Accelerating Decarbonisation in India’s Steel Industry: The Challenges, the Tools and the Solutions
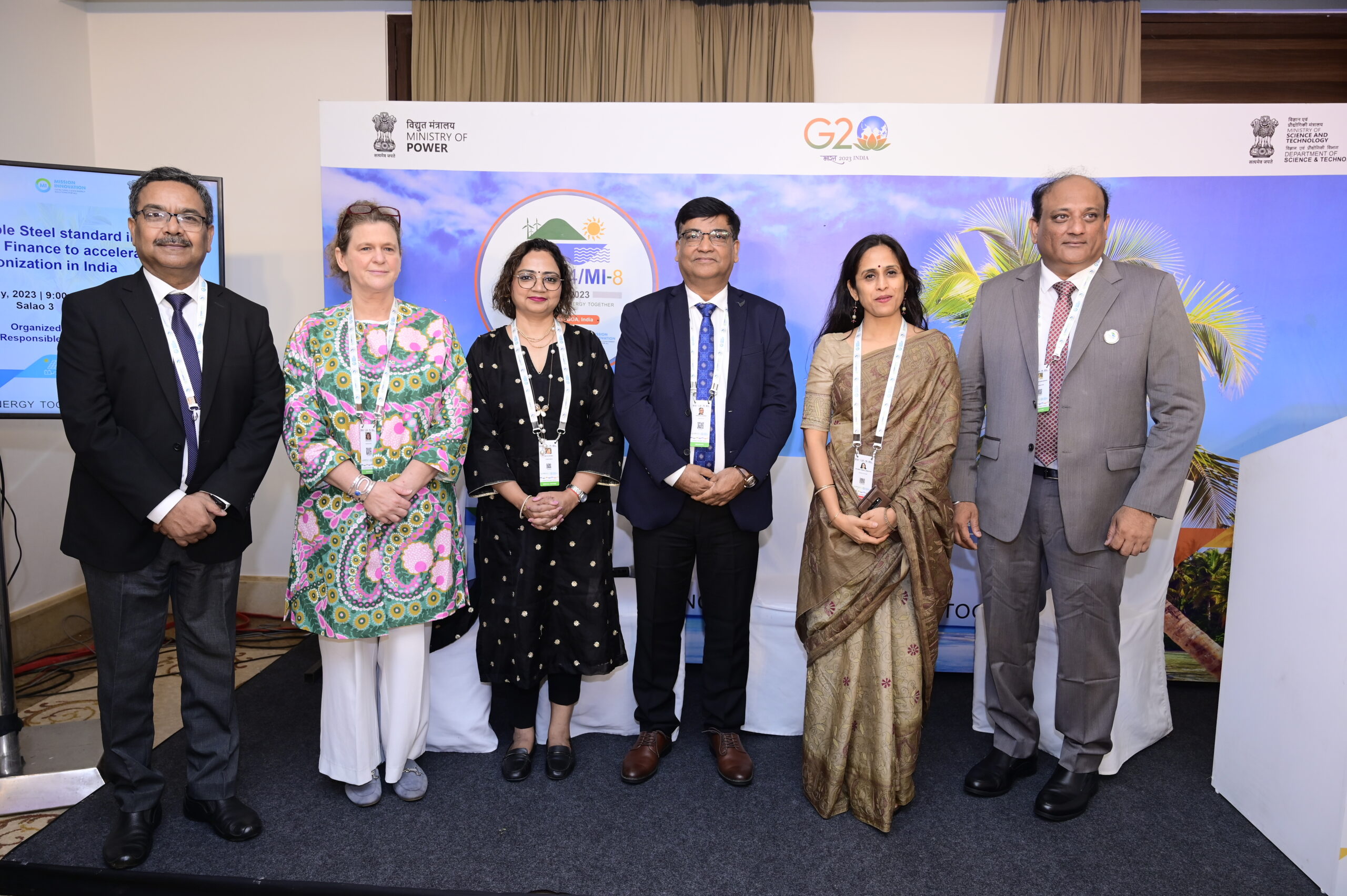
Now the most populous country in the world, India is also the second-largest producer of steel after China. According to the IEA, the Indian steel industry is projected to triple by 2050, making it the fastest-growing steel economy globally (IEA, Iron and Steel Technology Roadmap, 2020). The majority of India’s steel is used for domestic consumption – for infrastructure, transport, construction and consumer goods. Whether in airports or railway stations, steel use is increasing across India, and meanwhile, the expansion of renewable energy in the country, which also requires vast amounts of steel, is racing ahead at breakneck speed. This unprecedented growth in steel consumption is a vital part of India’s economic story.
But the steel industry also accounts for around 12% of India’s emissions, far more than the global average of 8%. So the country’s push to meet its net zero target by 2070 will rely heavily on the decarbonisation of its steel sector. Currently, almost half of Indian steel is produced via the traditional blast furnace route with the remaining being split between smaller less efficient induction furnaces and electric arc furnaces. Enormous efforts to decarbonise are already being made. Since 2005, emissions per tonne of crude steel in India have been reduced from around 3.1 tonnes to 2.5 tonnes. But the sheer amount of resources needed to accelerate decarbonisation remains huge.
There are many challenges. The lack of a transition fuel such as natural gas to accelerate the phase-out of coal is a significant issue. What is more, the use of the lower-grade iron ore found in India requires more energy for reduction. And while countries with long histories of producing and consuming steel – and all the associated emissions – now have the luxury of large stocks of scrap, India’s access to scrap is extremely limited today. A far more comprehensive plan is needed to reimagine the entire industry.
Deep thinking on the solutions is clearly happening within government. The Indian Ministry of Steel recently set up 13 task forces to investigate the policies needed to tackle the decarbonisation challenge from multiple angles: to improve energy and material efficiency, to enable the transition to renewable energies, to price carbon emissions, to stimulate green finance and, underpinning all these, to define the embodied emissions of steel.
Major steel companies are working to decarbonise at pace. Jindal Steel and Power has already committed to net zero by 2047, Tata Steel by 2045, and JSW by 2050. All of these are well ahead of the national 2070 target. But these ambitious targets require equally ambitious and comprehensive decarbonisation plans which will also accommodate rapidly expanding demand. To accommodate the steel growth foreseen in the Indian economy, the government is projecting a doubling in steel capacity by 2030, and much of the planning for this so far is via the traditionally emissions-heavy blast furnace route. Herein lies the challenge. Such companies will need to demonstrate how their new blast furnace investments can align with their net-zero targets. Investors are increasingly looking for transition roadmaps.
Whilst Indian steel companies may understand the technologies needed to reduce emissions, the processes are vastly more expensive, and so they need to see a clear business case: signals that their customers are ready to pay the premium on lower-emissions steel; facilitative policies from government to reduce costs and market incentivisation for technologies available in the near term; an effective price on carbon; preferential finance for decarbonisation projects. Such measures may all form part of steel company roadmaps to net zero.
Last month, as part of the 14th Clean Energy Ministerial in Goa, ResponsibleSteel brought together key stakeholders from the steel industry, downstream market, and government to discuss the role of the ResponsibleSteel International Standard in impacting policy, finance and the energy transition to accelerate decarbonisation in India’s steel industry at pace and scale. The event featured keynotes from the Secretary to the Ministry of Steel, the Secretary General and Executive Head of the Indian Steel Association, and ResponsibleSteel’s CEO. ResponsibleSteel also hosted a panel discussion on the challenges and solutions needed to achieve an equitable and just transition between representatives from the Ministry of Steel, JSW Steel and SteelZero. What’s clear is that to accelerate decarbonisation in India at scale and at speed, we need to share learning and build skills, not only to maximise scrap recovery but to drive demand and finance for low-emissions primary steelmaking on a vast scale.
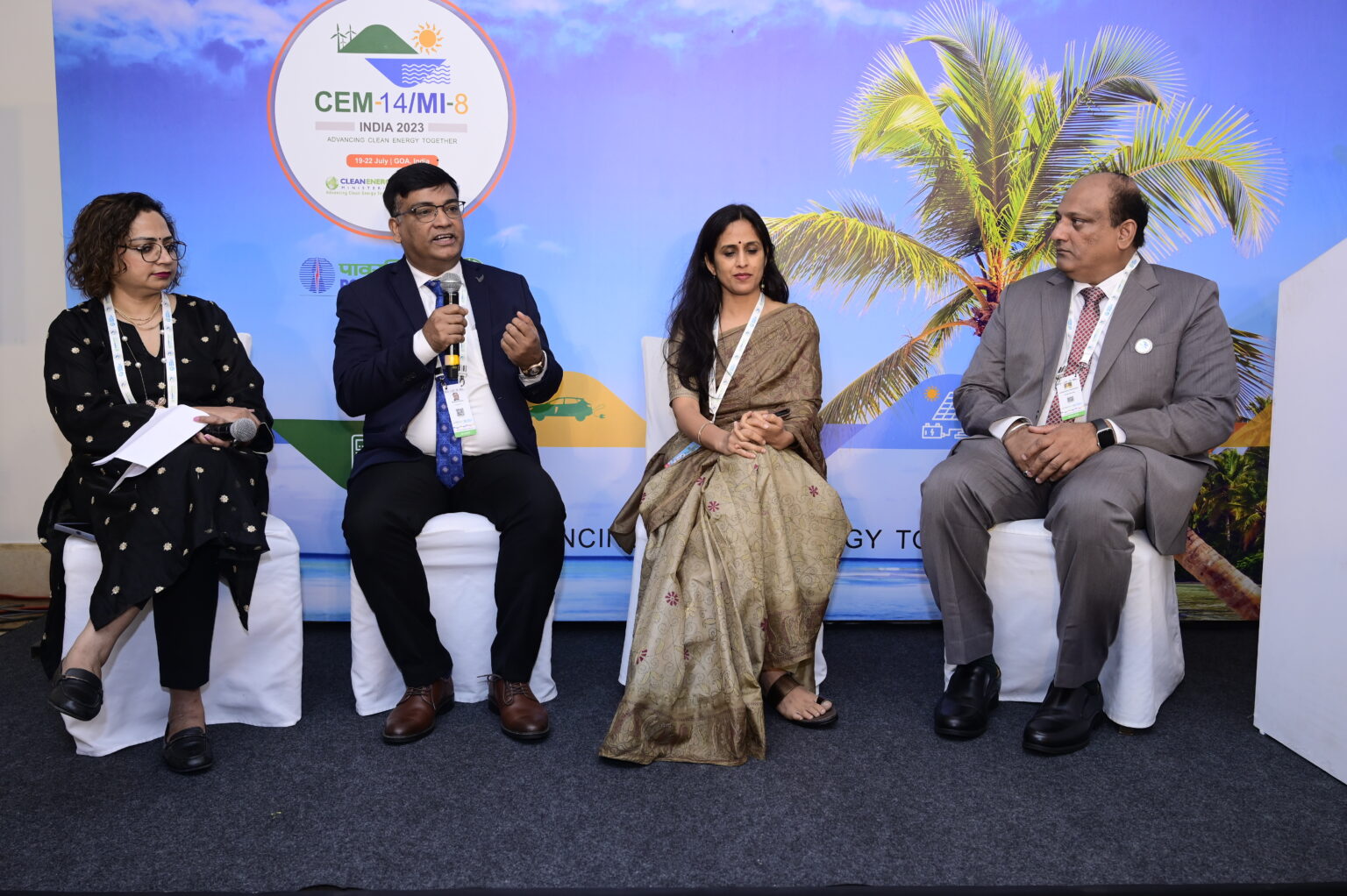
This means clean energy at scale. India has already made rapid progress on renewable electricity, reaching a capacity of 168 GW in the last ten years. The Indian government has targeted 50% renewable electricity by 2030, with an unparalleled 50GW a year in the pipeline over the next five years – more than the US or Europe installed in 2022. There is also a lot of talk on green hydrogen. The Indian government aims to have 5 million tonnes by 2030. Both the achievements to date and the plans ahead are inspiring examples of ambitious government strategy.
But whilst renewable energy is core to the decarbonisation roadmap for steelmaking in India, the shift to green hydrogen in India is complex due to the limited reserves of natural gas as a transition fuel. In the meantime, alternative ways of thinking are emerging to avoid a costly wholesale switch to H2 based DRI before green hydrogen is available. Tata Steel has recently demonstrated the 24/7 injection of hydrogen in the blast furnace as a reductant and believes this could deliver a 15% to 20% reduction in CO2 emissions. With additional capital expenditure, the potential is as much as 30% or, some say, even more.
The industry has also shown promising progress on carbon capture from coal used in the blast furnace as an intermediate technology that can divert vast volumes of carbon emissions and produce methanol. Currently, pilots are demonstrating the potential to deliver 15-20% emissions reduction, with the potential thought to be higher. At present, however, the costs involved prevent it from being scaled as a viable source of methanol. Improving efficiencies in the processing of input materials is another element under development, with innovations emerging to enable lower-grade iron ores to be used directly for reduction without need for sintering, for example.
Efforts to maximise the use of scrap are also underway. JSW and Tata Steel have invested in scrap collection after policies were introduced in recent years to mandate the end-of-life recycling of vehicles and facilitate the growth of metal scrapping centres in India.
Finally, development of carbon capture and storage technology is hampered by high costs, a lack of market incentives and a lack of concerted research and development. The potential for CCS in India has been subject to geological uncertainties, and yet the outlook may be more promising than once thought. For instance, basalts can mineralise captured carbon for effective and permanent storage. A recent study showed India has one of the largest onshore basalt formations in the world, and around 360GW CCS capacity in both basalts and deep saline formations, excluding no-go and densely populated areas (CEEW, 2023). Meanwhile, India’s annual emissions today are just over 3GW.
But underpinning all of this is the need for a common language for steel decarbonisation within countries and between countries. We need a consistent method of measuring and defining near-zero steel that is effective in driving down emissions globally. As Shri Nagendra Nath Sinha, Secretary for the Indian Ministry of Steel, stated, “It has to be clear, it has to be credible and it has to be standardised.” This is why ResponsibleSteel’s work is so critical. For Prabodha Acharya, JSW’s Chief Sustainability Officer, “Many customers are asking about green steel, and I don’t know what they mean by green steel, but when they ask for ResponsibleSteel we have a definitive standard… This is going to be the gold standard.”
It also has to be equitable. The ResponsibleSteel International Standard takes the approach of a ‘scrap variable scale’ to define decarbonisation progress levels. To incentivize decarbonisation in a way that is both effective and fair globally, not only in countries with the luxury of high scrap stocks. To avoid a commercial ‘race for scrap’ with no net gain for the climate, rather than encouraging the decarbonisation of steel production across the board and particularly from iron ore. To drive the entire global industry to net zero.
As ResponsibleSteel’s CEO Annie Heaton remarked, “We need to rise above the interests of individual companies, of individual countries, and individual technologies to drive decarbonisation at a global level.” Shri Alok Sahay, Secretary General & Executive Head of the Indian Steel Association, believes ResponsibleSteel plays a vital role in creating a more equitable system. “To decarbonise, it’s vital that we foster partnerships. ResponsibleSteel can bring everyone together, and help build a level playing field.”
You can watch a recording of ResponsibleSteel’s event at the Clean Energy Ministerial here.