major role in the development of the industry. Why do you think it is so important to apply this same creative approach to decarbonisation?
Steel is probably more intertwined with creativity and innovation than any other material, both with regards to its uses and how different steels are made. The invention of steel itself was one of the biggest industrial innovations in human history, taking iron ore and transforming it into an incredibly versatile and reliable alloy.
The beauty of steel is that it’s at home in everything from building structures to sculptures and spacecraft. The properties of steel allow industrial designers, architects and artists to create an infinite variety of tools, machines, buildings, and art.
Today there are four main types of steel and more than 3,500 grades, each with properties tuned for specific applications. This huge number is only possible because of the talent and continuous innovation in the steel industry.
2. How is Carbon Re currently working to support steel decarbonisation?
Steel is a very hard industry to decarbonize. Carbon Re’s focus is on developing solutions that bring financial and climate benefits to steel producers today—solutions that can be scaled rapidly. We are doing this by leveraging the huge advances in computation and artificial intelligence to help optimize steel production, reducing energy costs and emissions simultaneously.
Steelmaking may seem like a known quantity—in general terms it is, but it is also very complex, with physical and chemical interactions constantly changing as a result of the chemistry of fuels and materials, the state of equipment and the natural variation in the process.
We leverage the huge amount of data produced by industrial sensors and IoT to build a digital twin of the production process that reproduces the specific characteristics of a given plant, rather than being a generalised physics-based model. This digital twin then acts as a virtual training environment for artificial intelligence agents that learn through a method called reinforcement learning, a branch of AI particularly well-suited to complex environments whereby the AI learns by trial and error.
The results are AI agents that support operator decision-making, enabling dynamic adjustments of the production process to produce the desired amount of material, with the required quality at very efficient energy levels.
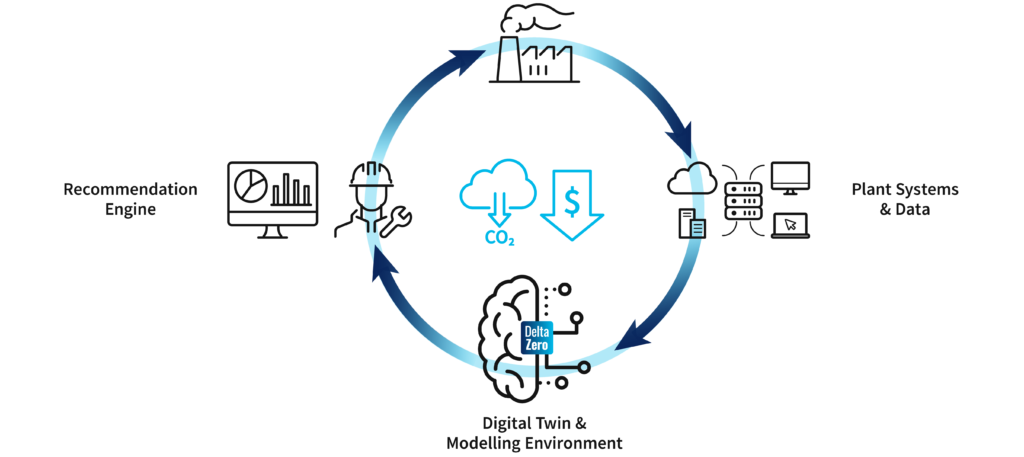
3. We are very proud to have Carbon Re as a member of ResponsibleSteel. What made you want to be part of the growing RS community?
The world is not moving fast enough to tackle climate change and most technological solutions are 10 years off impact and scale. We absolutely must take a multi-pronged collaborative approach to decarbonization and building a community like ResponsibleSteel is a vital part of that process. In fact, ResponsibleSteel has emerged as the leading global initiative to accelerate decarbonization in the steel industry and we are very proud to be part of it.
4. How do you think we can better support decarbonisation in the steel industry?
There are a number of challenges to decarbonization: technical, financial and regulatory. On the technical side, we need to encourage fast innovation and technology demonstration. Financially, we need the right incentives to encourage decarbonization—whether these take the form of carbon pricing or tax credits. Finally, on the regulatory side, we need active policies to support the steel industry to reduce its carbon intensity including, for example, responsive building codes that enable, rather than hinder, innovation in building materials.
5. Why do you think it is so important to have a global steel standard?
We think it is important to create a level playing field across the industry by ensuring consistency and transparency across measurement and reporting mechanisms. This not only substantiates claims and provides benchmarks for progress but also empowers steel buyers to make the right decisions to fulfil their own decarbonization objectives.
6. We are currently revising our ResponsibleSteel Standard to include enhanced GHG emissions and sourcing criteria. What do you foresee as the greatest challenges in tackling emissions in the steel sector?
The biggest challenge is almost certainly the substantial costs associated with most decarbonization solutions and dealing with legacy infrastructure. But there are low-cost solutions that can help tackle carbon emissions in the short to medium term.
7. What steps should steelmakers be taking to decarbonise? What innovations should they be adopting?
First, we have to acknowledge two realities.
The first is that the widespread use of steel is essential to modern societies and that there is no real replacement for it—not just because of its versatility but because iron is one of the most abundant elements in the world. The world produces close to two billion tons of steel every year, second only to cement as the most produced material in the world.
The second reality is that producing steel produces a lot of CO2 emissions, both due to the types of fuel used—such as coal—and the process CO2 emissions in blast furnace steelmaking. Today, these are very hard to decarbonize. There are technological solutions such as CCUS and green hydrogen, but they face many challenges for widespread adoption, including costs, energy requirements and storage/reuse requirements (for CCUS).
These technologies will evolve and become more affordable with time, but we simply can’t wait to start decarbonizing. I think we need to think of decarbonization in the steel industry in terms of three phases:
- Optimizing the use of existing assets
- Improving existing assets, for example by retrofitting CCUS
- Building a new generation of low-carbon assets
At Carbon Re, our focus today is optimizing the use of existing assets by delivering technology that provides near immediate financial and decarbonization benefits to steelmakers and that can be scaled rapidly.
8. How important do you think artificial intelligence is in the fight against climate change?
AI is a foundational technology—it can enable new applications in almost every industry, but it doesn’t work alone. When combined with industry-specific expertise and with other scientific fields such as chemistry and material sciences, it can accelerate the development of new solutions and new discoveries.
As such, AI has a very important role in the fight against climate change—from measuring emissions to modelling climate change to improving industrial processes and designing new low-carbon materials.
At Carbon Re, we are building a world-class multidisciplinary team, not just to bring the latest AI techniques to steelmaking, but to push the state-of-the-art of what’s possible to make the decarbonization of the industry a reality.
Buffy Price is co-founder & COO of Carbon Re. She was formerly AI for Climate Partnerships Manager at Element AI and Senior Advisor at Amnesty International. Buffy has extensive experience in change management, organizational processes and project management.
Sherif Elsayed-Ali is co-founder & CEO. A construction engineer by training, he has extensive experience in technology innovation and leadership. Before Carbon Re, Sherif led the AI for climate practice at Element AI and co-founded Amnesty Tech. He has a BSc from the Americana University in Cairo and an MPA from Harvard Kennedy School.